Reinforcement of winder steps. Monolith staircase
CATALOG OF CONCRETE STAIRS:
Monolithic concrete stairs have been used in construction for a long time and very successfully. These products are manufactured in accordance with GOST and all quality standards, have standard sizes, which are provided for during construction.
They can be used in private houses and cottages, in residential entrances apartment buildings, in office buildings and many other premises.
In the face of fierce competition, manufacturers are paying more and more attention to the quality of products. Therefore, we produce only high-quality products that meet the highest customer requirements.
Monolithic stairs made of concrete - manufacturing technology
The manufacturing technology of monolithic concrete stairs is not too complicated, but it requires care, correct calculations and high-quality work, since if all the points are not followed, the concrete may crack or shrink. Stairs must be installed strictly according to the project. At the stairwells recent times solid windows with light-shielding elements (roller blinds, blinds) are installed, and stairs are not always well lit at one time. It is important that such a platform and steps are neat, even, and all installation rules are observed.
If you still do reinforced concrete stairs with your own hands, follow the step-by-step instructions:
- We design. We clearly define the dimensions of the reinforced concrete staircase, the number of steps, the dimensions of the platforms and marches. Also quite a few important characteristic- rise (height) of the step.
- Formwork. Two manufacturing options are possible: for the entire length of the march (plus there will be speed of manufacture) and separately for the step (in this case, all steps will be exactly the same size).
- Strengthening. The outer side of the formwork should be strengthened so that the concrete mortar does not break the proportionality and does not destroy the formwork itself.
- Reinforcement. Concrete concrete staircase implies the presence of metal, which will serve for the rigidity of the structure. This can be reinforcement, rods or mesh, which is welded to the dimensions of the future monolithic staircase.
- Base. The very base of the formwork with the help of a drainage base made of broken bricks or gravel must be strong, perfectly even.
- Ramming. It should be carried out very tightly (you can additionally use sand) so that voids do not form.
- Fill. In technology, an important stage is the manufacture of a solution that contains proportionally: 1: 3: 3 cement: sand: crushed stone.
- Drying. It takes approximately 5-10 days (depending on humidity and temperature) for complete curing and drying.
- Finishing. It can be used as desired. Most often, the decoration is done in private. You can use porcelain stoneware, tiles, decorative stone, etc.
The price for the installation of reinforced concrete stairs varies from different specialists and can vary from 5,000 to 50,000 rubles. depending on the staircase itself, its dimensions, installation method, its design, as well as the presence of its decorative finish.
The production of monolithic concrete stairs can be complete or parts:
- steps (have different heights, lengths and widths);
- marches (manufactured according to GOST, have various sizes and weight);
- platforms (get by the size of the steps);
Stair steps, marches and platforms from MosStroyKomplekt. Production. Sale. Delivery. You can buy stair steps, marches and landings of the best quality from us. And our managers are always ready to give professional advice. Special flexible prices for you! Call now!
Monolithic products
Monolithic products must be reinforced. Monolithic structures, reinforced steel frame are called reinforced concrete structures.
Reinforcement of products performs the function of a "rod", on which the entire monolithic structure rests. Reinforcing structure (hereinafter reinforcement cage or simply reinforcement) depends on the purpose and loads that will be carried monolithic product.
Individual rods and wires are used as reinforcement reinforced concrete structures, as well as wire bundles and packages, welded meshes, flat and three-dimensional frames.
But embedded parts constitute a special group of reinforcing products. Embedded parts come to the concrete surface if the reinforcing cage in the finished product is walled up in concrete and serve as a link between the frame and products, which, if necessary, will be attached to this reinforced concrete structure.
Reinforcing works
The manufacture of the reinforcing cage and mesh must be carried out according to the drawings and have the exact location of the elements to be welded. The replacement of the reinforcing steel provided for by the project by class, grade and assortment is agreed with the design organization.
The process of manufacturing a reinforcing cage according to the technology provides for:
- straightening and cutting of steel reinforcement, wire supplied in coils with a diameter of 3 ... 14 mm and in bars with a diameter of 12 ... 40 mm into bars of a specific length
- straightening (bending) and butt welding of rods up to right size
- mesh and frame welding
- pre-assembly (welding and wire tying) of volumetric reinforcing blocks
- transportation and installation of frames at the construction site.
Reinforcing cage of a monolithic section for a landing.
