Kesme uçları ve çıkıntılar. Kesicilerin tasarım özellikleri. Alttan kesme için kesme koşulları
Genellikle uçlar ve çıkıntılar, çentik kesicilerle torna tezgahlarında kesilir.
Şek. 137, bir gösterilir kesici. Genellikle parçanın kesme yüzeyine yaklaşık 5 ° açıyla ayarlanmış uzun bir kesme kenarına 1 ve kısa bir kesme kenarına 2 sahiptir. merkezlerde keserken parçanın merkezi (Şek. 137, b, c).
Makinenin merkezi tarafından sınırlandırılmayan uçları, omuzları ve çıkıntıları kırparken, Şekil 2'de gösterildiği gibi kesiciler kullanılır. 138. Bu kesiciler hem boyuna hem de enine beslemelerle çalışabilir. Ulaşılması zor yerlerde uçları veya çıkıntıları kesmek için, örneğin kesiciyi kartuşa yaklaştırmanız gerektiğinde, bükülmüş kesiciler kullanın (Şek. 139). Aynı amaçlar için, enine beslemeden haberdar olan bükülmüş kesiciler sıklıkla kullanılır (Şekil 140).

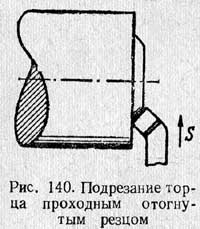
Uçları ve çıkıntıları düzeltirken, kesicinin ucu tam olarak merkezlerin yüksekliğine ayarlanmalıdır. Kesici merkezin altına ayarlanırsa, sağlam ucun ortasında kesilmemiş bir çıkıntı kalacaktır. Merkezin üzerine yerleştirilmiş bir kesici kırılabilir.
Küçük yükseklikteki çıkıntılar da bir çentik ile kesilebilir sert kesici silindirik bir yüzeyin döndürülmesiyle aynı anda uzunlamasına besleme ile (Şek. 138). Çıkıntının bu kesme yöntemiyle doğru konumu tamamen kesicinin kurulumuna bağlıdır, kesici kenarı parçanın eksenine kesinlikle dik olmalıdır.
Büyük yükseklikteki çıkıntıların işlenmesi genellikle uzunlamasına ve enine beslemeyi birleştirerek birkaç geçişte gerçekleştirilir. İlk olarak, silindirik bir bölümü işlemek için çıkıntı yüzeyine 5°'lik bir açıyla ayarlanmış bir çentik kesici kullanılırken, her uzunlamasına geçiş için 2-3 mm'lik bir tabaka çıkarılır. Daha sonra aynı kesici ile çıkıntı, merkezden çıkıntının dış yüzeyine doğru yönlendirilen bir besleme ile kesilir.
2. Uçları ve çıkıntıları kesme teknikleri
Uçları ve çıkıntıları keserken, parçalar uzunlamasına tornalama ile aynı şekilde kurulur.
Kırpma merkezlerde biter. Merkezlere monte edilen parçaların uçlarını keserken, monte edilmesi tavsiye edilir. punta Lafta yarı merkez(bkz. Şekil 137, b), ucun tamamının kesilmesini sağlar. Emniyetli (çift) konili merkez delikleri kullanmak daha da iyidir (Şek. 137, c). Her iki durumda da besleme yönü çevreden merkeze doğrudur.
Mandrendeki uçların kırpılması. Kartuşlara sabitlenmiş parçaların uçlarının bir çentikle değil, bükülmüş bir kesici ile kesilmesi önerilir (bkz. Şekil 140). İkincisi, daha yüksek kesme koşullarına izin veren daha büyük bir kesme parçasına sahiptir.
Uçları ve yüksek çıkıntıları keserken, besleme yönü dış yüzeyden merkeze (Şek. 141, a) veya merkezden dış yüzeye (Şek. 141, b) gidebilir. İkinci durumda, kesiciye etki eden kuvvet, kesici kenarını parçanın uç yüzünden uzağa itme eğilimindedir. Bu, parçanın dış yüzeyinden merkezine yönlendirilen bir besleme ile çalışmaya göre daha temiz bir uç yüzey sağlar. Bununla birlikte, uçları ve çıkıntıları kesmeye yönelik bu yöntem, parçanın diğer yüzeylerine göre bir test talaşından sonra ucun veya çıkıntının tam konumunun kontrol edilmesine izin vermez. Bu nedenle, enine besleme yönünün seçimine ilişkin yukarıdaki kural bazen terk edilmelidir.
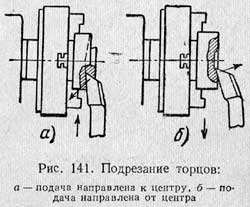
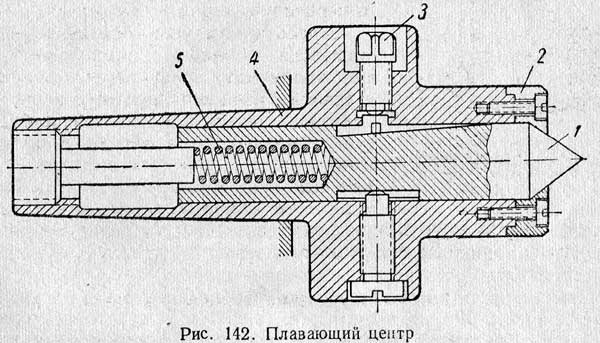
Yüksek performanslı çalışma yöntemleri. Çıkıntılı önemli sayıda aynı parçayı keserken, kaliperin hareketini sınırlayan bir durdurma ile birlikte uzunlamasına besleme kullanılmalıdır (bkz. Şekil 131).
Merkez deliklerin derinliği ne olursa olsun, tek tek adımların uzunluklarına dayanmak gerektiğinde, başarıyla kullanılırlar. yüzen merkezler(Şek. 142).
