Monolitik betonarme bina inşaatı için teknolojiler. Depoların ve endüstriyel binaların monolitik inşaatı
Endüstriyel tesisler başarılı bir simbiyozdur mukavemet özellikleri betonarme yapılar ve ısı yalıtımı ve kaplama malzemeleri alanındaki en son gelişmeler, en yüksek güvenlik gereksinimlerini karşılayan cesur projeleri hayata geçirmemize ve kısa sürede tamamlamamıza olanak tanır. Biri umut verici yönler Modern inşaat piyasasının, inkar edilemez bir şekilde monolitik inşaat olarak adlandırılabilir.
Ana taşıyıcı elemanlar monolitten, dış elemanlar (duvarlar, çatı) kaset sandviç panellerden yapılmıştır. Monolitik yapı temelden son katın tavanına kadar tüm yükseklik boyunca yerleştirilmiş ayrılmaz betonarme çerçevelerin yapımını içerir.
monolitik yapıda kalıp
Monolitik çerçeve yapılarının yapımında kalıp özellikle önemlidir. . Modern kalıp sistemlerinin kullanılması, yapının kendisinin güvenilirliğini ve hızını artırmayı mümkün kılmıştır. Kalıp kullanımının sonucu, ek bitirme gerektirmeyen düz bir beton yüzeydir.
Kalıp tabanlı monolitik yapı teknolojisi, yapıların çok yönlülüğü ve kolonlar için çok çeşitli modüler ızgaralar nedeniyle hem konut hem de endüstriyel tesisleri birleştiren projelerin uygulanmasında özel bir popülerlik kazanmıştır.
monolitik yapı
Fiyat maliyetlerinin analizi, günümüzde yekpare yapıya layık bir alternatif olmadığını göstermektedir. Ve monolitik kalıp üretimi için pahalı hammaddelerin ve büyük endüstriyel kapasitelerin kullanılmasına rağmen, kalıp sistemlerinin üretimi ve satışı piyasada yüksek talep görmektedir.
Bina monolitik kalıp üretimi için çelik, ahşap ve alüminyum kontrplak kullanılmaktadır. Ve nihai fiyatlandırmada belirleyici faktör olan malzemedir.
Kullanım koşullarına bağlı olarak, monolitik kalıp bileşenlerine göre sınıflandırılabilir:
- kontrol Paneli,
- kiriş-kıç yatırması
- küçük panel kalıp
Monolitik yapının ana aşamaları
Bir köy yerleşiminde "Sanayi ve depo kompleksi" projesi temelinde bir endüstriyel binanın monolitik inşaat sürecini ele alalım. Lagovskoye, Moskova bölgesi. Proje GK "SPETSSTROY" şirketi tarafından uygulandı.
toprak gelişimi . Geliştirme çalışmaları birkaç aşamada gerçekleşebilir ve kabartma değişiklikleri, mühendislik ağları ve temeller için hendeklerin düzenlenmesi, zemin stabilizasyonu, saha tesviyesini içerebilir. Yol yapım ekipmanının doğru seçimi, maliyet optimizasyonu ve zaman planlamasının anahtarıdır
kazı
Temel hazırlığı . asıl görev getirmektir. taşıma kapasitesi göstergeleri tasarlamak ve vakfın tabanla yüksek kaliteli temasını sağlamak için toprak. Cihaz için kazık temel monolitik bir ızgara ile kum yastığı kullanılır. Kazıkların montajından sonra kalıp, donatı kafesi düzenlenir ve beton dökülür.
zemin hazırlığı
Monolitik ızgaraların montajı . Izgaraların montajı için kırma taş veya cüruftan yapılmış bir drenaj yastığı düzenlenir.
ızgaraların düzenlenmesi
Prefabrik betonarme yapıların montajı . Kurulum kat kat ve kademeli olarak gerçekleştirilir. Derzler betonla kapatılmıştır. Sonraki her bir katman, yalnızca tüm elemanları sabitledikten ve derzlerde karışımın gücünün en az% 70'ini elde ettikten sonra monte edilir.
prefabrik yapıların montajı
Monolitik yapıların montajı ve montajı . Beton sertleştikçe kalıp bileşenleri demonte edilir ve bir sonraki kata aktarılır. Çoğu zaman, panel kalıbı kullanılır (ayrı formlardan). Kurulum sırasında prefabrik elemanlar en sık kullanılır: merdiven basamakları, asansör boşlukları
Monolitik bir asansör şaftının cihazı
Metal kafeslerin montajı
Çerçevenin düzenlenmesine paralel olarak duvarların yapımı
İnşa edilen duvarlar monolitik teknoloji, dikişlerin neredeyse tamamen yokluğunu öne sürüyor, sonuç olarak, derzlerin sızdırmazlığı ile ilgili herhangi bir sorun yok. Monolitik duvarların ve küçük kalınlıktaki tavanların montajı, temel üzerindeki yükü önemli ölçüde azaltır.
Monolitik yapının bir diğer önemli avantajı, binaların yüksek ses yalıtım katsayısıdır. Hatta tuğla evler duvar bölmeleri, sesin yayılmasına katkıda bulunan boşlukların varlığını ima eder; monolitik yapılarda bu dezavantaj ortadan kaldırılmıştır.
Monolitik yapıların özel bir özelliği sertlik ve sağlamlıktır. Monolitik binalar bu konuda sıkı bir şekilde lider konumdadır. Binanın düzgün büzülmesi ve yüklerin yeniden dağıtılması, çatlak oluşumunu engeller. Bu nedenle endüstriyel yapılarda betonarme kullanılmaktadır.
Soğuk mevsimde, beton sertleşme sürecini yavaşlatmak gerektiğinde bazı zorluklar ortaya çıkabilir. Beton kalitesinin bozulmasını önlemek için özel katkı maddeleri veya inert malzemeler - kırma taş ve kum kullanılarak ısıtılır.
beton ısıtma kablosu
Elektrik yardımıyla betonlama teknolojisi, kalıba dökülen beton bir elektrik kablosu ile ısıtıldığında da sıklıkla kullanılır.
Leningrad Terminal MLP - monolitik yapının bir nesnesi olarak
2004 yılında, MLP şirketi Moskova bölgesindeki ilk siteyi satın aldı ve cesur bir geliştirme stratejisi açıkladı - 1,5 milyon metrekare inşa etmek. Rusya, Ukrayna ve bölgelerde depo gayrimenkul m.
Bugün, tüm modern uluslararası standartlara uygun olarak inşa edilen Rusya'nın en büyük lojistik projelerinden biridir. Terminal ciddi kiracılara, ulusötesi tüketim malları üreticilerine ve önde gelen distribütörlere yöneliktir. "MLP - Leningrad Terminali", Leningrad karayolu boyunca 42 hektarlık bir alanı kaplıyor ve 197,35 bin metrekareyi kapsıyor. m depo sınıfı A. 3
Leningrad Terminali MLP
Depo kompleksinin yüksekliği 15.5 m'dir. (çalışma yüksekliği - 12,5 m) 6 katlı raf depolama sağlar Zeminler 6 tona kadar yük için tasarlanmıştır, bu da malları taşımak ve kaldırmak için herhangi bir ekipmana dayanabilmenizi sağlar. Ürünlerin ve özel depolama koşullarına sahip malların depolanması için özel bir iklim kontrol bölgesi geliştirilmiştir. Terminal, modern bir yangın söndürme sistemi olan Lennox'tan (Fransa) bir hava ısıtma sistemi ve klimalar kullanıyor. MLP'deki elektrik besleme sistemi, 8 otonom dizel jeneratör trafo istasyonu tarafından sağlanmaktadır.
Ana işlev taşıyıcı yapılar depo terminali, 12x24 m'lik bir basamakla monte edilmiş 15 metrelik monolitik betonarme kolonlardan yapılmıştır (uygulamanın gösterdiği gibi, bu teknoloji, ek yangın koruması gerektiren metal kolonların yapımından daha ucuzdur).
120 mm sandviç panellerle kaplanmış depo duvarları Fin yalıtımı kullanan Rus üretimi. Çatı kaplamasının düzenlenmesi için, plastikleştirilmiş PVC'den yapılmış, kendini kanıtlamış Alkorplan (Belçika) membran çatı kullanılmıştır. Bu membran %300 esneme sağlar ve doğru işlem 50 yıldan fazla sürecek.
katlar- Bir depo için bu en önemli detaylardan biridir, çünkü ağır yükleme ekipmanları zeminde yüksek hızda hareket eder. Beton taban levhasındaki boşluklar er ya da geç yıkıma yol açacaktır. döşeme ve ekipman arızası. Zeminlerin onarımı, rafların sökülmesi ihtiyacına ve sonuç olarak deponun kapanmasına yol açacaktır. Ve bir forkliftin bir tekerleğinin maliyetinin 1.000 dolara kadar çıkabileceği göz önüne alındığında, bir forklifti onarmak zahmetli bir iştir.
Depo zeminleri
Üssü inşa ederken, öncekilerin tüm nüansları ve hataları dikkate alındı. Kalınlık beton döşemeçift takviyeli 200 mm idi. Geliştirici, İsveç şirketi Tremix tarafından patentli olan ve betonun kılavuzlar boyunca yerleştirildiği vakumlu döşeme teknolojisini uyguladı ve ardından vakumlu dehidrasyon ve vibro sıkıştırmaya tabi tutuldu.
ayna yüzeyi beton tabançift rotorlu helikopter makineleri ile enjeksiyon yapılarak gerçekleştirilir. Ekstra yüksek aşınma direnci elde etmek ve tozumayı ortadan kaldırmak için, Durocem'den (İtalya) "üst" bileşim olan sertleştirici bir sıvı membran oluşturucunun betonunda katkı maddeleri kullanıldı.
Bu çalışma aşaması, zeminin döşenmesi süreci kış donlarının başlangıcına denk geldiğinden, belirli zorluklara neden oldu. Beton kalitesini korumak ve üzerinde çalışmaya devam etmek iç dekorasyon, sokakta sıcaklık artışının ardından deponun ısı tabancaları "Master" ile ısıtılmasına başlandı. Betonun tüm kübik kapasitesini ısıtmak için günde 6 ton gazyağı yakmak gerekiyordu!
Sayfa 2 / 13
İle monolitik moloz duvardan masif taş, moloz beton, beton (kaplamasız ve kaplamasız) ve betonarme destekleri içerir.
taş destekler
Taş destekler eski zamanlardan beri bilinmektedir. Örneğin, MS 104'te imparator Trajan'ın altında. e. Tuna nehri üzerinde toplam uzunluğu yaklaşık 1 km olan ve açıklıkları 52 m olan bir köprü inşa edilmiştir. açıklık yapıları ahşap kemerli köprüler. Desteklerin temelleri kaya üzerine inşa edildi, ara taş desteğin kalınlığı 18 m idi - açıklığın yaklaşık üçte biri. Orta Çağ'da, Avrupa şehirlerinde genellikle masif taş sütunlara sahip kemerli köprüler inşa edildi. XX yüzyılın ilk çeyreğinde. Rusya'da, bugüne kadar hayatta kalan moloz duvar destekli kiriş bölme sisteminin birçok köprüsü inşa edilmiştir.
Taş destekler için malzeme olarak granit, kalker, kumtaşı kullanılmıştır. Ayrıca, kenarları önceden yontulmuş doğal moloz ve parke taşı ile en az 40 MPa mukavemetli katmanlı taş kayaların geliştirilmesiyle elde edilen malzemeyi kullandık. Destekler ve kil tuğlalar için kullanılır.
taş desteklerçok dayanıklı, muazzam güç rezervlerine sahipler. Bununla birlikte, şu anda, yüksek malzeme tüketimi, işin önemli emek yoğunluğu ve işin tam mekanizasyonunun imkansızlığı nedeniyle, pratik olarak inşa edilmiyorlar.
Moloz beton destekler
19. yüzyılda moloz beton destekler yaygın olarak kullanılmaktadır Bu tip desteklerde taş (ama) ana malzeme değildir, ancak beton karışımı ile birlikte beton duvarın bir bileşeni olarak hizmet eder ve hacminin yaklaşık% 40'ını oluşturur. destek. (Taşlar% 20'den fazla değilse, bunlara "kuru üzüm" denir.) Moloz beton desteklerdeki malzemelerin tüketimi: buta - 1 m3 duvar başına 0,6 m3, beton karışımı - 1 m3 başına 0,7 m3 duvarcılık. Çimento tüketimi, taş desteklerden daha fazladır - 1 m3 duvarcılık için 200-250 kg.
İş emri:
- destek gövdesinin kalıbını oluşturun ve 25-30 cm kalınlığında bir beton karışımı tabakası döşeyin;
- bireysel taşlar, beton karışımına tamamen batmayan taze döşenmiş bir tabaka üzerine serilir;
- tekrar en az 20 cm kalınlığında bir beton karışımı tabakası yayın ve tekrar tek tek taşları döşeyin, bunları tamamen beton karışımına batırmayın, vb.
Taşın boyutu desteğin kalınlığının 1/3'ünden fazla olmamalı, taş desteğin kenarından en az 10 cm uzakta olmalıdır.
Yükseklik boyunca bitişik katmanlar arasındaki temas, alt katmandan çıkıntı yapan taşlarla yeterince güvenilir bir şekilde sağlanır.
Taşla karşılaştırıldığında moloz beton destekler teknolojik olarak daha gelişmiş, daha az emek yoğun, yapımlarının hızı daha yüksektir. Ancak, inşaatları için kalıp gereklidir.
Beton ve betonarme destekler
XX yüzyılın 30'larında ülkemizde inşaatın kapsamı. köprülerin yapımında bir hızlanma talep etti. Masif taş sütunların geleneksel şekil ve boyutlarına bağlı kalarak, köprü inşaatçıları beton sütunlar inşa etmeye başladılar. Bu, işi mekanize etmeyi ve inşaatı hızlandırmayı mümkün kıldı.
Destekler tamamen granit taş kaplama veya kısmen kaplama (ön kısım) olarak inşa edilmiştir.
SNiP 2.05.03-84*'e göre, en soğuk ayın aylık ortalama hava sıcaklığının -20 °C'nin altında olduğu bölgelerde ve ortalama günlük negatif sıcaklıklarda açılan nehirlerde bulunan köprülerin ara beton desteklerinin yüzeyleri, karşı karşıya. Diğer durumlarda, mimari nedenlerle gerekmedikçe, beton desteklerin kaplanması gerekli değildir.
Ana amaç zar- duvarları buz kayması ve su-kum karışımlarının aşındırıcı etkilerinden koruyun. Yapının dayanıklılığını sağlar ve desteğe mimari açıdan çekici bir görünüm kazandırır. dış görünüş.
Desteğin yüksekliği, değişken buz kayması seviyesi içinde sıralanmıştır. Hem kontur boyunca hem de kısmen yapılabilir. - yayda.
Pirinç. 3.2 - Destek gövdesine dönük: a- cüsseli; b- menteşeli; 1 - bakan taş kaşık; 2 - aynı, tychkovy; 3 - destek gövdesinin beton çekirdeği; 4 - "kuyu"; 5 - bakan plaka; 6 - betondan serbest bırakılan bir halka; 7 - Çapa; 8 - örgü teli; 9 - beton karışımı ile doldurulmuş boşluk; 10 - destek
Buz kayması olan nehirlerde masif kaplama doğal ve yapay (beton) taşlardan. Bunun için malzeme, en az 60 MPa (güçlü bir buz kayması - 100 MPa ile) mukavemetine sahip doğal kayalar veya B 45 sınıfı beton ve F500 mukavemet ve donma direnci sınıfıdır. Taşlar, destek gövdesinin dış yüzeyi boyunca sırayla yerleştirilir ve aynı zamanda destek çekirdeğine beton karışımı serilir (Şekil 3.2, a). Taşların ön yüzeyi, yarı temiz (5 mm'ye kadar düzensizlikler) veya temiz tee (düzensizlikler yukarı) kurallarına göre kaba bir şakaya (20-50 mm taş ön yüzeyindeki düzensizlikler ile) işlenir. 2 mm'ye kadar). Her taşın cephesinin çevresi boyunca 50 mm genişliğe kadar bir şerit (“bant”) kesmek mümkündür, taşın cephe kısmının geri kalanına “kürk manto” denir.
Kaplama, destek gövdesinin temel üzerindeki konumunun jeodezik olarak işaretlenmesinden sonra desteğin köşe (veya eğrisel) kısımlarından düzenlenir. Desteğin çevresi boyunca kuru bir sıra taş serilir, her bir taş 10-15 mm olması gereken dikişin kalınlığını (duvarın sağlamlığını sağlar) sabitleyen iki ahşap takoz üzerine yerleştirilir. Taşların konumu uzlaştırıldıktan sonra dikişler çekme ile doldurulur. Destek gövdesinin çekirdeği her sıra serildikten sonra doldurulur ve katmanların daha iyi eşleşmesi için betonun üst yüzeyi taşların tepesine ulaşmamalıdır. Betonlama sırasında, beton karışımını titreştirirken, betonun taşların kuyruk kısımlarına ulaşmadığı destekten taşların hareket etmediğinden emin olun. Taşların iç yüzeyleri ile çekirdek arasında ortaya çıkan "kuyular", bir çimento-kum harcı ile dökülür. Büyük kaplama taşları, kalın bir çimento-kum harcı tabakası üzerine hemen döşenebilir (taşın altında tahta takozlar varsa).
Desteğin duvarcılığı tamamlandıktan sonra, kalafat dikişlerden çıkarılır, daha sonra dikişler yıkanır ve birleştirilir, yani. kalın plastik bir harçla doldurulur ve dikişin dış yüzeyine içbükey bir derinlik verir. 6-10 mm.
Duvar eksikliği - çok sayıda sıranın yüksekliğine eşit mesafelerde düzenlenmiş çalışma dikişleri.
Doğal kayalardan yapılmış masif kaplama son derece emek yoğundur. Modern koşullarda, destekler, kural olarak, beton bloklarla kaplı prefabrik monolitik yapılar şeklinde inşa edilir.
Orta dereceli buz kaymaları koşullarında desteklerin görünümü için yüksek gereksinimler ile, menteşeli kaplama 15-20 cm kalınlığında, doğal taş veya betonarme levhalardan (Şek. 3.2, b). Bu durumda destek kalıpta betonlanır, masif kaplamalı desteklerin karakteristik çalışma dikişleri yoktur. Kalıp söküldükten sonra sırayla kaplama plakaları monte edilir. Her biri, plakaları hafif takviye çelik halkalarla birleştiren özel ankraj braketleri ile beton desteğe sabitlenir (betonlama işlemi sırasında desteğe gömülürler).
Harç üzerine kaplama plakaları monte edilir, dikey dikişler dışarıdan doldurulur ve sıvı bir harçla dökülür. Döşeme ve desteğin çekirdeği (150-200 mm) arasındaki boşluk, döşemelerin montajı ve sabitlenmesinden sonra beton karışımı ile doldurulur. İşin tamamlanmasından sonra dikişler işlenir.