Note:
Steel of class A-III with a diameter of 12-20 mm - steel of a periodic profile (in rods).
Steel class A-III, diameter 8 mm - smooth fittings (in coils).
Table 1: Reinforcement specification for the frame of a monolithic section of a landing
Position mark | Designation | Name | Weight, in kg | Consumption, in linear meters | Note |
5 | GOST 5781-82 | Armature dia.8 A-III | 35 | 106 | to one site |
6 | GOST 5781-82 | Rebar dia.12 A-III | 5 | 7 | Same |
7 | GOST 5781-82 | Armature dia.20 A-III | 14 | 7 | Same |
Concrete class At 15 | 0.5 m 3 |
The mesh is best welded by spot welding. For the frame, you must also use reinforcement according to the specified table:
The reinforcing bars of the cross crossings mounted individually, in the places of their intersection, established in the project, should be fastened with a knitting wire. In the reinforcing cage, there should be no dangling, crossing and broken wires. The wire should fit snugly against each other.
If the wire or reinforcing wire in coils is affected by corrosion, then it is not allowed to be used. If the rust on the wire cannot be removed by wiping, then the wire is considered to be corroded.
Do not forget to clean the reinforcement and formwork from debris, dirt and flaking rust before concreting. And the surface of the wooden formwork adjacent to the concrete must be moistened. If, during the installation of the frame, gaps were formed in the formwork flooring, then they should be repaired.
Linings (crackers from cement mortar) should be fixed on the formwork before installing the frame, providing the necessary gap between the reinforcement and the formwork to form a protective layer of the floor.
ATTENTION! Mounted reinforcement must be secured against displacement and protected from damage that may occur during the concreting of the slab structure. It is forbidden to use linings from rebar scraps, wooden blocks and crushed stone.
It should be noted that the concrete mixture is laid into the structure in horizontal layers of the same thickness without gaps, with a consistent laying direction in one direction in all layers. Also, when laying the concrete mixture, methods should be used that exclude its delamination.
The concrete mixture must be compacted with a vibrator, which must not be supported on reinforcement during operation. It is possible to stop vibrating only after the appearance of cement laitance on the surface.
In places where the density of the reinforcement or the location of the formwork prevents the compaction of the concrete mixture by vibration, the mixture is bayoneted (compacted with a metal rod, "bayonet").
Note: It is acceptable to compact the concrete mix with a surface vibrator if the thickness of the concrete mix layer in structures with double reinforcement does not exceed 120 mm.
Ceilings monolithically connected with vertical structures (walls, columns) are concreted 1-2 hours after these structures are concreted. Working seams must be arranged in the middle third of the spans of the slab.
ATTENTION! In places of the alleged breakage, during breaks in the laying of the concrete mixture, vertical shields should be temporarily installed. In this case, concreting should be brought up to these shields.
After a break, the concrete mixture is laid on the surface of the working joint, previously cleaned of dirt (cement film) and washed with water, provided that the strength of the previously laid concrete is at least 15 kgf / cm2.
The level of the top mix to be laid must be 50 mm below the top of the formwork panels.
Do not forget also that concrete work must be performed only at a positive temperature. environment.
ATTENTION! It is impossible to restore the mobility of the concrete mixture to the required consistency by adding water at the place of its laying.
If cracks appear on the concrete surface after its laying due to plastic shrinkage, then it is allowed no later than 1 hour after the completion of concrete laying, its repeated surface vibration.
Concrete curing and maintenance
In the initial period of its hardening, when curing the laid concrete, it is necessary:
- maintain a temperature and humidity regime that ensures an increase in the strength of concrete
- it is necessary to protect hardening concrete from impacts, shocks and other mechanical influences
- protect hardening concrete from wind, direct sunlight and systematically moisten.
Note: During initial maintenance, the curing concrete should not be allowed to come into direct contact with water (i.e., cover the concrete from moisture in case of rain).
Curing concrete should be wetted by spraying at a frequency that would keep the surface of the concrete wet at all times during curing.
In places where the concrete surface is not intended in the future for a monolithic connection with concrete or mortar, it is necessary to cover it with film-forming compounds or protective films instead of shelter and watering.
The open surface of the structure must be covered with a solid panel over the entire area, and the edges of the panel must fit snugly against the side surfaces of the concrete.
In order to exclude the time-consuming operation of moisture maintenance of concrete or to accelerate its hardening, electrical heating of concrete is performed.