Muhafazanın (4) içine monte edilen böyle bir merkez (1), mesnetli milin konik deliğine sokulur. Yay 5, merkezi sağa doğru bastırma ve merkez ile parça arasında temas oluşturma eğilimindedir.
Merkezlere takılan parça, punta ucuna basıldığında, gövdenin 4 ucuna takılı sertleştirilmiş bir dayanağa 2 getirilir. Bundan sonra, yüzer merkez, bu işlemin süresi boyunca bir cıvata 3 ile kilitlenir. Bölüm. Bir sonraki parçayı takarken cıvata 3 serbest bırakılmalıdır.
Yüksek hızlı tornacı Yoldaş Kulagin, delikli bir parçanın ucunu keserken (bkz. Şekil 143), aynı anda iki kesici 1 ve 2 kullanır.Bu kesiciler, aynı çıkıntı ile özel bir tutucuda 3 sabitlenir, bu da sırayla takım tutucu 4'e sabitlenmiştir. Kesici 2 dış çaptan ucu keser ve kesici 2, kesici kenar aşağıda olacak şekilde takım tutucuya takılır. İki kesicinin aynı anda işlenmesi nedeniyle, işleme uzunluğu ve dolayısıyla işlem süresi 2 kat azalır. İki kesici aynı anda çalıştığında çıkıntı olmadan pürüzsüz bir uç elde etmek zor olduğundan, ucun bu şekilde kesilmesi yöntemi kaba işleme için önerilebilir.
Uçları ve çıkıntıları ölçme yöntemleri. Uç yüzeyin düzlüğü, uç yüzeye uygulanan bir cetvel (Şekil 144) kullanılarak kontrol edilebilir. Bir boşluk varsa, boyutunu gözle veya özel bir ölçüm plakası probu ile belirleyebilirsiniz.
Çıkıntıların şaftın uzunluğu boyunca doğru konumu bir cetvel (Fig. 145, a), bir iç mastar (Fig. 145, b) veya daha kesin olarak bir derinlik mastarı (Fig. 145, c) ile kontrol edilir. Doğru bir kontrol için Büyük bir sayı aynı parçalar, şablonların kullanılması önerilir (Şek. 146).
3. Alttan kesme için kesme koşulları
Uçları ve çıkıntıları enine besleme ile kırparken, kesme derinliği kaldırılan tabakanın kalınlığıdır ve ilerleme, parçanın bir devri başına kesicinin enine yönde hareket miktarıdır.
Alttan kesme sırasında aşağıdaki çapraz beslemeler önerilebilir:
için kaba işleme- 2 ila 5 mm kesme derinliğinde 0,3 ila 0,7 mm/dev;
için Bitiricilik- 0,7-1 mm kesme derinliğinde 0,1 ila 3 mm/dev.
Uçları düzeltirken, dış silindirik yüzeyin işlenmesiyle aynı kesme hızı kullanılabilir, ancak daha büyük çapla hesaplanmalıdır.
4. Uçları ve çıkıntıları keserken evlilik ve bunu önlemek için önlemler
Uçları ve çıkıntıları keserken, aşağıdaki evlilik türleri mümkündür:
1) ucun veya çıkıntının yüzeyinin bir kısmı işlenmemiş olarak kaldı;
2) parçanın uzunluğu boyunca alttan kesme ucunun veya çıkıntının yanlış konumu;
3) çıkıntının parçanın eksenine dik olmayan konumu;
4) uç veya çıkıntının yüzeyinin yetersiz temizliği.
1. Birinci tipin evliliği, yanlış iş parçası boyutları, küçük işleme payı, yanlış montaj ve parçanın aynaya yanlış hizalanması, kesicinin parçanın uzunluğu veya merkezlerin yüksekliği boyunca yanlış montajı nedeniyle elde edilir. .
Böyle bir evlilik genellikle kurtarılamaz, ancak iş parçasının boyutlarını kontrol ederek, işleme payını artırarak, parçanın ve kesicinin doğru montajını kontrol ederek önlenebilir.
2. Kesik ucun veya çıkıntının uzunluk boyunca yanlış konumu, kesicinin yanlış takılması veya kendinden tahrikli tabancanın (uzunlamasına besleme ile) zamansız kapatılması ve ayrıca aynadaki parçanın eksenel olarak yer değiştirmesi ile elde edilir. Yetersiz güçlü sabitlemesinin bir sonucu. Aynı zamanda çıkıntının sınırı aşılırsa, bu tür bir evlilik onarılamaz. Kesicilerin kurulumunu ve parçanın kartuşa sabitlenmesinin gücünü ve ayrıca uzunlamasına besleme ile çalışırken kendinden tahrikli tabancanın zamanında kapanmasını kontrol ederek böyle bir evliliği önleyebilirsiniz.
3. Enine besleme ile çalışırken ucun veya çıkıntının parçanın eksenine dik olmayan bir konumu, kaliper kılavuzlarındaki yanlışlıklardan ve ayrıca gevşek sabitlemesi nedeniyle kesicinin preslenmesinden kaynaklanabilir. takım tutucuda, çok küçük kesici bölüm, kilitli değilse arabanın ayrılması. Boyuna besleme ile çalışırken, yaygın bir neden yanlış kesici ayarıdır. Bu tür evlilikler, listelenen nedenler ortadan kaldırılarak önlenebilir.
4. Uç veya omuz yüzeyinin yetersiz temizliği, aşırı besleme, kesicinin büyük çıkıntısı, kesicinin veya parçanın yeterince güçlü bir şekilde tutturulmaması, kesicinin yanlış bilenmesi, kesicinin önemli ölçüde körelmesi, metalin yüksek viskozitesi nedeniyle elde edilir. işlenmekte, şaryo veya kaliper parçalarının titremesi, mil veya aynanın titremesi veya salgısı.
Böyle bir evliliği, buna neden olan sebepleri zamanında ortadan kaldırarak önleyebilirsiniz.
sınav soruları 1. Puanlama kesicinin tasarım özellikleri nelerdir?