Desteklerin astarlanmasına gerek yoksa işlem şu şekilde olabilir:
- Destek gövdesinin eksenlerinin ve kontur ana hatlarının temel üzerindeki konumunun işaretlenmesi;
- Desteğin temel üst kısmının kalıbının montajı ve betonarme bir destek için takviye kafesinin montajı;
- Beton karışımının kalıba hazırlanması, teslimi ve serilmesi;
- Beton kürleme: normal sertleşmesini sağlamak için bir dizi önlemin uygulanması;
- Kalıpların sökülmesi ve destek yüzeylerinin bitirilmesi. Desteğin temel üstü kısmının yapım sürecini oluşturan çalışmalar aşağıda kısaca anlatılmıştır.
Kalıp atama.
Hacmin çoğu monolitik beton ve sıfır döngülü yapıların inşası için betonarme kullanılır ve binaların ve yapıların yer üstü kısımlarına sadece% 20 ... 25 harcanır. Monolitik yapıların en büyük verimliliği, yeniden yapılanmada kendini gösterir. endüstriyel binalar ve yapıların yanı sıra konut ve ortak inşaat yapımında. Monolitik beton kullanımı, çelik tüketimini %7...20, beton tüketimini %12'ye kadar azaltmayı mümkün kılar. Ancak aynı zamanda enerji maliyetleri de artar, özellikle de kış zamanı, ve şantiyede artan işçilik maliyetleri. Böylece binaların inşaatı sırasında şantiyede işçilik maliyetleri monolitik betonarme Büyük panel binaların yapımından 1,65 kat daha yüksek. Monolitik betondan binaların yapımında işin büyük kısmının şantiyeye düştüğü açıktır. Ancak büyük panel konut inşaatına kıyasla beton tüketimindeki %17 ... 19'luk artış, hafif betonun yetersiz kullanımı, modern döşeme yalıtımı ve daha düşük dereceli çimento kullanımı ile açıklanmaktadır.
Monolitik betonarme binaların inşası, tasarım çözümlerini optimize etmeye, elemanların ortak çalışmalarını dikkate alarak sürekli mekansal sistemlere geçmeye ve böylece kesitlerini azaltmaya izin verir. Monolitik yapılarda derz sorunu daha kolay çözülür, ısıl mühendislik ve yalıtım özellikleri artar ve işletme maliyetleri azalır.
Monolitik yapıların karmaşık montaj süreci şunları içerir:
Kalıp, donatı kafesleri, donatı-kalıp blokları, hazır beton hazırlanması için tedarik süreçleri. Bunlar esas olarak fabrika üretim süreçleridir;
İnşaat süreçleri - kalıp ve donatı montajı, beton karışımının taşınması ve yerleştirilmesi, betonun kürlenmesi, kalıbın sökülmesi.
Kalıp sistemi - rijitliğini ve stabilitesini, bağlantı elemanlarını, destekleyici yapıları, iskeleyi sağlayan kalıp ve elemanları içeren bir kavram.
Bireysel kalıp elemanlarının ve kalıp sistemlerinin türleri ve amacı:
Kalıp - monolitik yapılar için bir form;
Kalkan - bir güverte ve bir çerçeveden oluşan bir kalıp kalıbı elemanı;
güverte - şekillendirme çalışma yüzeyini oluşturan kalkanın bir elemanı;
Panjur paneli - bağlantı düğümleri ve elemanlar vasıtasıyla birbirine bağlanan ve tüm özel düzlemi şekillendirmek üzere tasarlanmış birkaç bitişik panelden oluşan düz bir kalıp elemanı;
Kalıp bloğu, çevre boyunca kapalı, tamamen düz ve köşe panellerden veya kalkanlardan oluşan bir mekansal elemandır.
Kalıp malzemesi çelik, alüminyum alaşımları, neme dayanıklı kontrplak ve ahşap levhalar, fiberglas, yüksek yoğunluklu dolgulu polipropilendir. Kalıp destek elemanları genellikle yüksek devir elde etmelerini sağlayan çelik ve alüminyum alaşımlarından yapılır.
Kombine kalıp tasarımları en verimli olanlardır. Malzemelerin belirli özelliklerinin en iyi şekilde kullanılmasına izin verirler. Kontrplak ve plastik kullanıldığında, kalıp cirosu 50 kat veya daha fazla ulaşırken, malzemenin betona düşük yapışması nedeniyle kaplamanın kalitesi önemli ölçüde artar. Çelik kalıplarda 2 ... 6 mm kalınlığında saclar kullanılır, bu da bu tür kalıpları oldukça ağır hale getirir. kalıp ahşap malzemeler sentetik kaplamalarla korunmaktadır. Filmler, ahşap emprenye için bakalit sıvı reçineler, epoksi-fenol vernikler ve fenol-formaldehit emdirilmiş cam kumaş kullanılarak sıcak presleme ile güverteye uygulanır. Şu anda en yaygın olanı, 18 ... 22 mm kalınlığında üretilen neme dayanıklı kontrplaktır. Kaplama tabakası için fiberglas, lamine plastikler, vinil plastikler kullanılır.
Ana kalıp türleri.
Kalıp, betonarme yapıların türüne bağlı olarak işlevsel amacına göre sınıflandırılır:
Duvarlar dahil dikey yüzeyler için;
Tavanlar dahil yatay ve eğimli yüzeyler için;
Duvarların ve tavanların aynı anda betonlanması için;
Betonlama odaları ve bireysel daireler için;
Kavisli yüzeyler için (esas olarak pnömatik kalıp kullanılır).
saat Beton işleri ah, kalıp sistemlerinin aşağıdaki yardımcı elemanları kullanılır.
Asma iskeleler, duvarların betonlanması sırasında bırakılan deliklere sabitlenen braketler kullanılarak cephelerin yan tarafından duvarlara asılan özel iskelelerdir.
Açılır iskeleler - sökülmeleri sırasında tünel kalıplarını veya döşeme kalıplarını çıkarmak için tasarlanmış iskeleler.
Açıcı kalıplar - monolitik yapılarda pencere, kapı ve diğer açıklıkları oluşturmak için tasarlanmış özel bir kalıp.
Monolitik yapıların üretilebilirliğini geliştirmek ve bir betonarme iş kompleksinin uygulanması için işçilik maliyetlerini azaltmak için ana talimatlar:
Betonun taşınması, döşenmesi ve sıkıştırılması için minimum işçilik maliyetlerini azaltan kimyasal katkı maddeleri içeren son derece hareketli ve dökme beton karışımlarına geçiş - el emeğini %35'ten %8'e düşürmek ve aynı anda betonlama yoğunluğunun artmasıyla, göreceli olarak beton karışımını döşemenin maliyeti önemli ölçüde azalır;
Tamamen hazırlanmış takviye kafeslerinin kullanımı, kaynaklı bağlantılardan mekanik bağlantılara geçiş - emek yoğunluğunda 1,5 ... 2 kat azalma;
Güverte temizleme ve yağlama maliyetini ortadan kaldıran özel bir polimer yapışma önleyici kaplamaya sahip modüler sistemlerin envanter, hızlı serbest bırakma kalıbının kullanılması;
Sürekli betonlama için kalıp sistemlerinin kullanılması, sabit kalıp kullanılması, sökülmesi için işçilik maliyetlerinin azaltılması veya ortadan kaldırılması.
Monolitik betonarme yapıların montajının toplam emek yoğunluğunu %100 olarak alırsak, kalıp yapımı için işçilik maliyetleri yaklaşık %45...65, donatı - %15...25 ve beton - 20.. .30%.
"SBH COTPAHC" tarafından dijital olarak hazırlanan ve sunulan makale
Karmaşık sürecin bileşimi.
Monolitik betonarme yapıların karmaşık yapım süreci, teknolojik olarak ilişkili ve sırayla gerçekleştirilen işlemlerden oluşur. basit süreçler:
Kalıp ve iskele kurulumları;
Fittings kurulumu;
Gömülü parçaların montajı;
Beton döşeme ve sıkıştırma;
Yazın beton bakımı ve kışın sertleşmesinin yoğunlaştırılması;
sıyırma;
Genellikle prefabrik yapıların bir montajı vardır.
Betonun sıyrılma mukavemeti kazanması için gereken süre genel teknolojik döngüye dahildir.
Basit süreçlerin bileşimi, emek yoğunluğu ve yürütme sırası, dikilen monolitik yapıların türüne ve özelliklerine, kullanılan mekanizmalara ve kalıp türlerine, işin teknolojik ve yerel özelliklerine bağlıdır.
Her basit süreç, entegre bir ekip halinde birleştirilen özel birimler tarafından gerçekleştirilir. Yapı, iş akışını düzenlemek için gerekli olan kulplara, planlı olarak katmanlara bölünmüştür.
Katmanlara ayrılma - betondaki kırılmaların kabul edilebilirliği ve sıcaklık ve çalışma derzlerinin oluşma olasılığı nedeniyle yüksek irtifa kesimi. Yani, tek katlı bina genellikle iki katmana ayrılır: ilk - temeller, ikincisi - diğer tüm çerçeve yapıları. AT yüksek katlı bina bir katman için, tüm katı tavanlı olarak alırlar. 4 m'den daha yüksek bir katman yüksekliği istenmez, çünkü yüksek bir yükseklik ve yoğun betonlama ile, döşenen beton karışımından kalıp üzerindeki yanal basınç artar.
Kulplara ayrılma - aşağıdakileri içeren yatay kesim:
Her basit işlemin emek yoğunluğu açısından eşdeğer, izin verilen sapma %25'ten fazla değildir;
Minimum kavrama boyutu (çalışma alanı) - bir vardiya sırasında bağlantının çalışması;
Bloğun boyutuna bağlı olarak, kesintisiz veya çalışma derzleri cihazı ile betonlanan kavramanın boyutu;
Nesne üzerindeki yakalama sayısı, iş parçacığı sayısının bir katına eşit veya katları.
Karmaşık hat içi somut çalışma sürecinin uygulanmasının net bir organizasyonu için, gereklidir:
Her sürecin karmaşıklığını belirleyin;
Nesneyi, vardiya sırasında bağlantının çalışması için yeterli olacak şekilde, her bir süreç için işgücü kapasitesi açısından benzer şekilde katmanlara ve kulplara bölün;
Akışın ritmini ve genel olarak en uygun çalışma süresini ayarlayın;
Tanımla ve seç optimal ekipman sunulması için iş yeri kalıp, donatı ve beton karışımı;
Bireysel süreçlerin karmaşıklığına, akışın kabul edilen ritmine göre gerekli işçi sayısını belirleyin ve birimleri ve ekipleri tamamlayın;
Karmaşık sürecin bir takvim (vardiya) çizelgesini hazırlayın.
Akışların havuzlanmasıyla ilgili seçenekler mümkündür. Bu nedenle, genellikle bir akış kalıbında kurulur ve takviye hemen içine monte edilir. Duvarların ve tavanların betonlanması ve ilgili işlemler bağımsız akışlara ayrıldığında ayırma da mümkündür.
Betonlama, monolitik yapıların inşa edilmesinin karmaşık sürecinde önde gelen süreçtir. Bu süreç, beton karışımının nakliyesi, işyerine teslimi, kabulü ve sıkıştırılması ile ilgili işlemlerden oluşur. Betonlama, teknolojik olarak yakından bağımlı olan kalıp ve donatı işlerinin zamanlamasını etkiler. Bu nedenle, heterojen süreçlerin farklı emek yoğunluğunda ritmik bir akış sağlamak için, her biri için farklı bir sayısal bağlantı bileşimi ile aynı çalışma süresi (betonlama süresi) alınır.
Birkaç tane geliştirmek arzu edilir. seçeneklerçalışma teknolojisi ve en uygun teknik ve ekonomik göstergelerle seçeneği kabul edin. İşlerin üretimini tasarlarken, mümkünse, ilk vardiyada yapıların betonlanması ve montajı için süreçlerin uygulanmasını sağlamalıdır.
İş tasarımının temel prensibi: kaç işlem, kaç kulp (çalışma alanları, beton blokları). Masada. 21.1, çok katlı tek bölümlü bir konut binasının katının inşası için iş üretimi için bir program gösterir. monolitik duvarlar ve prefabrik tavanlar. İş tasarlanırken, tüm inşaat süreçlerinin dört karmaşık süreçte birleştirilmesi, zemin tutuşunun yaklaşık olarak eşit miktarlarda (işgücü yoğunluğunun %25'i dahilinde) 4 çalışma alanına bölünmesi, kalıp ihtiyacının 4 kat azaltılması planlanmaktadır. - bir çalışma alanındaki betonlama hacmine .
Beton işlerinin mekanizasyonu.
Beton karışımının taşınması. Beton karışımı, beton kamyonları veya beton mikserleri ile tüketiciye yani beton çalışma alanına ulaştırılır. Beton kamyonları - 3 ... 5 m3 gövde hacmine sahip açık damperli kamyonlar, genellikle şantiyeye 10 dakika içinde bir beton santrali yerleştirildiğinde kullanılır. Beton mikser kamyonları, MAZ, KamAZ (küçük hacimler için) ve Renault, Mercedes (büyük hacimler için) gibi araçlara monte edilen 5 ... 8 m3 hacimli bir beton mikseridir. Ev tipi transmikserler iki çalışma modu ile üretilir: Sürücünün komutuyla kabinden beton karışımının cebri karıştırılması ve beton karışımının sadece araç hareket halindeyken karıştırılması. İkinci tip mikserlerin dezavantajı, uygulamalarının sınırlı kapsamıdır, yalnızca betonlamanın programa göre sıkı bir şekilde yapıldığı tesislerin yapımında, öngörülemeyen bekleme durumunda boşaltma çok daha karmaşık hale gelir.
Beton karışımının döşenmesi. Beton karışımı yapıya çeşitli şekillerde beslenir: tepsi ile, kaldırma mekanizmaları ile, beton pompaları ile. İlk iki yöntem, vardiya başına 50 m3'e kadar beton döşerken, üçüncüsü - herhangi bir hacim için kullanılır, ancak vardiya başına en az 45 m3 beton karışımı döşerken kullanmak ekonomik olarak uygundur. Örneğin, bir temel levhası dökülürken ve çukurun dibine bir araba sürme olasılığı, betonlanacak yapının seviyesinin üzerine bir beton karıştırıcı monte etmek mümkünse, tepsi boyunca beton karışımı beslenir. Tepsiler neme dayanıklı kontrplak veya 6 m uzunluğa kadar metal levhalardan yapılmıştır.Beton karışımını küvet veya bunkerlerde beslemek için diğer yükleme ve boşaltma işlemlerinde kullanılan mevcut kaldırma mekanizmaları kullanılmaktadır. Bunlar ağırlıklı olarak mobil ve kule vinçlerdir, bazen ataşman vinç kullanırlar. Kovalar 0,3 ... 1 m3 hacme sahiptir ve beton karışımını sağlama kolaylığı için, üzerine tamamen boşaltılması için bir vibratörün monte edildiği bir "cam" şeklinde yapılır.
Beton karışımını döşerken en yaygın olarak beton pompaları kullanılır. Vardiya başına 80 m3'e kadar beton döşeme hacmi ile KamAZ, MAZ, Mercedes araçlarına dayalı yerli veya ithal beton pompaları kullanılmaktadır. Kamyona monte beton pompaları, bir yükleme hunisi, bir pompa ve bir dağıtım bomu ile donatılmıştır. Beton karışımı dikey (80 m'ye kadar) ve yatay (360 m'ye kadar) yönlerde beslenir. Vardiya başına 60 m3'ten fazla beton ihtiyacı olan tesislerin yanı sıra artan kat sayısı (20 kattan fazla) olan binaların yapımında, beton finişer dağıtımı ile birlikte sabit beton pompaları kullanılmaktadır. 60 m'ye kadar erişim mesafesine sahip beton finişerler, monte edilmiş bina yapılarına veya yardımcı desteklere kurulur. Beton pompasının hunisi, içinden karışımın aktığı dikey bir boru hattı vasıtasıyla beton finişerine bağlanır. Beton finişerin bir park yerinden, birkaç kat üzerine beton serilir. Kütlesi 1...6 ton olan beton finişer tesiste kurulu bir montaj vinci ile bir sonraki otoparka taşınır, beton boru uzatılır ve beton karışımı binanın yeni kurulan katlarına beslenir. Beton karışımını sıkıştırmak için, iş teknolojisi gerektiriyorsa, çeşitli amaçlar için vibratörler kullanılır: dikey yapılar için - derin vibratörler, yatay yapılar için - titreşimli şaplar.
"Meva" şirketinin kalıbı.
Meva kalıp sistemleri. Alman şirketi "Meva", çözümde ortak olan, ancak bazılarında farklılık gösteren çeşitli kalıp türleri üretmektedir. Tasarım özellikleri. Kalıp sistemi "Meva", inşaat halindeki hem en küçük hem de büyük yapılar için herhangi bir yatay ve dikey bina yapısının kalıbı için tasarlanmıştır. Bu sistem, kendisine hak ettiği takdiri kazandıran birkaç farklı ve özgün tasarım unsuruna sahiptir. Panjur kilidi, yapısal çerçevenin herhangi bir noktasında yatay ve dikey yapılarda iki kepenk panelinin hızlı ve güvenli bir şekilde bağlanmasını sağlar. Çerçevelerin ve stifnerlerin kapalı profilleri, burulma yüklerine başarılı bir şekilde dayanan, birleştirme elemanlarının işlemlerini kolaylaştıran ve inşaat güvenliğini artıran kalıp bağlantıları oluşturur. Karşılıklı kalıp panellerinin birbirine işlevsel olarak sabitlenmesinin unsurları arasında, işçilik maliyetlerini önemli ölçüde azaltan ve tüm bağlantıları kolaylaştıran özel dişli vida bağları bulunur.
Meva kalıp levhalarının özellikleri: tüm levha çerçeveleri çelik, alüminyum veya karışık çerçeveden yapılmıştır, kavisli oluklu ve güverte elemanlarının kenarlarının güvenilir şekilde korunduğu tek parça içi boş profilden yapılmıştır. Kalıp panellerinin patentli kilitleri tüm Meva sistemlerine uygun ve güçlüdür, bu da çerçevenin herhangi bir yerinde kullanılmasına izin verir. Bir kilit uygularken, iki kalkan birlikte çekilir (altları düzleşir) ve profillerin alt kısımları ve elemanlar özel bir eğim yerlerinde bir araya getirilerek bir çekiç darbesiyle kapatılır. Kilit 2,8 kg ağırlığındadır ve tek elle takıp sabitlenebilir. Kilitteki kama, kilidin eksiksizliğini sürekli olarak sağlayan çıkarılabilir değildir. Bu yapıcı kalıp çözümünün avantajı, yalnızca panellerin değil, aynı zamanda tüm kalıp panelinin sertliğidir. Kalıp tasarımı, panellerin sadece dikey olarak değil, aynı zamanda yatay olarak da kurulmasını mümkün kılar, bu da aralıklarını azaltırken, panellerin bağlantısının sertliği ve gücü azalmaz.
a - Genel form duvar kalıbı montajı, b - kolon kalıbı, 1 - kalıp kalkanı, 2 - takviyeler, 3 - tesviye ve sıkıştırma lastikleri, 4 - çubuk ek; 5 - uzatılmış kilit, 6 - iki tahta güverte birleşimi, 7 - destek, 8 - bağlantı elemanı, 9 - kontrplak güverte, 10 - kalıp kalkanı kontur çerçevesi, 11 - kilit.