Concrete maintenance should be stopped in the evening. And after the cessation of leaving the concrete surface for another 2-3 days, they must be kept under the coating without additional moisture.
ATTENTION! The movement of people on concrete structures is prohibited, as well as the installation of scaffolding and formwork on them is allowed only after the concrete reaches a strength of at least 15 kgf / cm2.
One of the options for connecting the first and second floors of a private house can be, which, in principle, is not difficult to complete if you have even minimal experience with formwork. This staircase is almost eternal. It does not creak or loosen like wood, does not require frequent painting and does not collect dust like metal, is fire resistant and can withstand any load.
Yes, it is quite massive, material-intensive, it ... Here, perhaps, are all its negative sides. Because, for all its seeming static, it can be very different and original, unexpectedly impressive and aristocratically luxurious. The attractiveness of a monolithic staircase depends on the quality and originality of its finish, as well as on the type of handrails that will be used in its manufacture. Wood or forging, metal or glass - in any case, it will not look like a standard staircase in a multi-storey building. Because you are doing it for yourself, by yourself, in your home.
But the installation of formwork and the manufacture of reinforcing cages for stairs is the second, practical part of the monolithic staircase. First of all, you need to correctly calculate and at, because the convenience of constant ascents and descents depends on it. I will devote the next post to the topic of how to calculate the stairs, but for now I want to draw your attention to the fact that the standard height of the steps of the internal staircase is 150 mm with a step width of 300 mm. This ratio is optimal in all respects. The width of the flight of stairs must be at least 1000 mm, although the standard monolithic staircase has a width of 1200 mm. The minimum width of the landing should have a size corresponding to the width of the flight of stairs, to which another 100 mm is added.
When starting the construction of the walls of the house according to the project, do not forget to leave a gap in the wall of the stair masonry at the right height for the intermediate landing. The best option the support of the landing on the walls is considered three-sided. The minimum support of a monolithic platform on brick wall is 150 mm, for aerated concrete - 200 mm.
Reinforcement of a monolithic staircase
Since almost all country houses have a floor height of up to 3 meters, reinforcement of a monolithic staircase, which I will discuss below, you can safely use when building this structure in your own construction.
For reinforcement of a monolithic staircase reinforcement Ø14 mm А400С and Ø8 mm А400С, as well as wire Ø4 mm Вр-I are required. Both landings and flights of stairs are necessarily reinforced with a double mesh. Longitudinal reinforcement of flights of stairs, Ø14 mm А400С, is laid in increments of 150 mm. With the help of a simple one, it needs to be bent, giving the necessary shape corresponding to the profile of the platform and the march. The transverse reinforcement of the flights of stairs is made of Ø8 mm A400C, and it is laid on the longitudinal reinforcement rods in the following order:
- in sections of 800-900 mm from the points of support on the landing or foundation in increments of 150 mm;
- in the middle of the span, between the sections specified above - in increments of 200 mm.
Reinforcement of the landing is also made of reinforcement Ø14 mm, installing it in increments of 200 mm.
Only in places where the platforms rest on the walls, as well as in the area between the flights of stairs, the rods are laid in increments of 150 mm. The separation of two meshes of reinforcement of a monolithic staircase to the required distance is carried out using a special retainer made of reinforcement Ø8 mm A400C. Since the thickness of a monolithic staircase is 200 mm, the height of such a latch should be no more than 100 mm. The connection between the lower and upper grids is carried out with the help of vertical hooks, the height of which should not exceed 120 mm. Such hooks are installed on the longitudinal reinforcement of flights of stairs and landings in a checkerboard pattern, through one rod in a row. The steps themselves are reinforced with a flat mesh of Ø4 mm Vp-I, which is attached to the reinforcement of the main frame. For a better understanding, the reinforcement of a monolithic staircase is shown in the diagram.
Designation on the diagram: 1 - longitudinal reinforcement, reinforcement Ø14 mm А400С; 2 - latch separation of the upper and lower reinforcement mesh; 3 – reinforcement of the steps with a mesh of Ø4 mm Вр-I; 4 – vertical hooks made of Ø4 mm Вр-I.