2. Puanlama kesiciler nasıl kurulur?
3. Çıkıntıları kesmenin yolları nelerdir?
4. Yan beslemeli omuz kesimi için kesici nasıl ayarlanır?
5. Parçaları merkezlere takarken uçların kırpılması nasıl oluyor?
6. Aynaya parçalar takarken uçların kırpılması nasıl oluyor? Ne tür kesiciler kullanmak uygundur?
7. Çıkıntıları keserken, uçlarda yüksek performanslı çalışma yöntemleri hakkında bize bilgi verin.
8. Uç keserken kesme derinliğine ne denir?
9. Kesilen ucun doğruluğu nasıl kontrol edilir?
10. Uçları ve çıkıntıları keserken evliliğin ana türlerini ve nedenlerini belirtin; önlemek için önlemler.
Çoğu tornalama işlemi kesiciler ile yapılır. Ana tipler arasında kesici takım, kullanım sıklığı açısından lider konumdadır. Özel sertlikte özel kalite çelikten yapılırlar.
Kesici takımın amacı
Operasyon türüne bağlı olarak, ana kesici diş türleri kullanılır:
- dış ve iç kesim için dişli;
- düz, eğik ve kalıcı geçiş yoluyla;
- kör ve açık delikler için sıkıcı;
- kesme.
Torna kesme aletleri, küçük çaplı bir çubuktan bir parçayı kesmek ve iş parçasında oluklar oluşturmak için kullanılır. Özel amaçlar için kesici aletlerle kesilirler - kanal açma. Çalışma kafasının şekli, gelecekteki oluğun boyutuna ve şekline karşılık gelir. Genellikle tek geçişte oluk doğru beden yapamıyor. Birkaç geçişte, sert metallerle ve ayrıca geniş bir oluk genişliğiyle çalışırlar.
Çalışma alanının uzunluğu, kesilen parçanın çapının yarısından biraz fazla olmalıdır.
Kesici takımların tasarım türleri:
- katı: tek bir metal parçasından işlenmiş. Takım karbon çeliğinden, küçük olanlar yüksek hızlı kesme çeliğinden yapılmıştır. Pratikte yaygın olarak kullanılmaz;
- kaynaklı bıçaklarla: kafaya bir karbür veya yüksek hızlı bıçak kaynaklanır. Kaynak yaparken, teknolojiyi takip etmek önemlidir, aksi takdirde çatlaklar ortaya çıkar, alet hızla çöker;
- eklerin mekanik olarak sabitlenmesi ile: aletin kafasına bir kesici uç yerleştirilir ve mekanik olarak sabitlenir. Genellikle mineral seramik kesici uçlar için kullanılırlar.
Torna kesiciler sola ve sağa, düz veya bükülmüş olabilir. Pratikte en yaygın olanı sola eğik ve sağ düzdür.
Kesme bıçağı tasarımı
Hiç dönüm aracı bir gövde ve çalışan bir kafadan oluşur. Kesimin özelliği, başının çekilmesidir, yani genişliği vücudun genişliğinden daha az olmalıdır. Kenarın uzunluğu, boşluğu kesmek için uygun olacak şekilde olmalıdır. İşlevsel parçanın sertliği küçük olduğundan ve talaşların çıkarılması zor olduğundan, kesme kesiciler büyük bir yüke maruz kalır. Kafaların kalınlığı oldukça küçüktür, bu nedenle, güçlerini korumak için açılar yaklaşık 1 - 3 derece (arka ve planda) alır. Bu şekil nedeniyle alet yanlış takılırsa veya kötü giyilirse sürtünme önemli ölçüde artar.
Bu nedenle, tornalama işlemi sırasında karbür uçlu kesici takımlar genellikle parçalanır, kesici kenarlar ufalanır ve lehimleme ortadan kalkar.
Çalışma kafasında aşağıdaki bölgeler ayırt edilir: kesici kenar (ana ve yardımcı), başın üstü, başın ön yüzeyi ve bir çift arka. Kesici kenar, bir kama şeklinde yerleştirilmiş ve bilenmiştir. Gövde veya gövdenin amacı, aleti el aletine monte etmektir.
Yüksek kaliteli kesim ancak düzgün bilenmiş bir kesici aletle yapılabilir. Açıların doğru tanımlanması için aşağıdaki kavramlar kullanılır:
- ana düzlem: bu, boyuna ve enine düzlemlerde beslemeye paralel, referans düzlemi ile hizalanmış bir yüzeydir;
- kesme düzlemi: iş parçasının yüzeyine teğet, çalışma kenarı boyunca geçer.
Aşağıdaki açılar karşılanmalıdır:
- talaş açısı: talaşların metal boşluktan ne kadar kolay çıkarılacağını ve ne kadar iyi kesileceğini belirler;
- Büyük Boşluk Açısı: Bu, kesici yüzeyi ile torna düzlemi arasındaki açıdır. Ne kadar keskin olursa, kesicinin arka yüzeyi o kadar güçlü kütüğe sürtünür;
- koniklik açısı: ön ve arka ana yüzeyler arasında. Ne kadar küçük olursa, metali kesmek o kadar kolay olur. Ancak kesme yüzeyi daha hızlı aşınır, parçalanır.
Çalışma kafasının tutucu ile sabitlenmesinin güvenilirliğini arttırmak için, eğimli plaka, açı şeklinde yapılmış bir dile lehimlenmiştir. Bu nedenle, oturma alanları artar ve dilin kenarları, kesici ile çalışma sırasında ortaya çıkan kuvvetlerin etkisi altında plakanın yana hareket etmesine izin vermez.
Ayrıca, başın yüksekliği çubuğun uzunluğunu aşmalıdır.
İş parçasını keserken, alet malzemenin tüm kalınlığını kesmez, çünkü belirli bir aşamada parça kırılır ve ortada bir çubuk parçası bırakır. Uç parçayı bitirmek gerektiğinde, ana çalışma kenarı 75 - 80 derecelik bir açıyla bilenir, diğer durumlarda bu açı 90 derecedir.