"Thyssen" şirketinin küçük panel kalıbı "Rasto". Alman şirketi Thyssen, kalıp sistemlerini yaygın olarak uyguluyor. Özellikle Rasto küçük panel kalıp, Manto büyük panel kalıp ve Sompakt levha kalıp olmak üzere birbirini tamamlayan kalıp takımları geliştirmiştir.
Kalıp "Rasto", panellerin manuel montajı için tasarlanmıştır. Kullanımı kolaydır, dayanıklıdır, 60 kN/m2'ye kadar beton karışımının basıncına dayanır, çok yönlüdür ve çeşitli inşaat alanlarında kullanılabilir.
Ana eleman 270 cm yüksekliğinde bir kalkandır, yüksek yapılar için 150 cm yüksekliğinde, 45 ila 90 cm genişliğinde ve 5 cm dereceli ek kalkanlar uygulanabilir.Kalkanların dikey ve yatay olarak birleştirilmesi kolaydır , 5 cm'lik bir modül ile uzunluk boyunca ayar yapılır, hem yatay dikişler çakıştığında hem de yer değiştirdiğinde ekran uzantısı mümkündür.
Rasto sisteminin kalıp panelleri sıcak daldırma galvanizli çelikten imal edilmiş olup, kalıp elemanları yüksek dayanım ve mukavemete sahiptir. Kalıp çerçevesi, 12 cm yüksekliğinde bir metal profilden yapılmıştır, çevresi boyunca aynı kalınlıktaki güvertenin uçlarını her taraftan koruyan 14 mm yüksekliğinde bir çıkıntıya sahiptir. Çerçeve, kalkanların genişliğine bağlı olarak her 30 cm'de bir uzunlamasına nervürlerle donatılmıştır, 1 ... 2 enine nervürü vardır. Köşe bağlantılarının belirli yerlerde bulunması, panellerin yüksek sağlamlığını ve stabilitesini sağlar ve çerçeve için içi boş profillerin kullanılması ağırlıklarını önemli ölçüde azaltır. 2,7 x 0,75 m kalkan sadece 60 kg ağırlığındadır ve elle hareket ettirilebilir ve monte edilebilir. Makale kaynağı: www.sbh.ru
Kalkanları bağlamak için evrensel kilitler (rasto sıkma) kullanılır. 40 cm uzunluğunda bir eksantrik kilit (kombi-sıkma) iki bitişik elemanı kuzu dipten uca bir çalışma dönüşünde birleştirir, beton karışımının gerilimi, olası titreşimi ve basıncını dengeler. Kelepçe sadece kalkanların hizalanmasını ve hizalanmasını sağlamakla kalmaz, bağlantının sağlamlığı kalkanların vinçle kaldırılmasına izin verir toplam alan ile 40 m2'ye kadar. “Ayakta” ve “yalan” levhaların bağlanması veya levhalar arasına 15 cm genişliğe kadar bir ek yerleştirmek gerektiğinde, 55 cm uzunluğunda uzun kilitler (sürgülü kombi kıskaçlar) kullanılır. 6 cm'ye kadar da geliştirilmiştir. Rasto", kayışın bir hareketinin kenetleme pedlerini bağlamasına izin vererek, bitişik kalkanların sıkı bir şekilde bağlanmasını sağlar. Bu eksantrik kamalı kilitlerin sökülmesi basittir ve ekstra çaba gerektirmez. Kilit bağlantıları kurulum sırasında bulunur, iki bitişik kalkan başına iki kilit ve stabiliteden ödün vermeden kolay sökme sağlar ortak sistem kalıp.
Dally'den küçük panel kalıp. Dally kalıp, kalıp panelini dikey ve yatay panellerle tamamlamayı mümkün kılan modüler elemanlardan oluşur. Kalıbın ana avantajı, minimum sayıda eleman ve orijinal bağlantı elemanından, çok çeşitli yatay ve dikey yapıların kalıbını manuel olarak monte etmenin mümkün olmasıdır. Levhalar 264, 132 ve 88 cm olmak üzere üç boyda ve 10 boyda 75 ila 20 cm arasında 5 cm gradasyonlu olarak üretilmektedir.264 x 75 cm ölçülerindeki standart levhaların kütlesi 60 kg, manuel montaj kalıp elemanlarına izin verilir. Her kalkanın uçlarında, iki bitişik kalkanın güçlü bir pim bağlantısı için iki kaynaklı altıgen somun sağlanmıştır (Şekil 22.3).
Kalıbın çalışma yüzeyi, her bir kalıp elemanının düzenli temizlik ve yağlama ile en az 350 kez kullanılmasına izin veren, çift taraflı güçlendirilmiş kaplamaya sahip 21 mm kalınlığında 5 katmanlı bir ahşap levhadır. Kalkanların çerçeve elemanları, çerçeveyi oldukça sert yapan kaplamalar ve eşarplar ile çelik sacdan yapılmıştır, ancak bu çözüm kalkanın ağırlığını önemli ölçüde azaltabilir. Her kalkan sadece iki bağlantı çubuğuyla bağlanır,
Dally'den küçük panel duvar kalıbı:
a - seri elemanlar; b - iki kalkanın birleşimi; 1 - kalkanların sertleştirici elemanları; 2 - karşı kalkanları monte etmek için oluk; 3 - tesviye lastiği
Yerli kalıplar arasında TsNIIOMTP Enstitüsü tarafından geliştirilen birleşik kalıp en yaygın olanıdır. Duvar kalıbı, 300 ila 1800 mm modüler genişliğe sahip bir kat yüksekliğindeki levhaların yanı sıra ek levhalardan - uç ve köşeden oluşur. Kalkan metal bir güverte, yatay kirişler ve dikey makaslardan oluşur. Kalkanların alt kısmında vidalı krikolar bulunur. Kalıpta 3 m yüksekliğe kadar 12, 16 ve 20 cm kalınlığında beton duvarlar ve 10 ... 22 cm kalınlığında tavanlar yapmak mümkündür.
Monolitik örtüşme duvarların montajından sonra takım elbise ve onlar tarafından gerekli başlangıç gücünü ayarlayın. Döşeme kalıbı teleskopik payandalara monte edilir, iki kademede donatı ağları döşenir ve betonlama yapılır.
Katlanabilir kalıp elemanları:
1 - sütunların ahşap çerçeveleri; 2 - kolon kalıbı; 3, 4 - kalıp panelleri; 5 - kirişlerin tabanının kalkanı; 6 - ahşap kalıp kirişleri; 7 - kiriş kalıbının yan panelleri; 8 - tripodlarda teleskopik rafların desteklenmesi.
İşin organizasyonu ve teknolojik özellikler çeşitli kalıplar ve kalıp sistemleri monolitik konut inşaatı bölümünde ele alınmıştır. Beton ve betonarme monolitik yapılardan binaların inşası spesifiktir ve tuğla, prekast beton, ahşap ve metal yapılardan yapılmış bina ve yapıların yapımından farklıdır. Sözde "ıslak işlemler"in varlığı, beton yapıların güç kazanması için kürleme ihtiyacı, üretimlerinin özelliklerini belirler.
Betonlama bölgesinin bölümlere, katmanlara, tugayların ve birimlerin işe alınmasına, bir betonarme iş kompleksinin hat içi üretiminin organizasyonuna dikkat edilir.
Dört ana gruba ayrılan beton işleri için kullanılan çok çeşitli kalıpların kullanım özellikleri: açılır-kapanır, yatay ve düşey hareketli ve pnömatik, sabit ve ısıtmalı özel kalıp olarak adlandırılan kalıplar şunlardır: düşünülen.
1. MONOLİTİK BETONDAN YAPILARIN YAPILMASININ YAPI VE YAPISAL ÖZELLİKLERİ.
1.1 Kalıbın amacı.
Monolitik beton ve betonarme hacminin çoğu, sıfır döngülü yapıların inşası için kullanılır ve binaların ve yapıların yer üstü kısımlarına sadece% 20 ... 25 harcanır. Monolitik yapıların en büyük verimliliği, endüstriyel bina ve yapıların yeniden inşasında ve ayrıca konut ve ortak inşaat tesislerinin yapımında kendini gösterir. Monolitik beton kullanımı, çelik tüketimini %7...20, beton tüketimini %12'ye kadar azaltmayı mümkün kılar. Ancak aynı zamanda özellikle kış aylarında enerji maliyetleri artar ve şantiyede işçilik maliyetleri artar. Bu nedenle, monolitik betonarme binaların inşası sırasında şantiyedeki işçilik maliyetleri, büyük panel binaların yapımından 1.65 kat daha yüksektir. Monolitik betondan binaların yapımında işin büyük kısmının şantiyeye düştüğü açıktır. Ancak büyük panel konut inşaatına kıyasla beton tüketimindeki %17 ... 19'luk artış, hafif betonun yetersiz kullanımı, modern döşeme yalıtımı ve daha düşük dereceli çimento kullanımı ile açıklanmaktadır.
Monolitik betonarme binaların inşası, tasarım çözümlerini optimize etmeye, elemanların ortak çalışmalarını dikkate alarak sürekli mekansal sistemlere geçmeye ve böylece kesitlerini azaltmaya izin verir. Monolitik yapılarda derz sorunu daha kolay çözülür, ısıl mühendislik ve yalıtım özellikleri artar ve işletme maliyetleri azalır.
Monolitik yapıların karmaşık montaj süreci şunları içerir:
Kalıp, donatı kafesleri, donatı-kalıp blokları, hazır beton hazırlanması için tedarik süreçleri. Bunlar esas olarak fabrika üretim süreçleridir;
İnşaat süreçleri - kalıp ve donatı montajı, beton karışımının taşınması ve yerleştirilmesi, betonun kürlenmesi, kalıbın sökülmesi.
kalıp sistemi- rijitliğini ve stabilitesini sağlayan kalıp ve elemanları, bağlantı elemanlarını, destekleyici yapıları, iskeleyi içeren bir konsept.
Bireysel kalıp elemanlarının ve kalıp sistemlerinin türleri ve amacı:
kalıp- monolitik yapılar için form;
kalkan- bir güverte ve bir çerçeveden oluşan kalıp elemanının oluşturulması;
güverte- oluşturan çalışma yüzeyini oluşturan kalkanın bir elemanı;
kalıp paneli- bağlantı düğümleri ve elemanlar vasıtasıyla birbirine bağlanan birkaç bitişik panelden oluşan ve tüm özel düzlemin kalıplanması için amaçlanan bir şekillendirici düz kalıp elemanı;kalıp bloğu- Çevre boyunca kapalı, tamamen düz ve köşe paneller veya kalkanlardan oluşan bir mekansal eleman.
Kalıp malzemesi çelik, alüminyum alaşımları, neme dayanıklı kontrplak ve ahşap levhalar, fiberglas, yüksek yoğunluklu dolgulu polipropilendir. Kalıp destek elemanları genellikle yüksek devir elde etmelerini sağlayan çelik ve alüminyum alaşımlarından yapılır.
Kombine kalıp tasarımları en verimli olanlardır. Malzemelerin belirli özelliklerinin en iyi şekilde kullanılmasına izin verirler. Kontrplak ve plastik kullanıldığında, kalıp cirosu 50 kat veya daha fazla ulaşırken, malzemenin betona düşük yapışması nedeniyle kaplamanın kalitesi önemli ölçüde artar. Çelik kalıplarda 2 ... 6 mm kalınlığında saclar kullanılır, bu da bu tür kalıpları oldukça ağır hale getirir. Ahşap malzemelerden yapılan kalıplar sentetik kaplamalarla korunmaktadır. Filmler, ahşap emprenye için bakalit sıvı reçineler, epoksi-fenol vernikler ve fenol-formaldehit emdirilmiş cam kumaş kullanılarak sıcak presleme ile güverteye uygulanır. Şu anda en yaygın olanı, 18 ... 22 mm kalınlığında üretilen neme dayanıklı kontrplaktır. Kaplama tabakası için fiberglas, lamine plastikler, vinil plastikler kullanılır.
Özellikle fiberglass takviyeli plastik kalıplar kullanılmaktadır. Statik yük dayanımı yüksektir ve betonla kimyasal olarak uyumludur. Polimerik malzemelerden yapılmış kalıplar, düşük ağırlık, şekil stabilitesi ve korozyona karşı direnç ile ayırt edilir. Olası hasarlar yeni bir kaplama uygulanarak kolayca onarılabilir. Plastik kalıbın dezavantajı, ısıl işlem sırasında 60°C'ye kadar sıcaklık artışıyla taşıma kapasitelerinin keskin bir şekilde azalmasıdır.
Metal güverteye polipropilen levha uygulandığında birleşik kalıplar ortaya çıktı. İletken dolgulu kompozitlerin kullanılması, beton üzerinde kontrollü termal etki modları ile ısıtma kaplamalarının elde edilmesini mümkün kılar.
Makale şirket tarafından dijital olarak hazırlanmış ve gönderilmiştir.
1.2 Ana kalıp türleri.
Kalıp, betonarme yapıların türüne bağlı olarak işlevsel amacına göre sınıflandırılır:
Duvarlar dahil dikey yüzeyler için;
Tavanlar dahil yatay ve eğimli yüzeyler için;
Duvarların ve tavanların aynı anda betonlanması için;
Betonlama odaları ve bireysel daireler için;
Kavisli yüzeyler için (esas olarak pnömatik kalıp kullanılır).
Duvarları betonlamak için aşağıdaki tiplerde kalıplar kullanılır: küçük panel, büyük panel, blok form, blok ve kayar.
Döşemelerin betonlanması için, destek elemanlarına sahip küçük bir panel kalıp ve kalıp yüzeylerinin tamamen bir vinç tarafından yeniden düzenlenmiş tek bir kalıp bloğu oluşturduğu büyük panel bir kalıp kullanılır.
Duvarların ve tavanların veya bir binanın bir kısmının aynı anda betonlanması için hacimsel ayarlanabilir kalıp kullanılır. Aynı amaçlar için, dikey, yatay ve eğimli yüzeylerin betonlanması için kullanılabilen, yuvarlanan kalıp dahil olmak üzere yatay olarak hareketli kalıp kullanılır.
Katlanabilir küçük panel kalıp 3 m2'ye kadar alana ve 50 kg'a kadar ağırlığa sahip bir dizi küçük elemandan oluşur, bu da bunları manuel olarak kurmanıza ve sökmenize olanak tanır. Kalıp elemanları monte edilebilir büyük paneller ve kurucu elemanlara demonte edilmeden bir vinç tarafından monte edilen ve sökülen bloklar. Kalıp birleşiktir, sabit, değişken ve tekrar eden boyutlara sahip çok çeşitli monolitik yapılar için geçerlidir. Küçük hacimli standart olmayan yapıların betonlanması için kalıp kullanılması en çok tavsiye edilir.
Büyük panel kalıp büyük boyutlu kalkanlar ve bağlantı elemanlarından oluşur. Kalıp panoları, ek taşıyıcı ve destekleyici elemanlar kurmadan tüm teknolojik yükleri algılar. Genişletilmiş duvarların, tavanların ve tünellerin betonlanmasında kalıp kullanılır. Kalkanların boyutu, betonlanacak yapının boyutuna eşittir: duvarlar için - odanın genişliği ve yüksekliği, zemin için - bu katın genişliği ve uzunluğu. Geniş bir alanın beton zeminleri olması durumunda, yapının betonunu bir vardiyada döşemek ve sıkıştırmak mümkün olmadığında, zemin haritalara bölünür. Kartın boyutları teknolojik düzenlemeler tarafından belirlenir, sonraki kartlara yeterli yapışmayı sağlamak için sınırlarına 10 x 10 mm hücreli 2 ... 4 mm kalınlığında bir metal ağ yerleştirilir. Monolitik duvarları ve bölmeleri, prefabrik tavanları olan binalar için geniş panel kalıp önerilir. Katlanabilir büyük panel kalıp, değişken kesitli yapıların betonlanması için de kullanılır (silolar, bacalar, soğutma kuleleri).blok kalıp- bu, üst üste binen bir cihaz olmadan bir bina hücresinin konturu boyunca aynı anda üç veya dört duvarın inşası için tasarlanmış hacim ayarlı bir kalıptır. Kalıp, dikilen duvarların kalınlığına eşit boşluklarla ayrı bloklardan monte edilir.
Monolitik dış ve iç taşıyıcı duvarlara ve prefabrike tavanlara sahip binalar için, birleşik bir varyant önerilir: duvarların dış yüzeyleri için - büyük panel kalıp ve iç yüzeyler ve duvarlar için - blok, dikey olarak hareketli ve çıkarılabilir kalıp.
Blok Formları uzaysal kapalı bloklardır: tek parça ve sert, bir koni üzerinde yapılmış, ayrılabilir veya kayar (yeniden yapılandırılabilir). Blok kalıplar, nispeten küçük hacimli kapalı yapıların sadece dikey değil, aynı zamanda yatay yüzeyler için de betonlanması için kullanılır. Ayrıca, duvarların, asansör boşluklarının, bağımsız temellerin, kolonların vb. hacimsel elemanları için kullanılırlar.
Değişken kalıp U-şekilli bölümlerden oluşur ve duvarların ve tavanların aynı anda betonlanması için tasarlanmış yatay olarak çıkarılabilir büyük boyutlu bir bloktur. Sıyırma sırasında, bölümler içe doğru kaydırılır (sıkıştırılır) ve bir vinç tarafından daha sonra çıkarılması için açıklığa doğru yuvarlanır. Bu kalıp, konut ve sivil binaların enine taşıyıcı duvarlarını ve monolitik tavanlarını betonlamak için kullanılır. Bu tip uzunlamasına hareket eden kalıp, monolitik uzunlamasına taşıyıcı duvarlara ve monolitik betonarme tavanlara sahip binalarda uygulama bulmuştur.
Planda basit bir konfigürasyona, geniş bir taban alanına ve cephelerin düz yüzeylerine sahip binalar için hacimsel ayarlanabilir kalıplar önerilir - tünel, dikey ve yatay hareketli kalıplar.
tünel kalıbı- binanın iki enine ve bir boyuna duvarının aynı anda dikilmesi ve bu duvarların üzerine bindirilmesi için tasarlanmış hacimsel ayarlanabilir kalıp. Tünel, yatay ve dikey kalkanları hızlı açılan kilitlerle birbirine bağlanarak karşılıklı iki yarım tünelden oluşturulabilir. Tünel tipi kalıp, çoğunlukla monolitik iç duvarları, monolitik tavanları ve menteşeli cephe panelleri olan binalar için kullanılır.
yatay kalıp yatay olarak uzatılmış yapıların ve yapıların yanı sıra geniş bir çevreye sahip kapalı bir bölümün yapılarını betonlamak için tasarlanmıştır.
kayar kalıp yüksek binaların ve yapıların duvarlarını betonlamak için kullanılır. Duvarların çevresi boyunca monte edilen ve betonlama ilerledikçe hidrolik krikolar tarafından kaldırılan mekansal bir kalıptır.