Formwork and concrete
Undoubtedly, the best is the inventory formwork used in the device monolithic floor. Its easily adjustable posts, wooden crossbars and waterproof plywood make it possible not only to quickly and efficiently install the formwork, but also to obtain a finished structure. High Quality. I am almost 98% sure that you do not have such formwork. Well, to hell with her! The main thing is that there are strong sheets of plywood or other sheet material that can be laid on wooden bars section 140x80 mm. Use more nails, struts and stops. If the entire formwork is made carefully, using a level, without distortions and slack, this formwork method also has the right to exist. We sometimes use pallets in our work, connecting them with tops. Get stable stops. And remember, if the steps or platform are crooked, its lining ceramic tiles turn into a real torture for you.
Formwork for a monolithic staircase begins to be installed from the landings. Only after checking their horizontalness, you can proceed with the installation of formwork for flights of stairs. If your first flight of stairs rests on the ground, lean it on two columnar foundation with a diameter of 300 mm.
Monolithic staircase has a thickness of 200 mm. When laying concrete in the finished formwork, try to do-it-yourself monolithic staircase without interruption, in one day. Pay special attention to high-quality concrete laying. The use of a deep vibrator will significantly speed up the concreting process and improve the quality of the finished staircase.
After completing the work, let the formwork stand for at least a week. This is during the summer months. During the colder season formwork for a monolithic staircase should stay longer.
During construction work reinforced concrete monolithic structures should follow the requirements SNiP 3.03.01-87"Bearing and enclosing structures" and the relevant sections of the safety regulations given in SNiP III-4-80, working drawings and instructions for PPR - a project for the production of work.
Reinforcing works SNiP 3.03.01-87"Bearing and enclosing structures", GOST 19292-73, "Instructions for welding reinforcement joints and embedded parts of reinforced concrete structures" CH 393-78, "Guidelines for the production of reinforcing work" and other applicable normative documents.
In the proposed version for device monolithic landing with bevels(UM-3) use additional extension to the house in the form of a bay window.
Thereby the bay window serves and additional staircase lighting and saves space in the box space at home under the stairs.
Bay window- this is a part of the room emerging from the plane of the facade, partially or completely glazed, improving its illumination and insolation.
And since this version of the landing does not fit into the standard dimensions of industrial reinforced concrete products and structures, it is necessary fulfill her in monolithic version at the construction site.
In our version monolithic platform is a continuation prefabricated concrete stairs, the device of which can be viewed in the section of the site "Plan of the device of a reinforced concrete (reinforced concrete) staircase. Section of the stairwell under the reinforced concrete staircase. Installation of metal structures under the reinforced concrete staircase. Installation and finishing work when installing reinforced concrete stairs. Materials for the device reinforced concrete stairs on a metal frame" .
constructive features of monolithic products provide for their mandatory reinforcement. As reinforcement of reinforced concrete structures use separate reinforcing bars and wire, welded meshes, flat and three-dimensional frames.
A special group of reinforcing products are embedded details.
If a reinforcing cage in the finished product embedded in concrete, then embedded details come to the surface of the concrete and serve a link between the frame and products, which, if necessary, will be fastened to this reinforced concrete structure.
What is reinforcing cage, specifically for landings with bevels will be discussed below.
2. Reinforcing frame of the landing with bevels (UM-3).
Technological manufacturing process reinforcing cage provides:
- straightening and cutting steel fittings, wire supplied in coils with a diameter 3…14 mm and in bars diameter 12…40 mm on rods of measured length;
- straightening (bending) and butt welding rods to the desired size;
- mesh and frame welding;
- enlargement assembly(welding and wire knitting) volumetric reinforcing blocks;
- transportation and installation frames at a construction site.
The performance of the above works can be found in the sections of the site "Reinforcement works and types of reinforcement. Procurement and bending of rod and wire reinforcement. Procurement of embedded parts", "Heavy and light reinforcing mesh. Wire reinforcement mesh" and "Installation of reinforcing cages. Assembly and welding of reinforcing bars and field joints of steel structures. Non-welding methods of connecting reinforcement. Protective layer of concrete reinforced concrete products ", where links to the regulatory documentation of the work performed are indicated.
Reinforcing cage of the monolithic section UM-3 for the landing performed according to the dimensions indicated on the diagrams (see Fig.).
Manufacturing reinforcing cage and mesh must be carried out according to the drawings and have exact location elements to be welded. Replacement envisaged by the project reinforcing steel by class, brand and assortment agreed with the design organization.