Uygulamada, torna takımları genellikle planda 60 - 80 derece keskinleştirilmiş simetrik bir çalışma kenarı kırılmış olarak kullanılır. Bu pansuman sayesinde takım malzemeye daha kolay girer, talaş kaldırma işlemi kolaylaşır ve kesici çıkma olasılığı azalır. Bunun için 90 derecelik bir açıyla, her iki tarafta da 1,5 mm boyutuna kadar 45 derecelik bir açıyla pahlar seçilir.
Kesicinin takılması
Takım, merkezinde işlenen iş parçasına 90 derecelik bir açıyla yerleştirilmiştir. Bir milimetrelik kesir farkı, kesicinin kırılmasına neden olur.
Kırılgan metalleri tornalarken, kesici 10 dereceye kadar bir açıyla tutulur. Aksi takdirde, iş parçası torç merkeze ulaştığından daha hızlı kırılacaktır. Katı metalden yapılmış yüksek hızlı aletlerle çalışırken, 30 m/dakika'dan fazla olmayan işleme hızına dikkat etmek gerekir. Tungsten karbür kesiciler, dakikada 130 metreye kadar yüksek hızlarda çalışır.
Kesme kesici ters çevrilmiş
Özellikle düşük devirli ve zayıf amatör makinelerde zor kesim işleri teknik özellikler. Standart bir kesme kesiciyi keskinleştirebilirsiniz, ancak bu iş uzun ve özenlidir, alet oldukça kırılgan olacak ve işte aşırı hassasiyet gerektirecektir.
Bu sorunu çözmek için ters çevrilmiş kesicinin tasarımı icat edildi. Bunlar, değiştirilebilir karbür çelik uçlara sahip aletlerdir. İleri ve geri dönüş için kullanılabilirler. Ayrıca, bu aletin ana modu ters dönüştür, talaşlar engellenmeden ayrıldığında, çalışma alanından çıkarılması kolaydır, sıkışma daha az görülür.
Tasarım, takılabilir bir üçgen ve kesme plakalarının T şeklinde bir profili yardımıyla kesicinin yüksekliğinin ayarlanmasını sağlar. Bu şekil, malzemeye nüfuz etme sırasında sürtünmeyi azaltır. Kit genellikle plakaları kesmek için 4 - 5 seçenekle gelir. Uzunluk izin verdiği sürece birçok kez keskinleştirilebilirler.
Kesme plakasının geniş çıkıntısı çok uygundur, kalın iş parçalarının kesilebilmesi sayesinde çalışma sırasında yağlanması tavsiye edilir. Araç, özellikle düzlemler arasındaki temas noktalarında dar olukları örneklemek için iyidir.
Kesiciler sınıflandırılır:
besleme yönünde - sağa ve sola (sağ kesici dişler torna sağdan sola beslerken çalışırlar, yani makinenin mesnetine hareket ederler);
başın tasarımına göre - düz, bükülmüş ve çizilmiş (Şekil 4);
Pirinç. 5.4. Kesici dişler: a - düz, b - bükülmüş, c - çekilmiş
alet malzemesinin türüne göre - yüksek hız çeliğinden, sert alaşımdan vb.;
üretim yöntemine göre - katı ve kompozit olarak (pahalı kesme malzemeleri kullanıldığında, kesiciler kompozit yapılır: kafa alet malzemesinden yapılır ve tutucu yapısal karbon çeliğinden yapılır; lehimlenmiş sert alaşımlı plakalara sahip kompozit kesiciler veya mekanik olarak bağlananlar en yaygın olarak kullanılır);
tutucunun enine kesitine göre - dikdörtgen, yuvarlak ve kare; işleme türüne göre - açık delik, çentikleme, kesme, oluklu, delik açma, şekilli, diş açma vb. için (Şekil 5).
Pirinç. 5.5. Çeşitli işleme türleri için tornalama kesiciler:
a - kavisli geçiş kesici ile dış tornalama,
b - düz kesici ile dış tornalama,
c - çıkıntıyı dik açıyla keserek döndürme,
g - bir oluk kesmek,
e - yarıçap filetosunu döndürmek,
e - sıkıcı delikler,
g, h, i - dış, iç ve özel diş açma
Kesici açıları atamak için temel kurallar
Ana kabartma açısı , kesicinin arka yüzeyinin parçanın kesme yüzeyindeki sürtünmesini azaltmak için bilenmiş. Artması ile bu yüzeyler arasındaki temas alanı ve buna bağlı olarak sürtünme kuvveti azalır. Bununla birlikte, 'de belirli değerlerin ötesinde bir artış, koniklik açısında bir azalmaya, kesicinin kesme kamasının zayıflamasına ve sonuç olarak mukavemetinde bir azalmaya yol açar. Buna karşılık, kesme kamasının masifliğinin azalması, kesme sıcaklığında bir artışa ve buna bağlı olarak takım ömründe bir azalmaya neden olur.
Bu nedenle, ana arka açının değeri, aynı anda iki çelişkili koşulu karşılamalıdır. Önerilen açılar Tablo 5.1'de gösterilmiştir.
Yardımcı arka açı 1 aynı hususlara göre atanır ve genellikle açısına eşittir veya 1 ... 2 ° daha azdır.
Tablo 5.1
Kesici boşluk açısı değerleri
çeşitli işleme türleri ile
Ana talaş açısı , talaş kesmeyi kolaylaştırmak için keskinleştirilmiştir. Artması ile kesme tabakasının plastik deformasyonları ve kesme kuvvetleri azalır ve talaşların ön yüzey boyunca hareketi de kolaylaşır. Bu açıdan bakıldığında, eğim açısının 45°'ye yakın ayarlanması arzu edilir. Ancak açısındaki böyle bir artış, koniklik açısında bir azalmaya neden olur ve kesicinin kesme kamasını zayıflatır ve yukarıda belirtilen sonuçlara yol açar.