Kat sayısı fazla olan ve basit bir iç yerleşim planına sahip nokta (kule) tipi binalar için dikey olarak çıkarılabilir blok tipi kalıp veya kayar kalıp tavsiye edilir.
Pnömatik kalıp- Yapının boyutlarına göre kesilmiş esnek, hava geçirmez kabuk. Kalıp çalışma konumuna getirilir, içeride aşırı hava veya diğer gaz basıncı oluşturulur ve betonlanır. Bu tür kalıplar, nispeten küçük hacimli ve eğrisel ana hatların betonarme yapıları için geçerlidir.
Sabit kalıp Sıyırma yapmadan yapıların dikilmesinde, kaplama oluşturulmasında ve ayrıca termal ve su yalıtımında kullanılır.
Beton işleri sırasında kalıp sistemlerinin aşağıdaki yardımcı elemanları kullanılır.
asma platformu- Duvarların betonlanması sırasında bırakılan deliklere sabitlenen braketler yardımıyla cephelerin yan tarafından duvarlara asılan özel iskeleler.
Açılır iskele- Sökülmeleri sırasında tünel kalıplarını veya döşeme kalıplarını çıkarmak için tasarlanmış iskeleler.
açılış şekillendiriciler- monolitik yapılarda pencere, kapı ve diğer açıklıkları oluşturmak için tasarlanmış özel bir kalıp.Monolitik yapıların üretilebilirliğini geliştirmek ve bir betonarme iş kompleksinin uygulanması için işçilik maliyetlerini azaltmak için ana talimatlar:
Betonun taşınması, döşenmesi ve sıkıştırılması için minimum işçilik maliyetlerini azaltan kimyasal katkı maddeleri içeren son derece hareketli ve dökme beton karışımlarına geçiş - el emeğini %35'ten %8'e düşürmek ve aynı anda betonlama yoğunluğunun artmasıyla, göreceli olarak beton karışımını döşemenin maliyeti önemli ölçüde azalır;
Tamamen hazırlanmış takviye kafeslerinin kullanımı, kaynaklı bağlantılardan mekanik bağlantılara geçiş - emek yoğunluğunda 1,5 ... 2 kat azalma;
Güverte temizleme ve yağlama maliyetini ortadan kaldıran özel bir polimer yapışma önleyici kaplamaya sahip modüler sistemlerin envanter, hızlı serbest bırakma kalıbının kullanılması;
Sürekli betonlama için kalıp sistemlerinin kullanılması, sabit kalıp kullanılması, sökülmesi için işçilik maliyetlerinin azaltılması veya ortadan kaldırılması.
Monolitik betonarme yapıların montajının toplam emek yoğunluğunu %100 olarak alırsak, kalıp yapımı için işçilik maliyetleri yaklaşık %45...65, donatı - %15...25 ve beton - 20.. .30%.
Makale şirket tarafından dijital olarak hazırlanmış ve gönderilmiştir.
2. KOMPLE BETON ÜRETİMİ VE BETONARME İŞLERİ.
2.1 Karmaşık sürecin bileşimi.
Monolitik betonarme yapıların karmaşık yapım süreci, teknolojik olarak ilişkili ve sırayla gerçekleştirilen basit süreçlerden oluşur:
Kalıp ve iskele kurulumları;
bağlantı parçaları kurulumu;
gömülü parçaların montajı;
beton karışımının döşenmesi ve sıkıştırılması;
betonun yazın bakımı ve kışın sertleşmesinin yoğunlaştırılması;
sıyırma;
genellikle prefabrik yapıların bir montajı vardır.
Betonun sıyrılma mukavemeti kazanması için gereken süre genel teknolojik döngüye dahildir.
Basit süreçlerin bileşimi, emek yoğunluğu ve yürütme sırası, dikilen monolitik yapıların türüne ve özelliklerine, kullanılan mekanizmalara ve kalıp türlerine, işin teknolojik ve yerel özelliklerine bağlıdır.
Her basit süreç, entegre bir ekip halinde birleştirilen özel birimler tarafından gerçekleştirilir. Yapı, iş akışını düzenlemek için gerekli olan kulplara, planlı olarak katmanlara bölünmüştür.
katmanlama- betonda kırılmaların kabul edilebilirliği ve sıcaklık ve çalışma derzlerinin oluşma olasılığı nedeniyle yüksek irtifa kesimi. Bu nedenle, tek katlı bir bina genellikle iki katmana ayrılır: birincisi temeller, ikincisi ise diğer tüm çerçeve yapılardır. Çok katlı bir binada, katlı bir kat kat olarak alınır. 4 m'den daha yüksek bir katman yüksekliği istenmez, çünkü yüksek bir yükseklik ve yoğun betonlama ile, döşenen beton karışımından kalıp üzerindeki yanal basınç artar.
Kavramalara ayrılma- aşağıdakileri içeren yatay kesim:
Her basit işlemin emek yoğunluğu açısından eşdeğer, izin verilen sapma %25'ten fazla değildir;
en küçük beden kulplar (çalışma alanı) - bir vardiya sırasında bağlantının çalışması;
bloğun boyutuna bağlı olarak, kesintisiz veya çalışma derzleri cihazı ile betonlanan yakalamanın boyutu;
nesne üzerindeki yakalama sayısı, iş parçacığı sayısının bir katına eşit veya katları.
Bir vardiyanın ortasında bir işçi bağlantısının bir kavramadan diğerine geçişi istenmeyen bir durumdur. Kulpların boyutu genellikle bina bölümünün uzunluğuna karşılık gelir veya tam sayıda yapısal eleman içermelidir - temeller, kolonlar, diğer yapılar veya çalışma ve genleşme derzlerinin yapımı için belirlenen bölümlerin sınırları tarafından belirlenir.
Karmaşık hat içi somut çalışma sürecinin uygulanmasının net bir organizasyonu için, gereklidir:
Her sürecin karmaşıklığını belirleyin;
nesneyi, vardiya sırasında bağlantının çalışması için yeterli olacak şekilde, her bir süreç için emek kapasitesi açısından benzer şekilde katmanlara ve kulplara ayırın;
akışın ritmini ve genel optimal çalışma süresini belirlemek;
işyerine kalıp, donatı ve beton karışımı sağlamak için en uygun ekipmanı belirlemek ve seçmek;
bireysel süreçlerin karmaşıklığına, akışın kabul edilen ritmine göre gerekli işçi sayısını belirlemek ve birimleri ve ekipleri tamamlamak;
karmaşık sürecin bir takvim (vardiya) çizelgesini hazırlayın.
Akışların havuzlanmasıyla ilgili seçenekler mümkündür. Bu nedenle, genellikle bir akış kalıbında kurulur ve takviye hemen içine monte edilir. Duvarların ve tavanların betonlanması ve ilgili işlemler bağımsız akışlara ayrıldığında ayırma da mümkündür.
Betonlama, monolitik yapıların inşa edilmesinin karmaşık sürecinde önde gelen süreçtir. Bu süreç, beton karışımının nakliyesi, işyerine teslimi, kabulü ve sıkıştırılması ile ilgili işlemlerden oluşur. Betonlama, teknolojik olarak yakından bağımlı olan kalıp ve donatı işlerinin zamanlamasını etkiler. Bu nedenle, heterojen süreçlerin farklı emek yoğunluğunda ritmik bir akış sağlamak için, her biri için farklı bir sayısal bağlantı bileşimi ile aynı çalışma süresi (betonlama süresi) alınır.
Çalışma teknolojisi için birkaç olası seçenek geliştirmek ve seçeneği en uygun teknik ve ekonomik göstergelerle kabul etmek arzu edilir. İşlerin üretimini tasarlarken, mümkünse, ilk vardiyada yapıların betonlanması ve montajı için süreçlerin uygulanmasını sağlamalıdır.
İş tasarımının temel prensibi: kaç işlem, kaç kulp (çalışma alanları, beton blokları). Masada. 21.1, monolitik duvarlara ve prefabrik tavanlara sahip çok katlı konut tek bölümlü bir binanın katının inşası için çalışma programını gösterir. İş tasarlanırken, tüm inşaat süreçlerinin dört karmaşık süreçte birleştirilmesi, zemin tutuşunun yaklaşık olarak eşit miktarlarda (işgücü yoğunluğunun %25'i dahilinde) 4 çalışma alanına bölünmesi, kalıp ihtiyacının 4 kat azaltılması planlanmaktadır. - bir çalışma alanındaki betonlama hacmine .
Tablo 21.1. İŞLERİN ÜRETİM TAKVİMİ (AKSESUAR-MONOLİT), 1 SET, 12 GÜN.
İşlerin üretimi için program tasarlanırken, işin entegre bir ekip tarafından iki vardiya halinde, betonlama - sadece ilk vardiyada gerçekleştirileceği dikkate alındı. Komşu sahadaki teknoloji sadece betonun kürlenme sürecini kontrol ettiğinde kurulum bir "pencerede" gerçekleştirilecektir. Prefabrik yapıların döşenmesinden en az iki gün önce, yazın sıyırma işleminden önce duvarların betonunun kürlenmesi için bir gün yeterli olduğu öngörülmektedir. Kurulumun kendisini zamanında ertelemeniz ve duvar kalıbını bu çalışma alanına, ancak bir sonraki katta (kat) kurmadan önce gerçekleştirmeniz önerilir. Bir alandaki çalışma süresi, bu alandaki perde kalıbının kurulumunun başlangıcından bitişikteki duvar kalıbının montajının başlangıcına kadar alınır, süre bir kalıp seti ile 4 ve 3 gün olacaktır. , ve iki set ile 2 gün; 1.5 ve 1 gün. Böyle bir ritimle, kavrama üzerindeki çalışma süresi, iki set ile 16 ve 12 günlük bir set ile sağlanır - sırasıyla 8; 6 ve 4 gün.
İlgili çalışma programı tasarlanırken, iki çalışma bölümüne dayalı bir kalıp setinin kullanılması sağlanır (Tablo 21.2). İki takım kalıp, sabit sayıda işçi ile - vardiya başına 10 kişi, Daha iyi koşullar betonun kürlenmesi için (iki gün sonra deforme olur), kelepçe üzerindeki çalışma döngüsü 12 günden 8 güne düşürülür, betonlama ve montaj sadece ilk vardiyada yapılabilir.
Tipik bir zeminin inşası için üretim programı monolitik bina bir çalışma alanı için bir takım kalıp ile tabloda verilmiştir. 21.3. Tüm inşaat süreçleri de 8 karmaşık olana ayrılmıştır:
1) basamak kalıbının montajı ve takviye kafeslerinin montajı;
2) duvarların betonlanması;
3) beton duvarların dayanım kazancının korunması ve izlenmesi;
4) duvar kalıbının sökülmesi, onarımı, gerekirse yağlanması;
5) tavan kalıbının montajı, takviye ağlarının ve çerçevelerin döşenmesi;
6) zeminlerin betonlanması;
7) beton zeminlerin kürlenmesini sağlamak ve izlemek;
8) döşeme kalıp sökme, onarım, yağlama.
Süreçlerin zamanında birbirine bağlanması, gerekli ardışık süreçlerin üç çalışma alanı içerisinde gerçekleştirilebilmesini sağlar:
Çalışma alanı başına 3 günlük bir ritimle 12 günde zemindeki tüm iş setinin tamamlanmasını sağlamak;
entegre ekibin yapısını değiştirmeden komşu bölgelerdeki bireysel süreçlerin birleştirilmesini ve paralel yürütülmesini organize edin: işçiler için günlük ihtiyaç: 10 kişi;
Kalıp panelleri sökülmeden önce öngörülen beton kür süreleri içinde (duvarlar için bir gün ve tavanlar için iki gün), beton sertleştirme yoğunlaştırma kaynakları kullanılmadan, yaz koşullarında sıyırma mukavemeti kazanır.
Tablo 21.2 İŞLERİN ÜRETİM PROGRAMI (MONLİT-MONOLİT), 2 TAKIM, 8 GÜN.
Tablo 21.3 ÇALIŞMA PROGRAMI (MONOLİT), 1 SET, 12 GÜN.
Döşeme bölümünün betonlanmasından sonra, işçilerin bir sonraki katın duvarlarının kalıbını kurmak için bu sahaya dönmesi 7,5 gün sürer, bu süre betonun markalı mukavemetin %70'ini kazanması için yeterlidir.
İşin tasarımı ve organizasyonu için uygun, iki günlük modüler bir döngüdür. Bu süre zarfında, bir işçi ekibi tek vardiyada kalıbı şantiyede söker ve gerekirse onarır; iki vardiyada (gün içinde) ertesi günün ilk vardiyasında betonlama yapacağı komşu alana kalıp ve donatı kafeslerini kuruyor. Bu alandaki sonraki dört vardiya betonun kürlenmesidir, bu süre zarfında ekip başka bir alanda (kalıp montajı, donatı ve betonlama) benzer bir dizi işlemi gerçekleştirir. İki takım kalıp varlığında ve bir ekip çalışması ile kavramadaki çalışma döngüsü 16 gün olacak, bu süre zarfında iki ekip iki kattaki işi tamamlayabilecektir.
Tipik bir katın monolitik yapılarının inşası ile ilgili işlerin bir ekip tarafından üretilmesine ilişkin program Tablo'da verilmiştir. 21.4. İki kalıp setinin varlığı, aşağıdaki işlem sırasını sağlamanıza izin verir:
1) ilk bölümde duvar kalıbı ve donatı kurulur;
2) Birinci bölümde duvarların betonunun kürlenmesi sürecinde ekip dördüncü bölüme geçer, tavanların kalıplarını söker, üçüncü bölümde duvarların kalıplarını kurar ve donatıyı döşer;
3) Üçüncü bölümde duvarların betonunun kürlenmesi sürecinde, ekip ilk bölüme döner, burada duvar kalıbını söker, kalıp ve zemin donatısını kurar, bu zemini betonlar vb.
Tablo 21.4 ÜRETİM PROGRAMI (MONOLİT), 2 SET, 16 GÜN.
Bu çözümün başlıca avantajları, bir ekibin iki gün boyunca sabit bir ritimde çalışması, betonlamanın sadece ilk vardiyada yapılması, her bölümde duvar ve tavanlar için yükleme öncesi kür süresinin 16 gün olmasıdır.
Aynı ritim için işlerin iki günde üretilmesi için program, tüm iş kompleksinin 8 günde iki ekibin çalışmasıyla yerde uygulanması Tabloda verilmiştir. 21.5. Kavramayı dört çalışma alanına bölerken iş organizasyonunun ayırt edici özellikleri:
işçilerin ilk tugayı 1 ve 2 numaralı çalışma bölümlerine, ikinci - 3 ve 4 numaralı bölümlere hizmet eder;
serbest bırakılan kalıbın birinci bölümden üçüncü bölüme taşınması planlanmaktadır, ikinci kalıp seti 2 ve 4 numaralı çalışma bölümlerine hizmet vermektedir.
Tablo 21.5 ÜRETİM PROGRAMI (MONOLİT), 2 SET, 8 GÜN.
Uygulanan teknolojinin dezavantajı, betonun şantiyeye ulaştırılması ve montaj sahasına ulaştırılmasındaki zorluklar nedeniyle komşu alanlarda duvar ve tavanların aynı anda betonlanması olabilir. Ekiplerin çalışması için günlük zaman değişimi, yalnızca ilk vardiyada beton dökümüne izin verir.
Modern koşullarda, evrensel kalıp sistemlerinin kullanımıyla, 6 ve 4 gün içinde zemin yapılarının betonlanmasıyla yüksek hızlı inşaat giderek daha fazla tanıtılmaktadır. Bağımsız ekiplerin beton duvarlar ve zeminler üzerindeki çalışmalarını zamanında bağlamak için ilgili programlar Tablo'da sunulmuştur. 21.6 ve 21.7.
Tablo 21.6 ÜRETİM PROGRAMI (MONOLİT), 2 SET, 6 GÜN.
Tablo 21.7 ÇALIŞMA PROGRAMI (MONOLİT), 2 TAKIM, 2 SET, 6 GÜN.
Beton döşeme hızına bağlı olarak, bu işlem için gerekli makine seti seçilir, aynı hızda, kendileri için kabul edilen mekanizma ve cihazlarda kalıp ve güçlendirme işlemleri yapılmalıdır. Beton karışımlarının döşenme hızı, hareketliliklerinden büyük ölçüde etkilenir. Uygulamak döküm karışımları koni taslağı (OK) 12 cm'den (genellikle 14 ... 18 cm) fazla olan, mobil OK ile = 2...12 cm, yerleşik OK ile = 0,5...2 cm ve sert OK = 0 cm ile. özelliklesert 200 s'den fazla sertlik indeksi (LI) olan karışımlar. Dökme karışımları kullanırken titreşimsiz bir betonlama yöntemi kullanılır.
Uzun duvarlarla sürekli betonlama sağlamak için, sınırlarda metal çok hücreli bir ağdan dikey bölme kesimlerinin yerleştirilmesiyle 14 ... 16 m uzunluğa kadar bölümlere ayrılması önerilir.
Çok katlı monolitik konut binalarının yapıları, büyük panel, hacim ayarlı, kayar ve diğer kalıp türlerinde betonlanabilir. Seçilen seçeneğin, kalıbın kurulum ve sökülme sürecini mekanize etmesine izin vermesi önemlidir.
En iyi seçenek mekanizasyon üç ana gösterge tarafından belirlenir: çalışma süresi; işin emek yoğunluğu; 1 m3 serilmiş beton başına iş maliyeti.
Betonlama için önde gelen akışın (işlemin) performansına göre, diğer akışlar için bir dizi makine seçilir - kalıp montajı, donatı montajı vb. sadece ana ekipmanın yüksek performanslı kullanımını sağlamanız gerekir. Böylece, vinç tüm ana süreçlerde yer alabilir - iş yerine kalıp, takviye, beton karışımı sağlama, sıyırma.
Özel akışlar ve bağlantılarla çalışmak, kalıp setinin ve vinç ekipmanının daha verimli kullanılmasını sağlar, teknolojik kesintileri ortadan kaldırır ve işin ritmini ve kalitesini artırır.
Kavrayıcı üzerindeki kalıbın demontajı yaz koşullarında ve kışın - ısıl işlemden sonra - ancak sıyırma mukavemeti kazanıldığında yapılabilir. Kalıbın sökülmesi, kurulumunun tersi sırayla gerçekleştirilir. Beton duvarlar için 50 kg/cm2 ve zeminler için 100 kg/cm2 dayanım kazandığında, sıyrılmış yapıların yüklenmesine izin verilir.