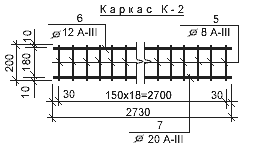
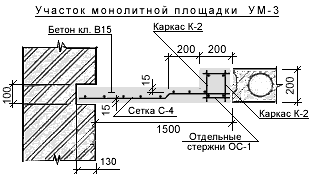
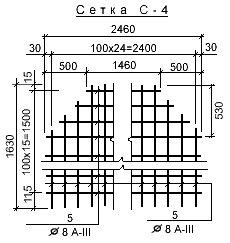
grid necessary spot welding. For frame used fittings according to the specified table.1.
Table 1: Reinforcement specification for the frame of a monolithic section of a landing
Note:
- steel grade A-III d=12-20 mm- steel periodic profile(in rods).
- steel grade A-III d=8 mm - smooth reinforcement(in coils).
Reinforcing bar cross crossings mounted individually, in their places intersections set in the project, should fasten knitting wire. In a reinforcing cage there should be no broken, crossed and broken wires. The wire should fit snugly against each other.
Wire(or reinforcing wire in coils), corroded, for use not allowed. A wire is considered corroded if the rust cannot be removed by wiping.
ATTENTION! To avoid injury and fire safety violations -
ONLY PERSONS ARE ALLOWED TO PERFORM WELDING WORK NOT UNDER 18 YEARS, WHO HAVE BEEN SPECIALLY TRAINED (welder-builder) AND HAVE PERMISSION TO PERFORM WELDING WORKS.
3. Concrete work for a monolithic landing with bevels.
Concrete works should be carried out in accordance with the requirements and recommendations SNiP 3.03.01-87"Bearing and enclosing structures". The composition of the concrete mixture, preparation, acceptance rules, control methods and transportation must comply with GOST 7473-85.
Rebar and formwork before concreting should clear from debris, dirt and flaking rust. The surface of the wooden formwork, adjacent to concrete, necessary moisturize. Formed during the installation of the frame cracks in the formwork close up.
Before installation frame on formwork must be linings fixed(crackers from cement mortar), providing the necessary gap between reinforcement and formwork for education protective cover layer.
Below is given cross section of the landing with bevels(UM-3) along the cut line 3-3:


ATTENTION! Mounted fittings must be secured against displacement and protected from damage that can occur during the concreting of the slab structure. It is forbidden to use linings from rebar scraps, wooden blocks and crushed stone.
concrete mix must fit into the design horizontal layers uniform thickness without gaps, with sequential direction laying in one direction in all layers.
When laying concrete mix should apply ways to prevent its delamination.
ATTENTION! Concrete compaction produced vibrator, which during operation cannot be leaned on reinforcement. stop vibrating can only after the appearance of cement laitance on the surface.
In places, where is the reinforcement density or the location of the formwork prevents compaction vibrating concrete mix mix bayonet (compacted metal rod, "bayonet").
NOTE: Allowed concrete mix compaction surface vibrator, if concrete layer thickness in designs with double reinforcement less than 120 mm.
Overlappings, monolithic connected with vertical structures (walls, columns), concreted after 1-2 hours after concreting these structures. Working seams necessary arrange in the middle third of the slab spans.
ATTENTION! Interruptions in concrete placement in the places of the expected break vertical shields should be temporarily installed. concreting at the same time it should reach these shields.
Laying concrete mix after the break is made on the surface of the working seam, pre purified from dirt (cement film) and washed with water, provided that the strength of previously laid concrete will be at least 15 kgf / cm².
Upper level mixture to be laid it should be by 50 mm below the top of the formwork panels.
Concrete works performed only at a positive temperature environment.
ATTENTION! Not allowed to recover mobility of the concrete mix to the desired consistency adding water at the place of its laying.
When it appears on the concrete surface after laying it cracks due to plastic shrinkage allowed no later than than through 1 hour after the completion of concrete placement, its repeated surface vibration.
4. Curing and care of concrete.
When curing laid concrete during the initial period of its hardening necessary:
- support temperature and humidity conditions, providing an increase in the strength of concrete;
- protect hardening concrete from impacts, concussions and other mechanical influences;
- protect hardening concrete from the influence of the wind, direct sunlight and systematically moisturize.
NOTE: During initial care not allowed direct contact of hardening concrete with water(those. cover concrete from moisture ingress in case of rain).