Bu bağlamda, 45°'ye yakın ön açılar yalnızca düşük mukavemet özelliklerine sahip malzemeler işlenirken atanabilir. Yüksek mukavemet özelliklerine sahip malzemeler için en büyük eğim açıları atanır. Karbür uçlarla donatılmış kesicilerin ana talaş açılarının aşağıdaki değerleri önerilir (tablo 5.2):
Tablo 5.2
Kesici dişlerin ana ön açılarının değerleri
karbür uçlar ile
Not: HSS penalarında açılar yaklaşık 5° artırılır.
Ön açının olduğunu görmek kolaydır. > 0, kesicinin kesme kamasının zayıflamasına yol açar. Bu nedenle, kesicinin büyük dinamik yüklere maruz kaldığı durumlarda mukavemetini artırmak gerekir. Bu, negatif eğim açıları kullanılarak elde edilir (< 0). В результате увеличивается массивность режущего клина и изменяется характер деформаций, которые он испытывает: изгиб заменяется сжатием. Поэтому в случае обдирочного точения с большими глубинами резания и динамическими нагрузками на резец передние углы назначают отрицательными в пределах -5…-15°.
Giriş açısı , takım ömrünü ve yüzey kalitesini önemli ölçüde etkiler. Artması ile kesme kamasının kütlesi azalır ve ana bıçaktan ısı transferi koşulları kötüleşir. Bu nedenle, direnç açısından, açısının küçük ayarlanması arzu edilir.
Bununla birlikte, bu genellikle, çoğunlukla kademeli olan parçaların konfigürasyonu ile önlenir. Ek olarak, küçük açılarında kuvvetler artar R de ve takım tezgahı-alet parçası (AIDS) sistemindeki titreşimler güçlendirilir. Bu nedenle, küçük açıların kullanılması ancak aynı çaptaki parçaları sert bir AIDS sistemi ile döndürürken mümkündür. Normal koşullar altında, giriş açısı, parçaların konfigürasyonu tarafından belirlenir ve 45°, 60° veya 90°'ye eşittir.
Yardımcı boşluk açısı 1 takım ömrü ve yüzey kalitesi üzerinde giriş açısı ile aynı etkiye sahiptir. açısı esas olarak takım ömrüne ve parçanın konfigürasyonuna göre atandığından, 1'in işlenmiş yüzeyin finişi üzerinde ana etkiye sahip olduğunu varsayabiliriz. Açı ne kadar küçükse 1 , işlenmiş yüzeyin mikro profil pürüzlülüğünün yüksekliği ne kadar düşükse. Kaba işleme ve ince talaş işleme kesicileri için bu açının önerilen değerleri 10…15°'dir. Daha yüksek bir yüzey kalitesi elde etmenin gerekli olduğu durumlarda, bu açı 3 ... 5 ° 'ye düşürülür ve bazı durumlarda 1 açı ile 3 ... 5 mm uzunluğunda bir yardımcı bıçak bilenir. = 0 (yenilikçi V. Kolesov tarafından keski).
Ana bıçağın eğim açısının talaş akış yönü ve takım ömrü üzerinde önemli bir etkisi vardır. Pozitif, negatif veya sıfır olabilir (Şekil 5.6).
Pirinç. 5.6. Ana bıçağın eğim açısının talaş akış yönü üzerindeki etkisi
Pozitif açılı kesici dişler için çip işlenmiş yüzeye doğru saptırılır. Yankı yönü şu durumlarda uygundur: ön arıtma koşulları. Negatif açılı kesicilerde talaşlar işlenmiş yüzeye doğru sapar. Bu yön, son işlem için en uygunudur, çünkü bu durumda işlenmiş yüzey çizilmeye karşı korunur. .
Pozitif değerdeki bir artışla kesme kamasının mukavemeti artar ve ısı giderme koşulları artar. Önerilen açı değerleri tablo 5.3'te verilmiştir.
Ana bıçağın eğim açılarının değerleri
Tablo 5.3
Pozitif ve negatif açılarında, kesicinin kesme kaması keskinleştirilir, bu da çok küçük kesme derinliklerinde çalışmayı mümkün kılar. t= 0,01 ... 0,02 mm, bu da son işlem için çok önemlidir.
Takım ucu yarıçapı r c = 0,1…0,5 mm. İşleme koşullarına ve işlenen yüzeyin kalitesine göre seçilir.
Parfenyeva I.E. YAPI MALZEMELERİ TEKNOLOJİSİ. M.: Çalışma kılavuzu, 2009
4. Tornalama türleri. Ana tornalama aletleri türleri. Torna takımının elemanları ve geometrik parametreleri.
4.1. Tornalama türleri
Torna tezgahlarında ve özellikle vidalı torna tezgahlarında aşağıdaki çalışma türleri gerçekleştirilebilir: merkezlerde, aynada ve ön plakada tornalama; sıkıcı; yüz çevirme; kesme ve kırpma; iplik kesme; uygun araç ve gereçler kullanarak konileri, şekillendirilmiş yüzeyleri ve diğer işleri tornalamak.
Yüzey işleme, boyuna veya enine besleme ile gerçekleştirilir. Uzunlamasına besleme ile işleme sırasında yüzeylerin şekillendirilmesi, enine besleme ile işleme sırasında izleme yöntemine göre gerçekleştirilir - esas olarak kopyalama yöntemine göre.
Merkez tornalama
Uzunluğun çapa oranı olan çubuk parçalar (miller, akslar) genellikle merkezlerde boylamasına kesiciler kullanılarak boyuna tornalamaya tabi tutulur. Uçlarında delinmiş eksenel deliklere sahip bir parça, mesnet ve punta merkezleri arasında kenetlenir. Başlığın merkezi iş miline, arkası ise punta uçlarına takılıdır. Parçanın bir ucunda, parmak sürücü ön yüzünün yuvasına girecek şekilde bir vida ile bir kelepçe sabitlenir. Ön yüz plakası, milin ön ucuna vidalanmıştır.