Bir kat yüksekliğe kadar betonarme yapıların inşası (monolitik temeller, istinat duvarları, temiz zeminler veya beton hazırlama) veya bir binanın zemininin betonlanması üzerindeki toplam çalışma süresi:
T \u003d t (m + n -1) + tb
nerede T - toplam çalışma süresi, gün; t- akış ritmi, günler; m, yakalama sayısıdır (çalışma alanları); P- yürütülen basit işlemlerin sayısı; tb- kalıpta betonun sertleşme süresi, günler.
Buradan, önceden belirlenmiş bir çalışma süresi ile gerekli yakalama sayısını belirleyebilirsiniz:
m \u003d (T - tb) / t - p + 1.
2.2. BETON İŞLERİN MEKANİZASYONU
Makale şirket tarafından dijital olarak hazırlanmış ve gönderilmiştir.
Beton karışımı emtia beton fabrikalarında yapılır. Bir şantiyenin ayda 3000 m3'ten fazla beton tüketmesi ve yerinde beton santrali (ünitesi) kurulmasının mümkün olması durumunda, inşaatı ekonomik olarak yapılabilir.
Beton karışımının taşınması. Beton karışımı, beton kamyonları veya beton mikserleri ile tüketiciye yani beton çalışma alanına ulaştırılır. Beton kamyonları - 3 ... 5 m3 gövde hacmine sahip açık damperli kamyonlar, genellikle şantiyeye 10 dakika içinde bir beton santrali yerleştirildiğinde kullanılır. Beton mikser kamyonları, MAZ, KamAZ (küçük hacimler için) ve Renault, Mercedes (büyük hacimler için) gibi araçlara monte edilen 5 ... 8 m3 hacimli bir beton mikseridir. Ev tipi transmikserler iki çalışma modu ile üretilir: Sürücünün komutuyla kabinden beton karışımının cebri karıştırılması ve beton karışımının sadece araç hareket halindeyken karıştırılması. İkinci tip mikserlerin dezavantajı, uygulamalarının sınırlı kapsamıdır, yalnızca betonlamanın programa göre sıkı bir şekilde yapıldığı tesislerin yapımında, öngörülemeyen bekleme durumunda boşaltma çok daha karmaşık hale gelir.
Beton karışımının döşenmesi. Beton karışımı yapıya çeşitli şekillerde beslenir: tepsi ile, kaldırma mekanizmaları ile, beton pompaları ile. İlk iki yöntem, vardiya başına 50 m3'e kadar beton döşerken, üçüncüsü - herhangi bir hacim için kullanılır, ancak vardiya başına en az 45 m3 beton karışımı döşerken kullanmak ekonomik olarak uygundur. Örneğin, bir temel levhası dökülürken ve çukurun dibine bir araba sürme olasılığı, betonlanacak yapının seviyesinin üzerine bir beton karıştırıcı monte etmek mümkünse, tepsi boyunca beton karışımı beslenir. Tepsiler neme dayanıklı kontrplak veya 6 m uzunluğa kadar metal levhalardan yapılmıştır.Beton karışımını küvet veya bunkerlerde beslemek için diğer yükleme ve boşaltma işlemlerinde kullanılan mevcut kaldırma mekanizmaları kullanılmaktadır. Bunlar ağırlıklı olarak mobil ve kule vinçlerdir, bazen ataşman vinç kullanırlar. Kovalar 0,3 ... 1 m3 hacme sahiptir ve beton karışımını sağlama kolaylığı için, üzerine tamamen boşaltılması için bir vibratörün monte edildiği bir "cam" şeklinde yapılır.
Beton karışımını döşerken en yaygın olarak beton pompaları kullanılır. Vardiya başına 80 m3'e kadar beton döşeme hacmi ile KamAZ, MAZ, Mercedes araçlarına dayalı yerli veya ithal beton pompaları kullanılmaktadır. Kamyona monte beton pompaları, bir yükleme hunisi, bir pompa ve bir dağıtım bomu ile donatılmıştır. Beton karışımı dikey (80 m'ye kadar) ve yatay (360 m'ye kadar) yönlerde beslenir. Vardiya başına 60 m3'ten fazla beton ihtiyacı olan tesislerin yanı sıra artan kat sayısı (20 kattan fazla) olan binaların yapımında, beton finişer dağıtımı ile birlikte sabit beton pompaları kullanılmaktadır. 60 m'ye kadar erişim mesafesine sahip beton finişerler, monte edilmiş bina yapılarına veya yardımcı desteklere kurulur. Beton pompasının hunisi, içinden karışımın aktığı dikey bir boru hattı vasıtasıyla beton finişerine bağlanır. Beton finişerin bir park yerinden, birkaç kat üzerine beton serilir. Kütlesi 1...6 ton olan beton finişer tesiste kurulu bir montaj vinci ile bir sonraki otoparka taşınır, beton boru uzatılır ve beton karışımı binanın yeni kurulan katlarına beslenir. Beton karışımını sıkıştırmak için, iş teknolojisi gerektiriyorsa, çeşitli amaçlar için vibratörler kullanılır: dikey yapılar için - derin vibratörler, yatay yapılar için - titreşimli şaplar.
Beton karışımının yapıya çeşitli teknolojik makine setleri ile tedarik edilmesinin nispi maliyetinin karşılaştırılması, Şek. 21.1.
3. AÇILIP DEĞİŞTİRİLEBİLİR KALIPLARDA BİNA İNŞAATI
İki tip katlanabilir kalıp vardır: küçük panel ve büyük panel. Eskinin montajı manuel olarak yapılabilir, büyük panel kalıp vinç montajı gerektirir. Modern sistemler Kalıplar, binaların temelleri, kolonları, traversleri, duvarları, tavanları ve diğer yapısal elemanların betonlanması için geçerlidir.
3.1. DUVAR VE KOLON KALIPLARI
3.1.1. İNCE KALKAN KALIP
Çelik, kontrplaktan veya kombine edilmiş çeşitli küçük boyutlu kalkanların yanı sıra sabitleme elemanları ve destek cihazlarından oluşur. Kalkanlar 3 m2'den fazla olmayan bir alana sahiptir, bu tür bir kalıbın bir elemanının kütlesi 50 kg'ı geçmemelidir, bu da gerekirse kalıbın manuel olarak kurulmasına ve sökülmesine izin verir. Aynı zamanda beton karışımının kalıp üzerindeki yanal basıncı 0,6 kPa'ya kadar korunur. Mekanizmaları kullanmak ve işçilik maliyetlerini azaltmak için, kalıp panelleri, vinçler kullanılarak kurulacak ve kaldırılacak büyük boyutlu düz kalıp panellerine veya boşluk bloklarına önceden monte edilebilir.
Küçük panel kalıplar çok yönlüdür, çok çeşitli yapıların inşası için kullanılabilirler - temeller, kolonlar, duvarlar, kirişler, tavanlar. Kontrplak güvertenin dikkatli yüzey işlemi, 200 döngüye kadar çalıştırılmasını mümkün kılar. Kalıp panellerini çerçeveye takmanın kolaylığı, aşınmış bir güverteyi hızlı bir şekilde değiştirmenizi sağlar.
Kalıp sistemlerinin kurulum ve demontajının üretilebilirliği öncelikle tasarım ile belirlenir. bağlantı elemanları. Evsel kalıplarda, pimli ve cıvatalı bağlantılara sahip bir kaplin veya metal çubuk şeklinde kilitlemeler kullanılır. Böyle bir kilitleme çözümü, sökme sırasında ve özellikle sıkışma sırasında büyük çabalar ve önemli işçilik maliyetleri gerektirir. Ön montajda, genellikle eski cıvatalı bağlantılar kullanılırken, yabancı deneyim cıvatalı bağlantıların hariç tutulmasına dayanmaktadır.
Küçük panel kalıbın önemli bir dezavantajı, kalıbın montajı ve çıkarılması için yüksek işçilik maliyetleri, bu işlemlerin düşük düzeyde mekanizasyonudur.
"Doka" şirketinin küçük panel kalıbı "Framaks".Çerçeve küçük panel kalıp "Framaks", Moskova bölgesindeki şantiyelerde yaygın olarak kullanılmaktadır. Kalıp, duvarları, temelleri ve kolonları betonlamak için tasarlanmıştır (Şekil 22.1). Tek bir tasarım çözümü ile bir dizi modifikasyona sahiptir. 80 kN/m2'ye kadar yanal beton basınçları için sıcak daldırma galvanizli çelik çerçeve kullanılabilir. Kapalı kontur ve toz boya sayesinde yapının yüzeyi beton karışımından kolay ve hızlı bir şekilde temizlenir. 60 kN/m2'yi aşmayan bir basınçta ve elemanların manuel olarak montajında, benzer bir alüminyum çerçeve kalıbı "Alu-Framax" kullanılır. Bu iki seçeneğin döşemesi aynıdır, kenetleme ve sabitleme cihazları ve aksesuarları aynıdır.

Framax kalıp sisteminin bir özelliği, az sayıda kalıp elemanıdır. Üç yükseklik uygulanabilir: 135, 270 ve 330 cm genişlikte elemanların boyutları 135, 90, 60, 45 ve 30 cm veya 5 boyuttadır. Elemanların ve bağlantılarının tasarımı, çeşitli boyutlardaki yüzeylerin kalıplanmasını kolaylaştıran hem dikey hem de yatay olarak konumlandırılmalarına izin verir. Geniş kalıp alanları için ve panelleri büyük panel kalıpta birleştirirken, 2,7x2,4 m büyük boyutlu bir panel kullanılması tavsiye edilir (Tablo 22.1).
Tablo 22.1 Kullanılan çerçeve elemanları "Framax"
Boyutlar, m |
Ağırlık (kg |
Boyutlar, m |
Ağırlık (kg |
Boyutlar, m |
Ağırlık (kg |
evrensel elemanlar |
|||||
Güverte çeşitli versiyonlarda yapılabilir - 21 mm kalınlığında su geçirmez kontrplaktan, arkadaki çerçeveye vidalarla tutturulmuş alüminyum ve galvanizli çelik levhalardan, beton yapının temiz ve pürüzsüz bir yüzeyini sağlayan ve güverte değişimini kolaylaştıran .
Kalıp elemanının kontur çerçevesinin, çerçevenin dış profili boyunca uzanan özel bir oluğa sahip olması nedeniyle, kalıp elemanlarının birbirine bağlantısı, çerçevenin herhangi bir yerinde hızlı ve güvenilir bir şekilde gerçekleştirilebilir. İki elemanı birbirine bağlamak için, hızlı hareket eden ve evrensel uzatılmış (kalıp panelleri arasında bir ek varsa), elemanların bağlantısını basit bir çekiç darbesiyle sabitlemenizi sağlayan kilitler (kelepçeler) kullanılır. Doka, hızlı serbest bırakma kelepçeleri kullanır. Yatay genişlemeyi algılamak için vida bağları kullanılır, bu da hızlı kurulum ve sökme sağlar.
Kalıp, küçük ve büyük güverte yükseklikleri için çok çeşitli yapıların inşası için uyarlanmıştır.
Vida bağları kullanarak kalıp panellerinin birbirleriyle bağlantısını tek bir kalıp sisteminde başarıyla çözdü. Bunu yapmak için, kalıp çerçevesinde özel olarak bırakılan ankraj manşonlarına yerleştirilmiş vida dişli ankraj çubukları kullanın. Ankraj vidaları, yüzeye geniş bir yapışma alanına sahip özel ankraj plakaları ve plakalara eksensel olarak tek bir bütün halinde bağlanan ankraj somunları yardımıyla sabitlenir ve sabitlenir. Vida bağı, konik ankraj manşonundan geçen ankraj vidalarının çerçeve elemanlarını birbirine eğik olarak bile sabitlemesine izin verecek şekilde tasarlanmıştır. Ankraj plakasının tasarımı, kalıba sağlam bir şekilde oturmasını ve ankraj somunlarının güvenilir şekilde sabitlenmesini sağlar.
Yüksek mukavemetli çerçeve çerçeveleri ve rijit güverte yapısı, panelleri kararlı ve düşük deformasyonlu hale getirerek, karşıt kalıp panellerinin yalnızca iki bağlantı çubuğuyla birbirine bağlanmasına olanak tanır ve böylece oldukça esnek bir sistem sağlar.
"Doka" şirketinin küçük panel kalıbı "Frameco". Doka şu anda kullanım için geliştirilmiş çerçeve kalıp sistemi Frameco'yu önermektedir. Kutu şeklindeki kalıbın çelik sıcak daldırma galvanizli çerçevesi, yüksek mukavemet ve sertlik sağlar, kalıp levhasının uçlarını hasardan korur. Çerçevenin dış profili boyunca mevcut oluk, bitişik kalıp elemanlarını herhangi bir yerde dikey ve yatay konumda bağlamanıza izin verir. Bağlantı parçaları ve bileşenleri olarak Framax sisteminin ürünlerini kullanabilirsiniz. Sistemlerin çerçeve profilleri aynı, Frameco sisteminin kalıp döşemesi incelmiş, kalınlığı 18 mm.
Standart boyutlardaki elemanların ızgarası biraz değişti. 330 kg kütleli tek büyük boyutlu eleman 2.4 x 3.0 m kalır, 60 kN / m2 yük için tasarlanmış kalan elemanlar üç nominal genişliğe sahiptir - 1.0; 0,75 ve 0,5 m ve iki yükseklik - 3,0 ve 1,2 m (Tablo 22.2). Kolonların kalıpları için beton karışımının 90 kPa'ya kadar basıncına izin veren özel elemanlar geliştirilmiştir. Kalıp panelleri 0.9 m genişliğe ve üç yüksekliğe sahiptir - 3.0; 1,8 ve 1,2 m, kalıbı gerekli kolon yüksekliğine en uygun şekilde ayarlamanıza olanak tanır. Panellerdeki deliklerin elverişli konumu, 5 cm'lik artışlarla 75 x 75 cm'ye kadar kesitli kolon kalıplarının monte edilmesini mümkün kılar.
Tablo 22.2 UYGULANAN ÇERÇEVE ELEMANLARI "FRAMECO"
Boyutlar, m |
Ağırlık (kg |
Boyutlar, m |
Ağırlık (kg |
Boyutlar, m |
Ağırlık (kg |
|
Evrenselelementler |
||||||
Eksantrik ve uzun kilitler, sistemin tüm elemanlarını hızlı ve sağlam bir şekilde bağlamanıza olanak tanır. Her cihazın parçaları birbirine bağlıdır, kaybolmaz. Kirliliğe karşı dayanıklıdırlar. Kilitler, bitişik kalıp panellerini, kilitteki özel bir deliğe bir çekiçle sürülen özel bir pim ile bağlar. Aynı zamanda, kalıp panellerinin bağlı elemanları birlikte çekilir, kenetleme cihazı, kalkanların çerçevesindeki olukların varlığı nedeniyle eklemi gerilmeye karşı korur, düzleştirilir ve dışarıdan aynı hizadadır.
Uzatılmış kilit (evrensel sıkıştırma cihazı), bağlantısı kesildiğinde bileşenlerinin kaybolmaması için tasarlanmıştır; ayrıca bitişik kalıp panellerini bir çekiçle özel bir yuvaya sürülen bir pim ile birbirine bağlar. Eksantrik kilidin aksine, uzatılmış kilit, kalıp panelleri arasına bir kiriş veya başka bir eleman takmanıza izin verir, eklemin toplam genişliği 15 cm'ye kadar ulaşabilir.
Meva kalıp sistemleri. Alman şirketi "Meva", çözümde ortak olan ancak bazı tasarım özelliklerinde farklılık gösteren çeşitli kalıp türleri üretmektedir. Meva kalıp sistemi, inşaat halindeki hem en küçük hem de en büyük yapılar için herhangi bir yatay ve dikey bina yapısının kalıplanması için tasarlanmıştır (Şekil 22.2). Bu sistem, kendisine hak ettiği takdiri veren birkaç farklı ve özgün tasarım öğesiyle ayırt edilir. Panjur kilidi, yapısal çerçevenin herhangi bir noktasında yatay ve dikey yapılarda iki kepenk panelinin hızlı ve güvenli bir şekilde bağlanmasını sağlar. Çerçevelerin ve stifnerlerin kapalı profilleri, burulma yüklerine başarılı bir şekilde dayanan, birleştirme elemanlarının işlemlerini kolaylaştıran ve inşaat güvenliğini artıran kalıp bağlantıları oluşturur. Karşılıklı kalıp panellerinin birbirine işlevsel olarak sabitlenmesinin unsurları arasında, işçilik maliyetlerini önemli ölçüde azaltan ve tüm bağlantıları kolaylaştıran özel dişli vida bağları bulunur.
Meva kalıp levhalarının özellikleri: tüm levha çerçeveleri çelik, alüminyum veya karışık çerçeveden yapılmıştır, kavisli oluklu ve güverte elemanlarının kenarlarının güvenilir şekilde korunduğu tek parça içi boş profilden yapılmıştır. Kalıp panellerinin patentli kilitleri tüm Meva sistemlerine uygun ve güçlüdür, bu da çerçevenin herhangi bir yerinde kullanılmasına izin verir. Bir kilit uygularken, iki kalkan birlikte çekilir (altları düzleşir) ve profillerin alt kısımları ve elemanlar özel bir eğim yerlerinde bir araya getirilerek bir çekiç darbesiyle kapatılır. Kilit 2,8 kg ağırlığındadır ve tek elle takıp sabitlenebilir. Kilitteki kama, kilidin eksiksizliğini sürekli olarak sağlayan çıkarılabilir değildir. Bu yapıcı kalıp çözümünün avantajı, yalnızca panellerin değil, aynı zamanda tüm kalıp panelinin sertliğidir. Kalıp tasarımı, panellerin sadece dikey olarak değil, aynı zamanda yatay olarak da kurulmasını mümkün kılar, bu da aralıklarını azaltırken, panellerin bağlantısının sertliği ve gücü azalmaz.

Kalkan kalıbı "Yıldız teknoloji" şirketi "Meva"(alüminyum kanatlı çelik çerçeve). Kalıp tipi "Yıldız teknolojisi" evrensel bir sistemdir; şekillendirilmiş oluklu tek parça içi boş profillerden yapılmış çelik çerçevelere dayanmaktadır. Profilin genişliği 4 cm, yüksekliği 12 cm, profilin kalınlığı statik çalışma şartlarına göre belirlenir ve 3,6 mm'ye kadar kabul edilir. Çerçevenin yüzeyi lakedir. Ağırlığı azaltmak için, iç sertleştiriciler - payandalar ve payandalar alüminyumdan yapılmıştır ve çelik çerçeveye yapışkanla tutturulmuştur. Çerçevenin bu çözümü, 40 m2'ye kadar bir panel alanına sahip vinç montajı için yapının sağlamlığını sağlar ve bireysel elemanların manuel olarak kurulmasına izin verir. Kalıp 70 kN/m2 statik yük için tasarlanmıştır. Optimal uygulama - temeller ve duvarlar için. 270, 135 ve 90 cm yüksekliğinde elemanlar üretirler, elemanların genişliği 9 boyuttadır - 270, 135, 90, 75, 55, 50, 45, 30, 25 cm 270 boyutları için elemanların özgül ağırlığı ve 135 cm, 1 m2 başına 55 kg'dır, diğer elementler için kütle 40 kg'ı geçmez.