Moisturizing should produce hardening concrete spattered with the frequency at which the surface of the concrete during the maintenance period would be wet all the time.
concrete surfaces, not further intended for monolithic connection with concrete or mortar, should instead of shelter and watering cover with film-forming compounds or protective films.
Should take cover open surface design solid cloth over the entire area, the edges of the cloth should fit snugly to the side surfaces of concrete.
In order to exclude the labor-intensive operation of moisture maintenance of concrete and accelerate its hardening, electrical heating of concrete.
End of concrete care carried out in evening time. After cessation of care concrete surfaces must be kept under cover still during 2-3 days without additional moisture.
ATTENTION! people movement for concrete structures, as well as installation on them scaffolding and formwork allowed only at least 15 kgf/cm².
Demoulding of monolithic structures should be made at the times indicated below:
- removal of side formwork, not load bearing from the weight of structures ( for the loggia, except for the landing and beveled slab) - after the concrete reaches strength, ensuring the safety of the surface and edges of the corners when removing the formwork;
- stripping of load-bearing reinforced concrete structures (landing and beveled slab) - after the concrete reaches strength and depends on the dimensions of the monolithic structure- according to Table 1 "Approximate terms of formwork removal" of the section "Arrangement and dismantling of formwork under monolithic slab".
Design features monolithic products provide for their mandatory reinforcement. Monolithic structures reinforced with a steel frame are called reinforced concrete structures.
Reinforcement of products performs the function of a "rod", on which the entire monolithic structure rests. The reinforcing structure (hereinafter referred to as the reinforcing cage or simply fittings) depends on the purpose and loads that the monolithic product will carry.
Individual rods and wires, wire bundles and packages, welded meshes, flat and bulk frames are used as reinforcement for reinforced concrete structures.
Embedded parts constitute a special group of reinforcing products. If the reinforcing cage in the finished product is embedded in concrete, then the embedded parts come to the surface of the concrete and serve as a link between the frame and products, which, if necessary, will be attached to this reinforced concrete structure.
In general terms, you now imagine what monolithic reinforced concrete structures are. What is a reinforcing cage, specifically for the landing, we will consider below.
Reinforcing works
Reinforcing work should be carried out in accordance with the requirements and recommendations of SNiP 3.03.01-87 "Bearing and enclosing structures", GOST 19292-73, "Instructions for welding reinforcement joints and embedded parts of reinforced concrete structures" SN 393-78, "Guidelines for the production of reinforcing works "TsNIIOMTP Gosstroy-1977. and other applicable regulations.
The manufacture of the reinforcing cage and mesh must be carried out according to the drawings and have the exact location of the elements to be welded. The replacement of the reinforcing steel provided for by the project by class, grade and assortment is agreed with the design organization.
The technological process of manufacturing a reinforcing cage provides for:
straightening and cutting of steel reinforcement, wire, supplied in coils with a diameter of 3 ... 14 mm and in bars with a diameter of 12 ... 40 mm into rods of a specific length;
straightening (bending) and butt welding of rods to the desired size;
welding of meshes and frames;
pre-assembly (welding and wire tying) of volumetric reinforcing blocks;
transportation and installation of frames at the construction site.
The reinforcement cage of the monolithic section No. 3 for the landing is made according to the dimensions indicated on the diagrams (see Fig.).
Note:
Steel of class A-III with a diameter of 12-20 mm - steel of a periodic profile (in rods).
Steel class A-III, diameter 8 mm - smooth fittings (in coils).
Table 1: Reinforcement specification for the frame of a monolithic section of a landing
Position mark | Designation | Name | Weight, in kg | Consumption, in linear meters | Note |
5 | GOST 5781-82 | Armature dia.8 A-III | 35 | 106 | to one site |
6 | GOST 5781-82 | Rebar dia.12 A-III | 5 | 7 | Same |
7 | GOST 5781-82 | Rebar dia.20 A-II | 14 | 7 | Same |
Concrete class At 15 | 0.5 m3 |
The mesh must be welded by spot welding. For the frame, reinforcement is used according to the specified table:
Cross crossings of reinforcement bars mounted individually, at their intersections, established in the project, should be fastened with a knitting wire. In the reinforcing cage, there should be no dangling, crossing and broken wires. The wire should fit snugly against each other.
Corroded wire (or reinforcing wire in coils) is not allowed to be used. A wire is considered corroded if the rust cannot be removed by wiping.
Attention! To avoid injury and fire safety —
Only persons at least 18 years of age who have undergone special training (builder welder) and have a permit to perform welding work are allowed to perform welding work.