Uzun parçaları işlerken, onları sapmadan korumak için kılavuz cihazlar - lunetler - kullanılır. Lunette sabit (yatak raylarına monte edilmiş) ve hareketli (kaliper taşıyıcıya monte edilmiş ve onunla birlikte hareket edebilir) olabilir.
Ağır ve uzun parçaları işlerken (haddelenmiş ürünlerden), bir uç aynaya sabitlenir ve diğeri puntanın merkezi tarafından desteklenir. Bu, parçanın sabitlenmesi için gerekli sertliği sağlar ve merkezlerin aşınmasını azaltır.
Chuck tornalama
Parçaları bir orana sahip işleme, aynaya sabitlerken gerçekleştirilir. Kartuşlar üç ve dört çenelidir.
Simetrik parçaları sabitlemek için genellikle üç çeneli kendinden merkezlemeli bir ayna kullanılır. Bu aynada, kavrama çeneleri aynı anda merkeze doğru veya merkezden uzağa doğru hareket edebilir.
Dört çeneli aynaların her bir çene için bağımsız hareketi vardır. Bu kartuşlar, karmaşık ve asimetrik şekilli parçaları takmak ve sabitlemek için kullanılır.
Ön yüz döndürme
İş miline vidalanan ön yüz plakası, simetrik olmayan parçaları ve karmaşık şekilli parçaları işlerken kullanılır. Ön yüz, radyal olarak kesilmiş oluklara sahip bir disktir. İş parçası, cıvatalarla ön plakaya sabitlenmiştir. Bazen bir kare önce yerleştirilir ve iş parçası ona bağlanır. Sabit kısım bir karşı ağırlık ile dengelenir.
Tornalama kaba ve bitişe ayrılmıştır. Kaba tornalamada 2-5 mm'lik bir pay kaldırılır. Tornalama, kesiciler ile gerçekleştirilir (Şekil 1). Kaba kesicilerin üst kısmının eğrilik yarıçapı R = 0,5-1 mm, yarı ince işleme R = 1,5-2 mm, ince tornalama için R = 3-5 mm.
Şekil 1. Tornalama kalıpları
1 - düz bir sol kesici ile uzunlamasına tornalama
2 - düz bir sağ kesici ile uzunlamasına tornalama
3 - bükülmüş sağ kesici ile uzunlamasına tornalama
4 - itme sağ kesici ile boyuna tornalama
Bitirme payları, kenar başına 1-2 mm veya daha az değişir. Tornalama, yuvarlak uçlu kesiciler ve geniş kesiciler ile gerçekleştirilir.
Uç yüzeyleri döndürmek için puanlama kesiciler kullanılır (Şekil 2). Uç yüzeyleri işlerken, iş parçaları, dış silindirik yüzeyleri işlerken olduğu gibi sabitlenir. Mandrene sabitlerken, iş parçasının çıkıntısı minimum olmalıdır. İş parçasının ucunu kenetleme arka merkezi ile sabitlerken kesmek için özel bir kesme referansı sabit merkez kullanılır.
İncir. 2. Uçların kesicilerle kırpılması:
a) doğrudan
b) bükülmüş
c) içinden itme
d) alttan kesme
Önceden delinmiş deliklerin veya kesme işlemleri sırasında elde edilen deliklerin açılması, kaba işleme ve finiş (yüklü bir kesme kenarı ile) kesiciler ile gerçekleştirilir. Açık delikler için delik işleme takımlarının ana giriş açısı 90 o'dan azdır, kör delikler için delik işleme takımları için açı 90 o'ye eşit veya biraz daha büyüktür (Şekil 3).
Şek. 3. Açık delik (a) ve kör delik (b) delik işleme
soyma kesici
İş parçalarının kesilmesi ve tornalanması dairesel oluklar kesiciler ve oluklu (oluk açma) kesiciler tarafından üretilir (Şekil 4).
Şekil 4. Kanal açma takımıyla kanal açma veya kesme takımıyla kesme
Şekilli yüzeyleri işlemek için yuvarlak ve prizmatik şekilli kesiciler veya fotokopi makineleri kullanılır.
sivrilen
Konik yüzeylerin işlenmesi aşağıdaki yöntemlerle gerçekleştirilebilir:
1. Punta muhafazasını dengeleyerek
2. Üst kaliper taşıyıcısının döndürülmesi
3. Bir kopya cetveli yardımıyla
4. Geniş bir kesici ile tornalama
Punta gövdesinin enine yer değiştirmesi ile konik yüzeylerin döndürülmesi (Şekil 5)
Şek.5. Punta gövdesinin enine yer değiştirmesi ile konilerin döndürülmesi
1 sürücülü kartuş; 2- ön merkez; 3- yaka;
4- arka merkez; 5- punta kalemi; 6 - boş; 7 - kesici
Bu yöntemle, arka merkez enine yönde kaydırılarak merkezlerin ekseni kaydırılır. İş parçasının, mesnet ve punta merkezlerine monte edilen işlenmiş konik yüzeyinin generatrisi, makinenin merkezlerinin çizgisine paralel olacaktır.
Punta gövdesinin enine yer değiştirmesinin değeri aşağıdaki formülle belirlenir:
nerede: d- koninin küçük tabanının çapı, mm; D koninin büyük tabanının çapıdır, mm; L– işlenen tüm iş parçasının uzunluğu, mm; ben konik yüzeyin yüksekliğidir, mm.
Bu sayede uzun dış konik yüzeyler en fazla olmayan bir açı ile hafif bir konik ile.
Yöntemin dezavantajları: iç konik yüzeylerin işlenmesinin imkansızlığı; sadece yumuşak koniler elde etme imkanı; merkezlerin yanlış hizalanması nedeniyle merkezlerin ve merkez deliklerin artan ve eşit olmayan aşınması.