Bir güverte olarak yüksek kaliteli çok katmanlı kontrplak benimsenmiştir; 90 cm genişliğe kadar olan elemanlar için kontrplak kalınlığı 15 mm'dir; 135 ve 270 cm genişliğindeki elemanlar için kontrplak kalınlığı 18 mm'ye çıkarılmıştır. Kontrplak her iki tarafta sentetik reçine ile kaplanmıştır. Levhalar çerçeveye dışarıdan keskin uçlu vidalarla tutturulur, tüm delikler plastik manşonlarla kapatılır, levhalar çerçeveye silikon ile sabitlenir.
Bileşenler ve kilitler Doka bağlantılarına benzer. Kilit (kelepçe) tek elle takılır (aynı anda merdivenlerde de olabilirsiniz), pim kelepçesine hafif bir çekiç darbesi ile bitişik kalkanları birlikte çeker, kalkanlar yer değiştirmeden hizalanır, sert düğüm oluşur. Kalıp panellerini bağlamak ve çözmek için, montajı için kalıp çerçevelerinde açık delikler bulunan vida bağları da kullanılır.
Startek kalıplarının lisanslı üretimi Rusya'da gerçekleştirilmektedir.
"Meva" şirketinin küçük panel kalıbı "Alu-star"(alüminyum panjur tahtası çerçevesi). "Meva" şirketinin "Alu-star" kalıbı, alüminyum tek parça iki odacıklı profillerden yapılmış çerçevelere sahiptir. Profilin genişliği 4 cm, yüksekliği 12 cm olarak alınır, çeşitli alanlardaki elemanlar için profilin kalınlığı statik işin özelliklerine bağlıdır. Çerçeve ayrıca, içinde olmayan enine bir nervür ile güçlendirilmiştir. metal çerçeve Startech sistemleri. Profilin yüzeyi, darbe direncini ve çizilme direncini artıran plastik bir kaplama ile korunmaktadır. Tasarım yükü - 60 kN/m2.
Öğe yelpazesi iki yükseklik içerir - 270 ve 135 cm, her iki yükseklik için genişlik olarak yalnızca 7 boyut kabul edilir - 90, 75, 55, 50, 45, 30 ve 25 cm 48 kg'lık maksimum ağırlık 270 x 90 cm'dir. , geri kalan elemanlar için kütle 1 m2 başına 30 kg'dır.
Güverte için, her iki tarafta sentetik reçine ile kaplanmış 15 cm kalınlığında yüksek kaliteli çok katmanlı kontrplak kullanılır - betonu iten plastik bir toz kaplama, kalıbı temizleme maliyetini önemli ölçüde azaltır. Kontrplak çerçeveye keskin uçlu vidalarla sabitlenir, delikler konik plastik manşonlarla kapatılır, kalkanların çerçeveye bitişik yerleri silikonla korunur.
Doka firmasının bileşenlerine benzer bileşenler kullanıldı. İki blendajı birbirine bağlamak için iki kilit bağlantısı yeterlidir. Tüm yardımcı elemanların sabitlenmesi ve kalıbın yayılması için vida bağları kullanılır. Montajı yapılan kalıp panelinin son seviyelendirilmesi için 50 cm uzunluğundaki traversler de kullanılır.
Kalıp önemli avantajlara sahiptir. İki odacıklı ve tek parça profil kullanımı sayesinde çerçeve sert ve dayanıklı hale geldi. Çerçevede alüminyum çerçeve kullanımı ürünlerin ağırlığını azaltmıştır, tüm paneller manuel olarak kurulabilir, yani kalıp vinci kurulumu yoktur. Hafif kilitleme bağlantıları kullanılmaktadır. Plastik güverte kaplaması yapışkan, darbe ve çizilmeye karşı dayanıklıdır. Bir çekiçle hafif bir darbe ile, kalkanların yüzeyinde mekanik hasar oluşmaz. Bütün bunlar, yeniden kullanım için temizlik zamanlarında önemli bir azalmaya yol açar.
Küçük panel çerçeve kalıbı "EcoAz", şerit ve cam tipi temellerin kalıpları için tasarlanmıştır ve manuel montaj sağlar. Kalkanlar 2400, 1600, 1200 ve 800 mm yüksekliğe sahiptir; 250 ila 800 mm genişlik, panelin maksimum ağırlığı 60 kg, kalıp üzerindeki yük 50 kN/m2'dir.
"Thyssen" şirketinin küçük panel kalıbı "Rasto". Alman şirketi Thyssen, kalıp sistemlerini yaygın olarak uyguluyor. Özellikle Rasto küçük panel kalıp, Manto büyük panel kalıp ve Sompakt levha kalıp olmak üzere birbirini tamamlayan kalıp takımları geliştirmiştir.
Kalıp "Rasto", panellerin manuel montajı için tasarlanmıştır. Kullanımı kolaydır, dayanıklıdır, 60 kN/m2'ye kadar beton karışımının basıncına dayanır, çok yönlüdür ve çeşitli inşaat alanlarında kullanılabilir.
Ana eleman 270 cm yüksekliğinde bir kalkandır, yüksek yapılar için 150 cm yüksekliğinde, 45 ila 90 cm genişliğinde ve 5 cm dereceli ek kalkanlar uygulanabilir.Kalkanların dikey ve yatay olarak birleştirilmesi kolaydır , 5 cm'lik bir modül ile uzunluk boyunca ayar yapılır, hem yatay dikişler çakıştığında hem de yer değiştirdiğinde ekran uzantısı mümkündür.
Rasto sisteminin kalıp panelleri sıcak daldırma galvanizli çelikten imal edilmiş olup, kalıp elemanları yüksek dayanım ve mukavemete sahiptir. Kalıp çerçevesi, 12 cm yüksekliğinde bir metal profilden yapılmıştır, çevresi boyunca aynı kalınlıktaki güvertenin uçlarını her taraftan koruyan 14 mm yüksekliğinde bir çıkıntıya sahiptir. Çerçeve, kalkanların genişliğine bağlı olarak her 30 cm'de bir uzunlamasına nervürlerle donatılmıştır, 1 ... 2 enine nervürü vardır. Köşe bağlantılarının belirli yerlerde bulunması, panellerin yüksek sağlamlığını ve stabilitesini sağlar ve çerçeve için içi boş profillerin kullanılması ağırlıklarını önemli ölçüde azaltır. 2,7 x 0,75 m kalkan sadece 60 kg ağırlığındadır ve elle hareket ettirilebilir ve monte edilebilir.
Kalkanları bağlamak için evrensel kilitler (rasto sıkma) kullanılır. 40 cm uzunluğunda bir eksantrik kilit (kombi-sıkma) iki bitişik elemanı kuzu dipten uca bir çalışma dönüşünde birleştirir, beton karışımının gerilimi, olası titreşimi ve basıncını dengeler. Sıkıştırma, yalnızca kalkanların hizalanmasını ve eşeksenliliğini sağlamakla kalmaz, eklemin sertliği, toplam alanı 40 m2'ye kadar olan kalkanların vinçle kaldırılmasına izin verir. “Ayakta” ve “yalan” levhaların bağlanması veya levhalar arasına 15 cm genişliğe kadar bir ek yerleştirmek gerektiğinde, 55 cm uzunluğunda uzun kilitler (sürgülü kombi kıskaçlar) kullanılır. 6 cm'ye kadar da geliştirilmiştir. Rasto", kayışın bir hareketinin kenetleme pedlerini bağlamasına izin vererek, bitişik kalkanların sıkı bir şekilde bağlanmasını sağlar. Bu eksantrik kamalı kilitlerin sökülmesi basittir ve ekstra çaba gerektirmez. Kilit bağlantıları, kurulum sırasında, iki bitişik panel başına iki kilit olacak şekilde yerleştirilir ve genel kalıp sisteminin stabilitesinden ödün vermeden kolay sökmeye izin verir.
Rasto küçük panel kalıp ürünlerinin tamamı kullanılmazsa, kalıpta duvar boyunca ve köşe parçalarında kurulum için beş santimetre kompansatörler (uçlar) kullanılır. Kalıp kiti, 15 x 15 cm ile 55 x 55 cm arasında değişen dikdörtgen ve kare şekillere sahip olmanızı sağlayan özel kolon kalıp panelleri içerebilir.
Kalıp panellerinin birbirine bağlanması, kolonların, duvarların ve bölmelerin kalıplarının çözülmesi için vida bağları sağlanmıştır. Kalıp panellerini hizalamak, kurulum ve betonlama sırasında kalıp bloğu olan panel sisteminin mekansal sertliğini sağlamak için farklı uzunluklarda ara parçalar (manşonlar) vardır.
Dally'den küçük panel kalıp. Dally kalıp, kalıp panelini dikey ve yatay panellerle tamamlamayı mümkün kılan modüler elemanlardan oluşur. Kalıbın ana avantajı, minimum sayıda eleman ve orijinal bağlantı elemanından, çok çeşitli yatay ve dikey yapıların kalıbını manuel olarak monte etmenin mümkün olmasıdır. Levhalar 264, 132 ve 88 cm olmak üzere üç boyda ve 10 boyda 75 ila 20 cm arasında 5 cm gradasyonlu olarak üretilmektedir.264 x 75 cm ölçülerindeki standart levhaların kütlesi 60 kg, manuel montaj kalıp elemanlarına izin verilir. Her kalkanın uçlarında, iki bitişik kalkanın güçlü bir pim bağlantısı için iki kaynaklı altıgen somun sağlanmıştır (Şekil 22.3).
Kalıbın çalışma yüzeyi, her bir kalıp elemanının düzenli temizlik ve yağlama ile en az 350 kez kullanılmasına izin veren, çift taraflı güçlendirilmiş kaplamaya sahip 21 mm kalınlığında 5 katmanlı bir ahşap levhadır. Kalkanların çerçeve elemanları, çerçeveyi oldukça sert yapan kaplamalar ve eşarplar ile çelik sacdan yapılmıştır, ancak bu çözüm kalkanın ağırlığını önemli ölçüde azaltabilir. Her kalkan sadece iki bağlantı çubuğuyla bağlanır,
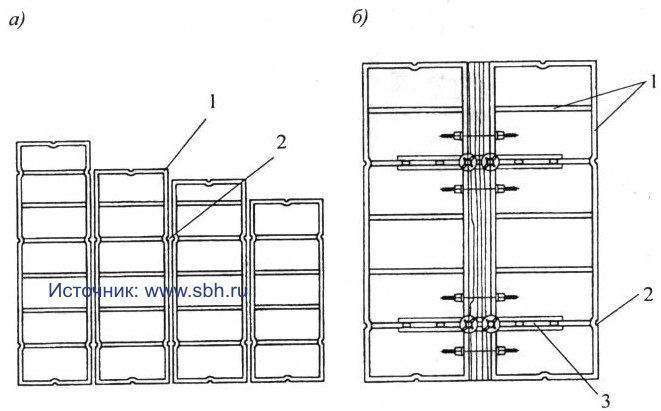
son sabitleme - elle kelebek somun ile. Şirket, iki bitişik kalkanın açık deliğine yerleştirilen ve bir çekiç darbesiyle sıkıca sıkıştırılan kendi cıvatalı (kilitsiz) kelepçelerini geliştirmiştir. İki bitişik kalkan dikey olarak yer değiştirirse, bir çekiç darbesiyle herhangi bir yere sabitlenen özel bir braket kullanılabilir. Bu sabitleme, yardımıyla kalıp profillerinin birbirine bastırıldığı iki kam sayesinde gerçekleşir. Çekiç ters yönde vurularak kepenk braketi çıkarılır.
Köşe birleşimlerinin oluşturulması için, panellerin herhangi bir açıda kenetlenmesini sağlayan dış ve iç köşe elemanları sağlanmıştır. Kalıp oluşturmanın mümkün olduğu özel ayarlanabilir teneke düzleştiriciler geliştirilmiştir.

tam olarak gerekli boyutlarda panel. Panellerin ve köşe bağlantılarının özgünlüğü, farklı kalınlıklarda, yüksekliklerde ve yapının çeşitli ana hatlarını plandaki duvarlar için standart elemanlardan Dally kalıbının kullanılmasına izin verir.
Karşılıklı kalıp panellerinin bağlantısı ve karşılıklı sabitlenmesi kelebek somunlu özel vidalı kaplinler kullanılarak gerçekleştirilebilir; bağlantı vidası, kalıbın uç yüzeylerinde bulunan bitişik iki panelin özel yarım deliklerinden geçirilir.
Dalli kolon kalıbı 4 eleman yüksekliği için tasarlanmıştır - 300, 264, 132 ve 100 cm (Şekil 22.4), tasarım, panellerin yüksekliğinde, kolon boyutları 10 x 10'dan 80 x 80 cm'ye 2,5'lik artışlarla oluşturmaya izin verir. santimetre
Makale şirket tarafından dijital olarak hazırlanmış ve gönderilmiştir.
SBH COTPAHC (www.website) tarafından yazının içeriğine "RINGER" ile ilgili paragraf eklenmiştir:
"RINGER" (Avusturya) tarafından üretilen sığ kalıp: RINGER kalıp, tasarımda ortak olan ve birbiriyle tam uyumlu birkaç tip içerir. Bazı tasarım özelliklerinde farklılık gösterirler. Kalıp, inşaat halindeki yapıların herhangi bir yatay ve dikey yapısının oluşturulması için tasarlanmıştır (Şekil 5.1). Kalıp tasarımı, panellerin uzun süreli çalışmasını ve montaj kolaylığını sağlayan birkaç karakteristik özgün çözüme sahiptir.
Şirket üç tip kalıp sistemi üretmektedir:
1) Alu-Master- 60 kN/m2'ye kadar yükler için alüminyum kalıp,
2)
Çelik Ustası- 80 kN/m2'ye kadar yükler için çelik kalıp,
3)
Alu-2000- 60 kN/m2'ye kadar yükler için basitleştirilmiş profile sahip alüminyum bütçe kalıp modeli.
Kalıp kilidi, levhaların ana bağlantı elemanıdır ve kendinden kilitli bir tasarıma sahip olduğu için tek elle monte edilebilir. Kilidin kuvvet kilitlemesi diğer el ile kama üzerine çekiç darbesi ile yapılır. Kilidin kaması çıkarılamaz, bu da kaybını hariç tutar. 270 cm yüksekliğindeki panoların dikey bağlantısı için sadece 2 kilit yeterlidir.Kilit bağlantıları elektrikli olup, kasanın herhangi bir yerinde kilit kullanımına izin verir. Kilidi takarken, kalkanlar birlikte çekilir ve hizalanır. Kilitlerin tasarımı, birkaç panodan oluşan tüm kalıp panelinin sağlamlığını sağlar. Kalkanlar hem dikey hem de yatay olarak monte edilebilir.
"RINGER" firmasının kalkan kalıbı STEEL-MASTER ve ALU-MASTER. MASTER kalıp çerçevesi (Şekil 5.2), sabit bir şekle sahip bükülmeyen sert kenar profillerinden oluşur. Çerçevenin içinde rijitliği artıran, mukavemet sağlayan ve deformasyonu önleyen eğik bir nervür bulunur. Bağlantı elemanlarını kenar profiline takmak için eğik bir nervür ile güçlendirilmiş bir sıkıştırma yeri sağlanır. Kalıp güvertesinin üst üste geldiği yerlerde, çerçeve, kalkanın kenarlarını hasardan koruyan özel bir çıkıntıya sahiptir. İki destek platformu, kalkanların temizlenmesini büyük ölçüde kolaylaştırır. Çerçeveyi güçlendirmek için, kenar (kalkanın çevresi boyunca) ve fonksiyonel (kalkan boyunca) profiller, güverte için bir destek oluşturarak ona kaynaklanır. Bir güverte olarak, hem Fin kontrplağını hem de plastik PRIMUS'u kullanabilirsiniz - her güverte çerçeveye vidalarla vidalanır. Fonksiyonel profiller, diğer yapı elemanları - gergi kelepçeleri, destekler vb. bunlara kolayca takılacak şekilde yapılmıştır.Çerçeve profilinin genişliği 123 mm, yüzeyi kolay temizlik için toz boyalıdır.
Kalıp STEEL-MASTER, 330, 270 ve 135 cm olmak üzere üç uzunlukta ve on genişlikte çelik çerçeveli panellerden oluşur (Tablo 5.1).
Tablo 5.1 Çelik kalıp panelleri "RINGER STEEL-MASTER"
Boyutlar, m |
Ağırlık (kg |
Boyutlar, m |
Ağırlık (kg |
Boyutlar, m |
Ağırlık (kg |
evrensel elemanlar |
|||||
ALU-MASTER kalıp, 270 ve 90 cm olmak üzere iki uzunlukta ve sekiz genişlikte alüminyum panellerden oluşmaktadır (Tablo 5.2). Genişliğin boyutları, herhangi bir konfigürasyonun bir yüzeyini oluşturmak için kullanılabilecek şekilde seçilir. Alüminyum kalıp, çelik kalıba göre önemli bir avantaja sahiptir - panellerin düşük ağırlığı manuel montaja olanak tanır.
Tablo 5.2 Alüminyum kalıp panelleri "RINGER ALU-MASTER"
Boyutlar, m |
Ağırlık (kg |
Boyutlar, m |
Ağırlık (kg |
evrensel elemanlar |
|||
Kalıp çerçevesinde 4 adet kaynaklı geçişli burç bulunmaktadır. Ankraj pimlerinin diş açılmasını kolaylaştırmak için burçlar koni şeklindedir. Ankraj pimlerinin kullanılması, kalıp elemanlarının bozulmasını ve bunların yükseklikteki yer değiştirmesini ortadan kaldırmayı mümkün kılar.
Üniversal elemanlar sütunlar (Şekil 5.6) veya köşeler (Şekil 5.5) oluşturmak için kullanılır. Evrensel kalkan ile aynı boyutlardaki normal kalkan arasındaki fark, evrensel kalkanın çerçevesinde delikler olmasıdır. 5 cm'lik delikler arasındaki mesafe, duvar kalınlığı veya kolon kesitinin değerini ALU-MASTER için 20 ila 65 cm veya STEEL-MASTER için 20 ila 85 cm arasında değiştirmeyi mümkün kılar.

Üniversal panoları bağlamak için sadece üniversal bir bağlantı vidası ve bir kombinasyon kelebek somun gereklidir.
MASTER iç ve dış köşeler kullanılarak 90 derecelik açılar oluşturulur (Şekil 5.7). Köşeler, kalıp panellerinin boyuna karşılık gelen uzunlukta üretilir.