Concrete works
Before performing concrete work, it is necessary to install scaffolding and formwork under the monolith. For the principle of formwork installation, see the section “Arrangement and dismantling of formwork for a monolithic slab”.
Concrete work should be carried out in accordance with the requirements and recommendations of SNiP 3.03.01-87 "Bearing and enclosing structures". The composition of the concrete mixture, preparation, acceptance rules, control methods and transportation must comply with GOST 7473-85.
Reinforcement and formwork should be cleaned of debris, dirt and flaking rust before concreting. The surface of the wooden formwork adjacent to the concrete must be moistened. Close the gaps formed during the installation of the frame in the formwork flooring.
Before installing the frame on the formwork, linings (crackers from cement mortar) must be fixed, providing the necessary gap between the reinforcement and the formwork to form a protective layer of overlap.
Attention! Mounted reinforcement must be secured against displacement and protected from damage that may occur during the concreting of the slab structure. It is forbidden to use linings from rebar scraps, wooden blocks and crushed stone.
The concrete mixture must be laid into the structure in horizontal layers of the same thickness without gaps, with a consistent direction of laying in one direction in all layers. When laying the concrete mixture, methods should be used that exclude its delamination.
Compaction of the concrete mixture is carried out with a vibrator, which must not be supported on reinforcement during operation. It is possible to stop vibrating only after the appearance of cement laitance on the surface.
In places where the density of the reinforcement or the location of the formwork prevents the compaction of the concrete mixture by vibration, the mixture is bayoneted (compacted with a metal rod, "bayonet").
Note: It is allowed to compact the concrete mix with a surface vibrator if the thickness of the concrete mix layer in structures with double reinforcement does not exceed 120 mm.
Ceilings monolithically connected with vertical structures (walls, columns) are concreted 1-2 hours after these structures are concreted. Working seams must be arranged in the middle third of the spans of the slab.
Attention! During breaks in the laying of the concrete mix, vertical shields should be temporarily installed in the places of the alleged breakage. In this case, concreting should be brought up to these shields.
After a break, the concrete mixture is laid on the surface of the working joint, previously cleaned of dirt (cement film) and washed with water, provided that the strength of the previously laid concrete is at least 15 kgf / cm2.
The top level of the mix to be laid must be 50mm below the top of the formwork panels.
Concrete work is carried out only at a positive ambient temperature.
Attention! It is not allowed to restore the mobility of the concrete mixture to the required consistency by adding water at the place of its laying.
If cracks appear on the concrete surface after its laying due to plastic shrinkage, it is allowed no later than 1 hour after the completion of concrete laying, its repeated surface vibration.
Concrete curing and maintenance
When maintaining the laid concrete in the initial period of its hardening, it is necessary:
maintain a temperature and humidity regime that ensures an increase in the strength of concrete;
protect hardening concrete from impacts, shocks and other mechanical influences;
protect hardening concrete from exposure to wind, direct sunlight and systematically moisten.
Note: During the initial care, direct contact of the hardening concrete with water is not allowed (i.e. cover the concrete from moisture in case of rain).
Moistening should be carried out on curing concrete by spraying at a frequency at which the surface of the concrete during the curing period would always be in a wet state.
Concrete surfaces that are not further intended for a monolithic connection with concrete or mortar should be covered with film-forming compounds or protective films instead of shelter and watering.
The open surface of the structure should be covered with a solid panel over the entire area, the edges of the panel should fit snugly against the side surfaces of the concrete.
In order to eliminate the time-consuming operation of moisture maintenance of concrete and accelerate its hardening, electrical heating of concrete is performed.
The termination of care of concrete is carried out in the evening. After the termination of care, the concrete surfaces must be kept under the coating for another 2-3 days without additional moisture.
Attention! The movement of people on concreted structures, as well as the installation of scaffolding and formwork on them, is allowed only after the concrete reaches a strength of at least 15 kgf / cm2.
Demoulding of monolithic structures must be carried out within the following periods:
removal of side formwork elements that do not bear the load from the weight of structures (for a loggia, except for a landing and a beveled slab) - after the concrete has reached strength, ensuring the safety of the surface and edges of the corners when the formwork is removed;
stripping of load-bearing reinforced concrete structures (landing and beveled slab) - after the concrete reaches strength and depends on the dimensions of the monolithic structure.