Üst desteğin taşıyıcısını çevirerek konik yüzeylerin işlenmesi (Şekil 6).
Şekil 6. Üst desteğin taşıyıcısını çevirerek konileri döndürme.
1- üç çeneli ayna; 2 - boş; 3 - üst kaliperin manuel hareketi için tutamak; 4 - alet tutuculu üst destek; 5 - kesici
Bu sayede kısa konik yüzeyler herhangi bir koni açısı ile döndürülür (ve sıkılır). Bunu yapmak için, üst kaliperin taşıyıcısı, işlenmekte olan koninin tepesindeki açının yarısına eşit bir açıyla döndürülür. İşleme, üst kaliperin makine merkezleri hattına açılı olarak manuel olarak beslenmesiyle gerçekleştirilir. Açı değeri şu ifadeden belirlenir:
Yöntemin dezavantajları: işgücü verimliliğini azaltan ve işlenmiş yüzeyin pürüzlülüğünü artıran manuel besleme kullanımı; uzunlukları üst destek taşıyıcısının (100-150 mm) strok uzunluğunu aşan konik yüzeylerin döndürülmesinin imkansızlığı.
Geniş bir torna aleti ile konik bir yüzeyin tornalanması (Şek. 7).
Şekil 7. Geniş bir tornalama aleti ile konileri döndürme
1 - üç çeneli ayna; 2 - boş; 3 - arka merkez; 4 - kesici
Bu şekilde, kısa konik yüzeyler, plandaki ana açının tornalanmış konik yüzeyin tepesindeki açının yarısına eşit olduğu torna kesicilerle 25-30 mm'den fazla olmayan bir generatrix uzunluğuna sahip tornalanır. Kesicinin ana kesme bıçağının uzunluğu, konik yüzeyin generatrisinin uzunluğundan 1-3 mm daha uzun olmalıdır. İşleme, kesicinin enine veya boyuna beslemesi ile gerçekleştirilir. Yöntem, işlenmiş silindirik yüzeylerde pah kırmak için yaygın olarak kullanılmaktadır.
Yöntemin dezavantajları: gibi uzun konik yüzeyleri işleyememe parçanın uzunluğundaki bir artışla, işlenen yüzeyin pürüzlülüğünü artıran titreşimler meydana gelir; işlenmiş yüzeyin düşük kalitesi.
4. 2. Ana torna takımları türleri
Torna kesiciler bir dizi kritere göre sınıflandırılır.
1. Yapılan işin türüne veya teknolojik özelliğe göre: (1), alttan kesme (2), delme (3), kesme (4), dişli (5) vb.
2. Kesici başın şekline göre: düz (1), bükülmüş (2), kavisli (3), çekilmiş (4).
3. Besleme yönünde: sol(1), sağ(2).
Doğru Ana kesici kenarın sağ elin başparmağının yanına yerleştirildiği, elin avuç içi ile kesicinin üzerine yerleştirildiği, böylece parmakların kesicinin üstüne doğru yönlendirildiği bir kesici denir. Bu tür kesicilerle tornalarken, kumpas sağdan sola hareket ettirildiğinde talaşlar iş parçasından kesilir.
Ayrıldı Ana kesici kenarın sol elin başparmağının yanına yerleştirildiği, elin avuç içi ile kesicinin üzerine yerleştirildiği, böylece parmakların kesicinin üstüne doğru yönlendirildiği bir kesici denir. Bu tür kesicilerle tornalarken, kaliper soldan sağa hareket ettirildiğinde talaşlar iş parçasından kesilir.
4. Kesme parçasının malzemesine göre: yüksek hız çeliği, sert alaşım.
5. Kesici parçanın tasarımına göre: katı ve kompozit (lehimli bir plaka ile veya kesme plakasının mekanik olarak sabitlenmesi ile).
4.3. Bir torna takımının elemanları ve geometrik parametreleri
Herhangi bir kesici takım iki parçadan oluşur: I - kesme parçası; II - sabitleme parçası (Şek. 8).
Şekil 8. Bir torna aletinin elemanları
Kesme kısmında, aşağıdaki unsurlar ayırt edilir:
1 - talaşların çıktığı ön yüzey
2-ana bıçağa bitişik ana arka yüzey
3 ana kesme bıçağı
4'lü kesici
5-yardımcı bıçağa bitişik yardımcı arka yüzey
6-yardımcı kesme bıçağı
4. 4. Statik olarak kesicilerin geometrisi
4.4.1. koordinat düzlemleri
Kesme işlemini gerçekleştirmek için kesici ön ve arka yüzeyler boyunca bilenir. Kesicinin açılarını okumak için koordinat düzlemleri kullanılır (Şekil 9, 10).
ana uçak(OP) boyuna doğrultulara paralel bir düzlemdir ( S pr) ve enine ( S p) vuruşlar. Torna kesiciler için ana düzlem genellikle kesici milin alt yatak yüzeyi ile çakışır.
Şekil 9. koordinat düzlemleri
kesme düzlemi(PR), iş parçasının kesme yüzeyine teğet olarak kesicinin ana kesme bıçağından geçer.
Ana kesme düzlemi (NN) ana kesme bıçağının ana düzlem üzerindeki izdüşümüne dik olarak ana kesme bıçağının keyfi bir noktasından geçer.
Yardımcı kesme düzlemi yardımcı kesme bıçağının ana düzlem üzerindeki izdüşümüne dik olarak yardımcı kesme bıçağının keyfi bir noktasından geçer.
Şekil 10. Doğrudan tornalamanın kesme parçasının geometrik parametreleri
kesici aracılığıyla
4.4.2. Takım açıları tornalama
Kesicinin ana bileme açıları, ana kesme düzleminde ölçülür.
ön açıön yüzey ile ana kesme bıçağının içinden çizilen kesme düzlemine dik düzlem arasındaki açıyı arayın.
arka açı kesicinin ana arka yüzeyi ile kesme düzlemi arasındaki açıya denir.