60 ila 180 derece arasında keskin ve geniş açılar elde etmek için MASTER iç ve dış menteşeli köşeler kullanılır (Şekil 5.8). Menteşeli köşelerin yüksekliği 330, 270, 135, 90 cm, iç köşe kenarlarının uzunluğu 30 cm, dış köşesi 6.5 cm'dir.

135 derecelik köşelerin yapılması, önceden yapılmış 135 derecelik köşelerin mevcudiyeti ile büyük ölçüde kolaylaştırılmıştır. Sabit köşeler, mafsallı köşelere göre daha sağlam ve stabildir ve ek tesviye rayları gerektirmez. 135 derecelik köşeler, 25 cm et kalınlığında iç ve dış köşeler herhangi bir ek eleman kullanılmadan birleştirilecek şekilde yapılmıştır.
MASTER ark kalkanları ile poligonal bir şekilde (poligon şeklinde) yuvarlak duvarlar oluşturabilirsiniz.Ark kalkanları kalkanlarla birleştirilir. İstenilen yarıçapı elde etmek için bir ara cıvata kullanılır. Minimum iç yarıçap 1,8 m'dir Ark ekranları, ekranlara kelepçelerle bağlanır (Şekil 5.3).
Düzeltme kalkanları yardımıyla 4 ila 20 cm arasındaki boşluklar doldurulabilir, duvarın kalınlığını eşitlemek için bir tahta kullanılır (Şekil 5.3).
20 cm genişliğe kadar olan ayar derzleri Master kelepçe kullanılarak yapılır. 270 cm panel yüksekliğinde, boşlukları doldurmak veya bitmiş bir duvara eklemek için sadece 2 kelepçe gereklidir.
20 cm genişliğe kadar olan ayar derzleri bir kelepçe kullanılarak yapılır. Kelepçenin dudakları arasındaki mesafe bir vida pimi ile ayarlanır.
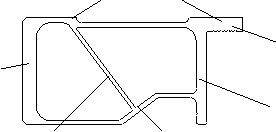

Önemli yükseklikteki yapıları güçlendirmek için, MASTER 150 doğrultma rayları kullanılır MASTER 100 doğrultma rayları, levhalar veya levhalar ile bitmiş duvar arasındaki derzleri düzleştirmek için tasarlanmıştır. Doğrultma rayı, MASTER-RS gerdirme kelepçesi kullanılarak fonksiyonel profile sabitlenir (Şekil 5.3). Doğrultma rayı ankrajlara da takılabilir.
Panellerin eğimli montajı, kalıp çerçevesindeki özel bir eğimli manşon yardımıyla mümkündür. Kalkanlar bir gergi cıvatası ve bir kombi pul ile bağlanmıştır. Cıvata delikleri konik olduğundan, kalkanlar eğilebilir. Kombi yıkayıcının haznesi, çerçeveye tam oturmasını sağlayan bir menteşe ile donatılmıştır.
"RINGER" firmasına ait kalkan kalıp ALU-2000. Bu kalıp sistemi, ALU-MASTER sisteminin bütçe versiyonudur ve daha basit bir çerçeve tasarımıyla (iç eğik nervürsüz) ayırt edilir. Çerçeve kalınlığı 10 cm'ye düşürülmüştür Buna rağmen kalıp 60 KN/m2 aynı yük ile çalışmanıza olanak sağlar ve aynı zamanda %15 daha düşük maliyetlidir. Çerçeve tasarımının basitleştirilmesi, kalıp çevrimlerinin sayısını %5-10 oranında azaltır.
Tablo 5.3 Alüminyum kalıp panelleri "RINGER ALU-2000"
Boyutlar, m |
Ağırlık (kg |
Boyutlar, m |
Ağırlık (kg |
evrensel elemanlar |
|||
Makale şirket tarafından dijital olarak hazırlanmış ve gönderilmiştir.
3.1.2. GENİŞ KALKAN KALIP
Kalıp, 3...20 m2'lik artan taşıma kapasitesine sahip levhaları içerir ve büyük kalıp yüzeylerine sahip yapılar için kullanılır. Kalıp elemanları, güverteyi destekleyici aşıklar ve nervürlerle birleştirir. Kalıp levhalarının boyutlarının arttırılması, yapıların kalıpları üzerindeki işin emek yoğunluğunu büyük ölçüde azaltmayı ve süreçlerin karmaşık mekanizasyonunu daha tam olarak gerçekleştirmeyi mümkün kılar. Geniş panel kalıp, kullanımda en çok yönlü ve hareketlidir ve ara yüzlerin sayısını azaltarak yapıların kalitesini önemli ölçüde iyileştirebilirken, kalkanın yüksekliği betonlama katmanının yüksekliğine eşit olarak alınır.
Kalıp, çok çeşitli yapıların büyük boyutlu monolitik yapılarının inşası için tasarlanmıştır, kalıbın montajı ve sökülmesi sadece vinçler tarafından gerçekleştirilir. Kalıp panelleri kendinden desteklidir ve bir güverte, kalkan takviyeleri ve yük taşıyıcı yapılar içerir. Bu tür kalkanlar, iskeleler, kurulum ve ilk hizalama için payandalar ve ayar krikoları ile donatılmıştır.
Büyük panel kalıp, binaların ve yapıların hemen hemen tüm yapısal elemanları için geçerlidir: temeller, dış ve iç duvarlar, sütunlar, zeminler. Kalıp, konut ve sivil binaların yapımında en büyük dağılımı bulmuştur.
Çok katlı konut yapımında, büyük panel kalıp kullanıldığında, dış duvarların prefabrike prefabrik panellerden (etkili yalıtıma sahip üç katmanlı), genişletilmiş kil beton veya tuğladan yapılması tercih edilir. İç taşıyıcı duvarlar monolitik betonarmedir. Ortak bir tasarım şeması, betonarme kolonların kirişli veya kirişsiz tavanlı taşıyıcılar olduğu bir tasarım şemasıdır. Prefabrik ve tuğla dış duvarlar için, beton iş üretiminden bir katın montajının gerisinde kalınması tavsiye edilir.
Betonlanacak yapının kalınlığına ve yüzeylerin kalitesine ilişkin gereksinimlere bağlı olarak, kalıp kalkanı bir destekleyici çerçeveden yapılır ve tüm kalıp düzlemi için bir güverte veya bir kalıp paneli, birbirine bağlı ayrı envanter panellerinden monte edilir. kilit sistemi. Karşılıklı iki kalıp paneli, gelecekteki beton yapının gövdesinden geçirilen ve betonlamadan önce kurulan bir yatay vida bağları sistemi ile birbirine bağlanır. Kalıbın stabilitesini sağlamak ve tasarım pozisyonuna hizalamak için, çeşitli sistemler mekanik vidalı krikolar ve ayar cihazları ile donatılmış payandalar ve destekler (Şekil 22.5).
Duvar kalıbı iki aşamada kurulur. İlk önce, takviye kafesi monte edilir, daha sonra - duvarın bir tarafındaki kalıp, zeminin tüm yüksekliğine ve işin son aşamasında - ikinci taraftaki kalıp. Kalıp kabul edilirken geometrik boyutlar, eksenlerin çakışması, kalıp panellerinin dikeyliği ve yataylığı, gömülü parçalar, derzlerin ve dikişlerin yoğunluğu kontrol edilir.
Beton karışımı, kalkanın dış tarafında bulunan, üzerine sabitlenmiş konsol iskelelerden kalıba yukarıdan yerleştirilir. Duvarların betonlanması bölümler halinde yapılır, sınırlar genellikle kapılardır. Beton karışımlı hazne, her zaman birkaç noktadan boşaltılırken, karışım, döşemenin hemen ardından derin vibratörlerle sıkıştırılarak 30 ... 40 cm kalınlığında tabakalar halinde kalıba yerleştirilir. Kalıbın montajı sırasında beton karışımının basıncını algılamak için özel envanter burçları ve bazen ek astarlar kullanılır. Duvarlar ve tavanlar için kalıp panelleri genellikle betonlanacak alanın (binanın hücreleri) boyutuna göre yapılır; bu alan 70 m2'yi geçmemelidir.
Kalıp, tasarımı ile belirlenen bir sırayla kurulur ve çalışma sürecinde bireysel elemanların ve kalıbın bir bütün olarak stabilitesini sağlar.
"Meva" şirketinin büyük panel kalıp "Mammut"(büyük yapılar için). Mammut kalıp her türlü inşaat için geçerlidir, ancak en yaygın olarak konut inşaatında kullanılır.
100 kN/m2'ye kadar beton karışımının tasarım basıncı için "Mammut" betonarme kalıp sistemi geliştirilmiştir. Kalıp çerçeveleri, şekillendirilmiş oluklu yüksek mukavemetli tek parça çelik içi boş profillerden yapılmıştır. Profilin yüksekliği, küçük panel kalıpta olduğu gibi aynı kaldı - 12 cm, ancak genişlik 6 cm'ye yükseldi; Bireysel kalkanlar için profilin kalınlığı, statik çalışma koşullarına göre 3,8 mm'ye ulaşır. Çerçevenin yüzeyi lakedir.
Yükseklik açısından 3 boyut kabul edilir - 300, 250 ve 125 cm, her yükseklik için elemanların genişliğinin 4 değeri kabul edilir - 250, 125, 100 ve 75 cm, ancak gerekirse elemanlar 5 cm'lik artışlarla 60 ila 25 cm genişlikte aynı yükseklikte temin edilebilir.Kabul edilen standart ölçüler hemen hemen her boyutta bir kalıp paneli elde etmeyi mümkün kılar. Kalıbın sadece vinç montajı sağlanır, panellerin ağırlığı 1 m2'de 62 kg'dır. Kalıbın yapısal çözümü, 97 kN/m2'ye kadar beton karışım basıncında bile sistemin belirtilen rijitliğini sağlamayı mümkün kılar. Bu kalıp için, beton karışımının pnömatik sıkıştırılması için dış vibratörlerin kullanılması kabul edilebilir.

Beton karışımının tasarım basıncına bağlı olarak, her iki tarafta sentetik reçine - plastik bir kaplama ile işlenmiş 21 mm kalınlığında çok katmanlı yüksek kaliteli bir kontrplak kullanılır. Kesici kenarlı vidalarla döşemenin yanından çerçeveye sabitleme, delikler plastik manşonlarla kapatılır, kalkanların çerçeve ile bağlantısı silikonla korunur.
Bileşenler olarak, diğer sistemlere benzer şekilde, kilitler kullanılır - eleman başına iki, tüm yardımcı parçaları elemanlara sabitlemek ve kalıbı yaymak için evrensel kilitler (gerekirse bağlantı vidaları). Set, yüzeyin enine hizalanması ve tesviyesi için çapraz çubuklar içerir.
Kilit bağlantıları çerçevenin herhangi bir yerine kurulabilir. Bunlar aynı yapıcı çözümün özel kilitleridir, basit, güvenilir ve kullanımı kolaydır. Vida bağları - standart. Sıcak daldırma galvaniz sayesinde tüm bileşenler yeterince dayanıklıdır.
Kalıbın avantajı, cihazın ilave sabitleme ve destekler olmadan 4,5 m'ye kadar izin verilen yüksekliğidir, kalıp yüksek hızlı betonlamaya dayanabilir.
MevaDek döşeme kalıbı dört farklı çözüm sunar: kalıp kaplamalı ana ve yardımcı kiriş sistemi; hazır panellerin veya basitçe lamine kontrplakların kalıp kaplaması ile ahşap kirişler sistemi şeklinde üst üste binen enine kirişler; panel sistemi; sıyırma işlemini kolaylaştırmak için düşük başlı aksesuarların kullanılması.
"Thyssen" şirketinin geniş panel kalıbı "Manto". Büyük panel kalıp "Manto", büyük konut ve sanayi tesislerinin inşası için tasarlanmıştır. Konutlar için 2,7 m yüksekliğe ve endüstriyel ve sivil inşaat için 3,3 m yüksekliğe sahip geniş bir kalkan yelpazesi geliştirilmiştir. Kalıp, 80 kN / m2'ye kadar beton karışımının basıncına dayanacak şekilde tasarlanmıştır (Şekil 22.6).
Çerçeve çerçevesi, bükülmeye karşı yüksek direnç sağlayan karmaşık şekilli 14 cm yüksekliğinde galvanizli metal profilden oluşur. Sıcak daldırma galvanizleme, kalkanları kolaylaştırır, korozyonu ortadan kaldırır ve çerçevenin yapışmasını keskin bir şekilde azaltır. Çerçevenin diğer stabilite elemanları ile birlikte kabul edilen boyutları, kalkanlara özel bir mukavemet kazandırır, beton karışımının 3,3 m yüksekliğe kadar hidrostatik basıncına dayanmalarına izin verir. 5,4 m yüksekliğe kadar kalkanlar, destek olmadan yapabilir.

Sıradan kalıp panelleri 330, 270, 120 ve 60 cm yüksekliğinde ve 45 ila 330 cm genişliğinde üretilmektedir.Herhangi bir pozisyonda tüm paneller yatay ve dikey olarak, yükseklik veya yatay ofset ile birleştirilir. Kalıp panelleri, çerçevelerinin içindeki iki fonksiyonel oluk, farklı şirketler tarafından geliştirilen çeşitli bağlantı araçlarının optimum kullanımını garanti ettiğinden, evrensel olarak kabul edilebilir. Tüm levhalar, değerli ahşaptan yapılmış plastik kaplı çok katmanlı levhayı darbelere ve hasara karşı koruyan, kontur boyunca çelik bir çerçeve profiline sahiptir.
Kalkanları birbirine bağlamak için, gerilmeye ve titreşime iyi dayanıklı iki elemanın basit, hızlı ve güvenilir bir şekilde bağlanmasını sağlayan özel doğrultma kelepçeleri kullanılır. Bağlantının rijitliği ve sağlamlığı, vinç montajı sırasında 40 m2'ye kadar alana sahip kalıp panellerinin ek sabitleme olmadan kaldırılmasını mümkün kılar. Bağlantıya ek olarak, kilitler aynı anda kalkanları düzeltir ve hizalar. Kalkanlar inşa edildiğinde, yükseklikleri kaydırıldığında kullanılabilirler. İki kalıp panelini birleştirmek için maksimum boyutlar iki kilit yeterlidir.
Betonlama bandı için ve sütunlu temeller ve sütunlar minimum sayıda elemanla yönetilebilir. Temelleri oluşturmak için tahtalar "yatarak" yerleştirilir. Kolonları betonlamak için özel olarak tasarlanmış bir kalıp kullanabilirsiniz, ancak geleneksel kalkanların ve köşe kilitlerinin kullanılmasına izin verilir. Vidalı şaplarda betonun basıncına bağlı olarak Dividag dişli vidalar DV15 ve DV20 kullanılmaktadır. Bağlantı çubuklarının büyük boyutlu rondelaları ve somunları, iyi yük dağılımı, vidaların taşıma kapasitesinin etkin kullanımı ve beton karışımının basıncına karşı güvenilir direnç sağlar.
NOE'den duvarlar ve kolonlar için katlanabilir kalıp.İnşaat ihtiyaçları için kalıp sistemi "NOE 2000" dört modifikasyonda üretilmiştir - 80 kN / m2'ye kadar bir yük için tasarlanmış çelik dahil gerekli herhangi bir kaplama ile ana çelik çerçeve kalıbı (Şekil 22.7) yüksekliği ile 3,31 m'ye kadar olan paneller ve 14,05 m2'ye kadar maksimum kalıp alanı kalkanı; çelik çerçeveli hafif sistem, vinçsiz kuruluma olanak tanır; özel olarak manuel çalışma için tasarlanmış bir alüminyum kalıp ve kolonlar için 125 kN/m2'ye kadar beton karışım basıncına izin veren evrensel bir kalıp. Perde kalıbı, dikey veya yatay olarak düzenlenmiş paneller ile farklı kombinasyonlarda monte edilebilir.
Çelik çerçeve kalıbının standart ölçüleri; eleman genişliği 265; 132.5; 125; 100; 75; 50 ve 25 cm; yükseklik 331; 300 ve 265 cm, güverte dönüşü 70...90 kez, çelik çerçeve - 500 devir. Hafif bir sistem için 530 ve 331 cm genişliğinde ve 265 yüksekliğinde elemanlar ek olarak uygulanabilir; 132,5 ve 66 cm.

Levhaların kaplaması, 265 x 530 cm boyutlarındaki levhalar için bile, her zaman tek parça olarak, ek ve uzantı olmadan yapılır.Bir güverte olarak, 21 ve 22 mm kalınlığında su geçirmez ahşap yapıştırılmış üç katmanlı levhalar veya yapısal ahşap levha gerekli kalınlıkta kullanılabilir; güverte her zaman arkadan kalkanlara takılır. Bu avantajlar, panellerin yüksek oranda değiştirilmesini, soyulmuş yüzeyin optimal bir görünümünü elde etmeyi mümkün kılar ve panellerin temizlenmesini basitleştirir. Çoğu zaman, huş ağacı, çift taraflı fenol kaplama uygulanmış toplam 21 mm kalınlığa sahip 15 kat halinde kalıp kaplaması için kullanılır.
Kalıp levhasının bağlama çerçevesindeki dış yekpare oluk levhaların her yerde birbirine bağlanmasına olanak sağlar. Panelleri tek bir kalıp paneline monte etmek için, sıradan bağlantılar için kama biçimli ve vidalı kelepçeler ve 25 cm genişliğe kadar ekleri olan panelleri tesviye etmek için uzun kelepçeler kullanılırken, eklemin ve tüm kalıp panelinin gücü azalmaz. Kalıbın tüm çelik elemanları, sadece görünümü iyileştirmekle kalmayıp aynı zamanda panellerin devrini artıran, betona yapışmayı önemli ölçüde azaltan sıcak daldırma galvanizli olmalıdır.
Saf çelik çerçeve kalıbı her zaman hacimli ve ağırdır. HOE Hafif Kalıp, çelik çerçevenin ekonomisini ve gücünü alüminyum takviyelerle birleştiren bir modeldir.
NOE alüminyum kalıbın 4 standart boyutu vardır - 90, 75, 50 ve 25 cm, ikisi yükseklik - 265 ve 132,5 cm, kalkan dönüşü 60 ... 80 kez, çerçeveler - 400 dönüş. Toplam kalınlığı 15 mm olan su geçirmez 9 katlı kontrplaktan yapılmış güverte ön tarafından perçinlenir, panellerin sıyrılmasını ve bakımını kolaylaştırmak için üstüne koruyucu bir tabaka püskürtülür. Kalıp hafiftir, manuel kuruluma izin verir; Gerekirse, NOE 2000 sistemi çerçevesinde başka tip ve modifikasyonlarda kalkanlar kullanılabilir. Ayrıca tüm köşe plakaları, tesviye elemanları ve diğer bağlantı elemanları aynıdır ve gerektiğinde kullanılabilir.