Ön ve ana arka yüzeyler arasındaki açıya denir. konik açı kesici diş.
Eğim yüzü ile kesme düzlemi arasındaki açıya denir. kesme açısı .
Plan açıları taban düzleminde tanımlanır.
Önde gelen açı- ana kesme bıçağının ana düzlem üzerindeki izdüşümü ile besleme yönü arasındaki açı.
Yardımcı kurşun açısı- yardımcı kesme bıçağının ana düzlem üzerindeki izdüşümü ile besleme yönüne zıt yön arasındaki açı.
Kesicinin üstündeki köşe- ana düzlemdeki ana ve yardımcı kesme bıçaklarının çıkıntıları arasındaki açı.
Ana kesme bıçağının eğim açısı ana kesme bıçağından ana düzleme dik olan bir düzlemde, ana kesme bıçağı ile kesicinin ucundan ana düzleme paralel olarak çizilen bir çizgi arasında ölçülür.
Açı pozitif (kesici uç, ana kesme bıçağının en alt noktasıdır), negatif (kesici uç, ana kesme bıçağının en yüksek noktasıdır) veya sıfır olabilir.
Yardımcı kesici açıları yardımcı kesme düzleminde dikkate alınır.
Yardımcı arka köşe- ikincil arka yüzey ile ana düzleme dik olan ikincil kesici kenardan geçen düzlem arasındaki açı.
açıların atanması
Arka açı kesicinin arka yüzeyi ile iş parçası arasındaki sürtünmeyi azaltmaya yarar. Sürtünmenin azalmasıyla, ısı ve takım aşınması azalır, ancak büyük bir arka açı ile kesici zayıflar ve kırılabilir. Boşluk açısı arttıkça yüzey kalitesi iyileşir. Metal ne kadar yumuşaksa, açı o kadar büyük olmalıdır. Kesicinin üstündeki köşe
Eğim açısı, değerinde bir düşüşle (sıfırdan ve aşağıdan) keskin bir şekilde azalan kesicinin titreşim direnci üzerinde büyük bir etkiye sahiptir. Bu nedenle, titreşimlerin ortaya çıkmasını önlemek için, 15-25 ° 'lik bir ön açı almak gerekir ve genellikle plakanın yerleştirme açısına eşit yapılır. Talaş kıvrılmasını ve uygun şekilde çıkarılmasını sağlamak için kesicinin ön yüzeyinin kavisli veya delikli olması önerilir. Ana kesme kenarını sertleştirmek için, -3 - 5° negatif eğim açısına sahip 0,2-0,3 mm genişliğinde bir şerit sağlanması tavsiye edilir. Bununla birlikte, böyle bir şeride yalnızca kesici için yeterince ağır çalışma koşulları varsa izin verildiğini unutmamalıyız. Sertlik koşulları, negatif açılı bir takviye bandı kullanımına izin vermiyorsa, sert ve viskoz malzemeler için 10° pozitif bir açıyla sert için 5°'lik bir pozitif açıyla yapılması tavsiye edilir. Küçük genişliği ile takviye şeridi, kesme direncinin değerini etkilemez, çünkü talaşın basınç merkezi, şeridin sınırının ötesine, geniş bir eğim açısı ile donatılmış kavisli ön yüzey bölgesine girer.
Şekil 66 - Kesme takımı açıları
Uygulamada, ön yüzeyin dihedral açı şeklinde oluşturulduğu kesiciler vardır (Şekil 66, b). Düzlemleri referans düzleme μ = 10÷15° açıyla eğimlidir. Bu düzlemlerin kesişim çizgisi referans düzlemine paraleldir. Bu tasarım, kesicinin iş parçasına daha iyi nüfuz etmesine katkıda bulunur.
Arka açı
Ana kesici kenarın arka açısı plaka üzerinde 8º ve tutucuda 12º olarak alınmıştır.
keskin kenar
Kesicinin ana kesici kenarı çeşitli şekillerde tasarlanabilir. Büyük iş parçalarını kesmek için iki kesici kenarlı bir kesici tavsiye edilebilir (Şek. 66, c)². Talaşların iki parçaya ayrılmasını sağlayarak kesme bölgesinden çıkarmayı kolaylaştırırlar. Bu tasarım yüksek hız çeliği kesiciler için daha uygundur, keskinleştirme zorluğu ve kesici kenarın düşük mukavemeti nedeniyle karbür kesiciler için daha az uygundur.
Dikkate değer olan, ana kesici kenarın iki açıda φ tasarımıdır (Şek. 66, d). Bu şekil, kesicinin iş parçasına kesilmesini kolaylaştırır ve kenarını uzatır. Plan açıları φ 60-80° (ς = 30 ÷10º) içinde kabul edilir.
Ana kesici kenarın φ = 90° açıyla yapılması durumunda, her iki tarafta 45° açıyla f = 1 ÷ 1,5 mm pah yapılması veya küçük yuvarlama yapılması önerilir (Şek. 66, e). ).
Uygulamada, kesme sırasında iş parçasının merkezindeki silindirik işlemin kesilmeden bırakılmasının istenmediği durumlar vardır (örneğin, otomatik makinelerde işlerken). Böyle bir çubuğu kesmek için, kesici kenar φ = 75 ÷ 80° açıyla oluşturulur.
Artan titreşim direnci
Bazen boşluklar, ana kesme kenarının ana arka yüzeydeki bir deliğin taşlanmasıyla elde edilen içbükey bir şekle sahip olduğu bir kesici ile kesilir (Şekil 66, g). Bu formun amacı, kesicinin titreşim direncini ve ilerleme hızını artırma olasılığını arttırmaktır.
Kesici kesicilerin ağır çalışma koşulları, kural olarak, bunları formda kullanmaya zorlar. monolitik yapı, prefabrik yapılar ise pratikte nadiren bulunur.
- 4515 görüntüleme