NOE şirketinin kolon kalıbı, genişliklerini 15 ila 150 cm arasında sorunsuz bir şekilde ayarlamanıza izin veren dört panelden (Şekil 22.8) oluşur, panellerin yüksekliği 300, 275, 100 ve 50 cm'dir, standart bağlantı elemanlarını kullanarak panelleri yüksekliğe bağlayın. Kalıp çerçevesi tamamen çeliktir, sağlam ve dayanıklıdır, levha kaplama isteğe bağlı olarak çok katlı, üç katlı kontrplak, levha veya 4 mm çelik sacdan yapılır. devir tahta döşeme 20...30 devirde, çelik çerçeve, çelik güverte dahil, 400 defaya kadar. Kalkanların cıvatalara veya özel üçgen plakalara bağlanması.

Utinor tarafından kalkan duvar kalıbı. Fransız şirketi "Utinor", üretiminde tanınmış bir liderdir. metal kalıp. Duvarlar, kolonlar, tavanlar, asansör boşlukları vb. için 4 mm çelik sac şeklinde bir kalıp yüzeyi ile çeşitli kalıp türleri geliştirilmiştir, bu ve rijit bir çerçeve sayesinde kalıbın mukavemeti önemli ölçüde arttırılmıştır. , standart kalıp cirosu 800 devirdir. Çoğu zaman, büyük panel kalıp duvarlar ve tavanlar, tünel kalıpları için kullanılır.
Şu anda Utinor, standart, katlanır ve konteyner kalıp olmak üzere üç model duvar kalıbı üretmektedir. Katlanır kalıp, standart panel kalıp ile konteyner kalıp arasında bir ara çözümdür.
Standart duvar kalıbı, 2.52 yüksekliğinde dikey panellerden oluşur; 2,60 ve 2,70 m ve 1,25 ila 6,25 m sette elemanlara sahip olmanızı sağlayan 1,25 m modül uzunluğu Kalıp panelleri, takviye elemanları ve yük taşıyıcı yapılar (kafesler) ile 3 veya 4 mm kalınlığında bir şekillendirme metal sacdan oluşur (kafesler) , kirişler), beton karışımından gelen kuvvetleri algılayan ve kalıbın gerekli stabilitesini ve ayar olasılığını sağlayan (Şekil 22.9).
Çift taraflı duvar oluşumu için iki kalıp paneli, “keçi” kaldırma yardımı ile “yüz yüze” pozisyonda birbirine sabitlenir, bu sayede her iki panelin stabilitesi gerekli süre boyunca sürekli olarak sağlanır. Sıyırma sırasında, her iki kalkan da asılır, bir vinç tarafından kaldırılır, tasarımları sayesinde "keçiler" kalkanları otomatik olarak ayırır.
Perde kalıbı yeni bir çalışma konumuna hareket ettirildiğinde, paneller birbirinden 1,1 m uzaklıkta sabit bir çalışma dışı konumdadır, bu da takviye kafeslerinin, diğer gömülü parçaların ve eklerin montajına izin verir. Betonlama için hazırlanırken, panellerin tasarım konumunda montajı ve sabitlenmesi özel geri çekilebilir silindirler kullanılarak gerçekleştirilir. Kalkanlar kuplörler (saplamalar) ile bağlanır ve üst kuplör beton seviyesinin üzerindedir ve alt kısım duvarın en tabanında bulunur. Duvarın betonlanmasından sonra başka hiçbir düzensizlik ve delik oluşmaz. Kalıbın üst kısmındaki kalıp panelleri (betonlu yapının kalınlığı) arasındaki gerekli mesafe, betonlama işlemi sırasında, alt kısımda, özel manivela cihazları yardımıyla, portal çerçeve yapısı tarafından belirlenir ve sağlanır.
Her duvar kalıbı, tabanda, istenen seviyeye ayarlamak için krikolar ve başında iki kaldırma braketi ile donatılmıştır. Beton karışımından gelen yükü taşıyan dikey kafes kirişler, 1.25 m'lik artışlarla (kalkan başına 3.75 m uzunluğunda 3 eleman) kalıp üzerine sabitlenir ve tüm kalıp panelini kesinlikle dikey olarak ayarlamak için tabanda bir kriko bulunur. Her duvar kalkanı, bir çalışma platformu ve bir merdiven ile donatılmıştır.
Metal kalıp, yüksek kaliteli bir şekillendirme yüzeyine sahiptir. İki duvar panosunun şekillendirici yüzeylerinin mükemmel bir şekilde birleştirilmesi, özel yönlendirme ve bağlantı kolları ve kilitleme pimleri ile sağlanır. Dişli bağlantılar (saplamalar), dağıtım plakaları ve kelebek somunlar, iki karşıt panelin rijit bir karşılıklı montajını sağlar ve kalıba dökülen beton karışımının basıncını algılar. Her bir kuplörün üzerine, iki karşıt duvar kalkanı arasındaki mesafeyi içeriden sağlam bir şekilde sabitleyen özel burçlar-ara parçaları konur, burçlar, kalkanın alt ve üst kısımlarındaki her bir kirişin altına yerleştirilir.
Dikilecek beton duvarın gerekli yüksekliğinin standart perde kalıbı yüksekliğini aşması durumunda, ana kalkanın üst kısmına yerleştirilen üst ek paneller kullanılır. 0,35 m'den fazla olmayan bir ekleme yüksekliği ile konumları, üzerine oturan vidalar kullanılarak ayarlanır. iç yüzey kalıp sertleştiriciler; 1 m'ye kadar olan uçlar için ayar vidalı özel stabilizatörler kullanılır. Ek elemanların yüksekliği 1 m'den fazla olduğunda, ana destek kirişlerine bağlanan özel ek kirişler kullanılır. Beton karışımının basıncından gelen tüm çabalar, ek elemanlardan ana kalıp panellerine aktarılır.

önemli bir unsur Yüksek kaliteli ve eş eksenli betonlama için dikey olarak bir yapının sıfır seviyesinde, 60 ... 100 mm yüksekliğinde uzatılmış donatı ile betonlanır. Bazalar, bodrumun üzerindeki döşeme plakaları ile aynı anda betonlanmalı, birinci katın zemini betonlanırken, ikinci katın duvarlarının kaideleri betonlanmalıdır.
Betonlama sonucunda elde edilen yüzeyler pratik olarak herhangi bir iyileştirme gerektirmez, çünkü bitirme işi miktarı önemli ölçüde azalır. Metal kalıp, doğrudan metal panellere manyetik kelepçelerle sabitlenen pencere, kapı ve diğer açıklıkların kullanılmasına izin verir, bu da pencere ve kapı çerçevelerinin ve çerçevelerinin bu açıklıklara hızlı ve verimli bir şekilde monte edilmesini mümkün kılar. Bu açıklıklar rijit olabilir ve belirli boyutlarda üretilebilir veya geri çekilebilir ve farklı boyutlarda kullanılabilir. Bu durumda otomatik olarak içine yerleştirilmiş olan pencere ve kapı çerçevelerini hemen içerebilirler. betonarme yapı veya aynı pencere ve kapı çerçevelerinin daha sonra monte edileceği açıklıkları belirtin.
Önceden monte edilmiş kalıbı çıkarmak ve yeni bir işyerine kurmak özellikle zor değildir. Önceden betonlanmış duvarın soyulması sırasında, açma kalıplarının vida bağları ve vidaları çıkarılır, kafes kirişlerin krikoları gevşetilir, duvarların uç kesimleri çıkarılır ve kalıp panelleri ayrılır (birbirinden itilir), daha sonra sonraki kavrama taşındı.
Bireysel kalkanların kalıplarının sökülmesi, ön zayıflamalarından sonra kafes krikolarının çıkarılmasıyla başlar, ardından kalkanlar beton yüzeyden ayrılır, geriye yaslanır, ancak "keçiler" sayesinde gerekli stabiliteyi korurlar. Sıyırma işleminden sonra çalışma yüzeyi bir su jeti ile durulanmalı, bir sıyırıcı ile temizlenmeli ve özel yağ ile yağlanmalıdır. Kalıp, halihazırda betonlanmış kaidenin üzerinde yeni bir yere kurulur. Kalkanın üzerine doğru yerlerde, gerekli tüm açma kalıpları monte edilir, önceden betonlanmış duvarlardan çıkarılır; elektrikçilerden oluşan bir ekip bağlantı kutularını yerleştirir, kalıbı açar ve kablolama işlemini gerçekleştirir. Takviye işçileri, birbirine ve tabandan serbest bırakılan takviye çubuklarına bağlayan takviye ağları ve çerçeveleri kurar. Daha sonra kalıp panelleri bazaya bastırılır, birbirine bağlanır ve krikolar yardımıyla dikey ve yatay olarak hizalanır. Bundan sonra vida bağları takılır, üzerlerine burçlar konur, kalkanlar son olarak tabana yakın çekilir ve vida bağları yardımıyla sıkılır.
Kalıbın yataylığı ve dikeyliği ayarlandıktan sonra kalıbın son konumu sabitlenir. Kalıp montajının son aşamasında, duvarların uçları, ayarlandıktan sonra kalıbın kenarları boyunca sağlam bir şekilde sabitlenen kesimlerle kapatılır.
Standart perde kalıplarında, yeni bir şantiyeye taşınırken, menteşeli platformların, takviye kirişlerinin ve diğer çerçeve elemanlarının sökülmesi gerekir. Katlanır kalıp, nakliye sırasında boyutlarını önemli ölçüde küçültmeyi mümkün kılan döner ve yana katlanır alet elemanları ile donatılmıştır.
Utinor'dan konteyner duvar kalıbı. Standart 2.52 ve 2.60 m kalıp kombinasyonları için 1.25 ve 2.5 m uzunluğunda modüler versiyonda üretilmektedir. Kalıp çerçevesinin takviye nervürleri, 15 cm nervür aralığına sahip bir keson şeklinde tasarlanmıştır, bu da 4 mm kalınlığında bir şekillendirme levhasından yapılmış güverteye artan sertlik ve mukavemeti garanti eder. Kalıbın tüm köşeleri, paneller arasındaki bağlantının ana unsuru olan özel konteyner kilitleri ile donatılmıştır. Bu kilitler sayesinde paneller deformasyonlardan iyi korunur, bitişik paneller özel vida bağları sıkılarak bağlanır. Aynı zamanda bağlı kalıp panellerinin kenetlenmesi ve hizalanması ek ayar yapılmadan garanti edilir.
Konteyner duvar kalıbı tamamen katlanır: çalışma platformu (platform ve çit) ve stabilizasyon payandaları nakliye sırasında sökülmez.
Utinor metal kalıbın önemli bir avantajı, yükseklik, genişlik ve uzunluk olarak dönüştürülebilmesi, yani farklı duvar kalınlıkları, zemin yükseklikleri ve 8,2 m'ye kadar açıklıklar ile çeşitli projelerde kullanılabilmesidir.Utinor teknolojisini kullanarak. , büyük panel konstrüksiyona kıyasla inşaat maliyetini %30'a kadar azaltmak mümkündür ve yüksek hızlı ve yıl boyu yapılan çalışmalarla inşaat süresini kısaltmak mümkündür.
Kalıp sistemi "Kaplock"."Kaplock" kalıp sistemi İngiltere'de geliştirilmiştir, evrenseldir, duvar ve tavan kalıplarında, köprülerin, tünellerin ve diğer yüksek yapıların destekleyici bir parçası olarak ve kullanımı kolay bir iskele sistemi olarak kullanılabilir. dış ve iç çeşitli yapıları bitirmek için.
2,7 ve 1,5 m yüksekliğinde (şekil 22.10), 18 mm kalınlığında lamine kontrplak güverte ile 6 kPa'ya kadar yanal beton karışım basıncı için tasarlanmış iki tip perde kalıbı paneli sunulmaktadır.
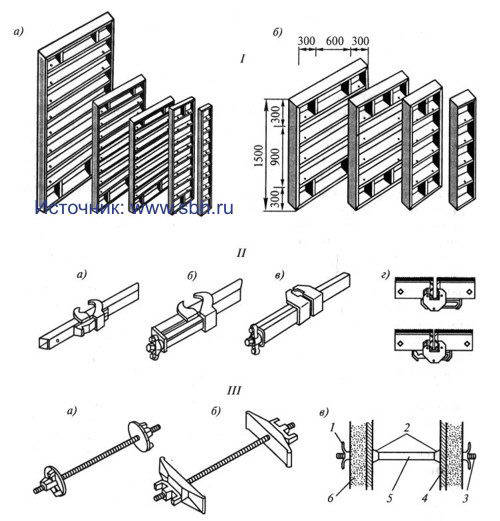
Tablo 22.3. Pano kalıp sistemi "Kaplock"
Kalkan boyutu, mm |
Ağırlık (kg |
Kalkan boyutu, mm |
Ağırlık (kg |
Panellerin (Tablo 22.3) ve kalıp sisteminin diğer tüm elemanlarının birden fazla devrini sağlamak için, metal parçaları, daha fazla kaplama sağlayan derin sıcak galvanizlemeye tabi tutulur. Yüksek kalite geleneksel boya galvanizlemeden daha iyidir. Kaplamanın kalitesi, 5...6 yıl boyunca korozyona ve mekanik hasara karşı yüksek direnci garanti eder. Kolaylık, bağlantı kolaylığı ve elemanların sabitlenmesi, kaplamanın dayanıklılığına katkıda bulunur ve bakım maliyetlerini azaltır.
Kalkanları kalıp paneline bağlamak için, çalışma sırasında daha uygun ve yukarıdan dövülmüş metal pimlerden daha güvenilir olan yandan kilitlemeli orijinal kilitler geliştirilmiştir. Özel uygulamaya bağlı olarak kilitlerin birkaç çeşidi vardır: eksantrik kilit ve yan kelebek somunlu iki tip uzun kilit.
Vidalı bağların, üst yüzleri boyunca karşılıklı panelleri bağlamanıza izin veren bağlar ve betonarme yapının kesitinin incelmesini önleyen ekler (ara parçalar) içeren bağlar dahil olmak üzere üç çeşidi olan kendi ayırt edici özellikleri vardır.
Makale şirket tarafından dijital olarak hazırlanmış ve gönderilmiştir.
3.2. Zemin kalıbı
Kirişli tavan kalıbını kurarken, çalışma sırası aşağıdaki gibi olacaktır (Şekil 22.11). Önce kolonların donatı kafesi kurulur, daha sonra kolonların kalıbı vida bağları veya kelepçelerle sabitlenerek ve 2 ... 3 seviyede parantez ile sabitlenerek monte edilir. Üstteki yapılarla arayüz oluşturmak için kolonların takviyesi, kalıbın üst kenarının 40 ... 50 cm yukarısından serbest bırakılır ve ardından kolonlar betonlanır. Bundan sonra, kirişlerin veya kirişlerin tabanının kalkanları, kolonların kalıbındaki özel oyuklara döşenir, altlarına destekleyici teleskopik raflar veya uzaysal destekler monte edilir ve yükseklikleri ayarlanır. Mekansal sertlik için raflar tripodlara monte edilmiştir. Kirişlerin kalıbının yan panelleri monte edildikten ve yatay vida bağları ile birbirine bağlandıktan sonra alt kalkana sabitlenir. Bir sonraki aşamada, ikincil ahşap kirişlerin altına raflar monte edilir, üzerlerine neme dayanıklı bir kontrplak güverte yayılır.
Takviye kafesleri ve ağları döşendikten sonra, iç kablolama için boruların döşenmesi, betonlama gerçekleştirilir. Kalıp sökme işleminin betonun sıyrılma mukavemeti kazandıktan sonra ve kalıp montajının tersi sırayla yapılması tavsiye edilir.
Yerli kalıplar arasında TsNIIOMTP Enstitüsü tarafından geliştirilen birleşik kalıp en yaygın olanıdır. Duvar kalıbı, 300 ila 1800 mm modüler genişliğe sahip bir kat yüksekliğindeki levhaların yanı sıra ek levhalardan - uç ve köşeden oluşur. Kalkan metal bir güverte, yatay kirişler ve dikey makaslardan oluşur. Kalkanların alt kısmında vidalı krikolar bulunur. Kalıpta 3 m yüksekliğe kadar 12, 16 ve 20 cm kalınlığında beton duvarlar ve 10 ... 22 cm kalınlığında tavanlar yapmak mümkündür.
Duvarlar dikildikten ve gerekli ilk mukavemeti kazandıktan sonra yekpare bir tavan düzenlenir. Döşeme kalıbı teleskopik payandalara monte edilir, iki kademede donatı ağları döşenir ve betonlama yapılır.

Büyük panel kalıp için, "masa kalıbı" olarak adlandırılan evrensel bir döşeme kalıbı geliştirilmiştir. 12 m'ye kadar kalkan uzunluğuna, 5,6 m'ye kadar genişliğe ve 1,75 ila 10 m park seviyesinden yüksekliğe sahip kalıp montajını mümkün kılan bir dizi modüler elemandan oluşur.Kalıp azaltılarak çıkarılır. masa desteklerinin yüksekliği. Daha sonra, kalıp tavanın altından açılır ve başka bir yere yeniden düzenlenir. Kurulum ve yeniden düzenleme, bir "ördek burnu" traversi ile gerçekleştirilir.
Şu anda, TsNIIOMTP Enstitüsü'nde geliştirilen, duvarlar ve tavanlar için alüminyum alaşımlardan yapılmış, katlanabilir-ayarlanabilir geniş panelli bir kalıp geliştirilmiş ve uygulama bulmuştur. Bu kalıbın amacı, kapsamı ve tasarımı, "İnşaat süreçleri teknolojisi" yazarlarının ders kitabında ayrıntılı olarak tartışılmaktadır (Bölüm 2. - M: Yüksekokul, 2003.).
Thyssen tarafından Sompakt kalıp(Şek. 22.12). Herhangi bir uzunluk, genişlik ve kalınlıktaki zeminler için kalıp düzenlemenizi sağlar. Bu, kalıbın tüm bileşenlerinin birbirine oturması, önemli mukavemet ve dayanıklılığa sahip olması nedeniyle elde edilir. Genel olarak, kalıp aşağıdaki yük taşıyıcı elemanlardan oluşur: Her türlü zeminin montajı için uygulanabilen H20 kompakt kirişler; basit çelik direklere sahip uzatılabilir tripodlar, kolay kalıptan çıkarmak için uzatılabilir çubuklar ve çıkarılabilir başlıklar (çatal ve destek) ve sadece bu direği 10 cm'ye kadar indirmek için “düşen” bir başlık.
Kalıp montajı aşağıdaki sırayla gerçekleştirilir. "Düşen" olanlar da dahil olmak üzere çıkarılabilir kafalar yukarıdan raflara monte edilir, raflar tasarım konumunda sabitlenir ve tripodu uzatarak gerekli mekansal stabiliteyi alırlar. Rulman boyuna kirişler, enine kirişlerin yerleştirildiği, kalkanların veya basitçe kalıp levhalarının üstüne yerleştirildiği rafların çıkarılabilir kafalarına monte edilir. Sıyırma için, “düşen” kafalar aşağı indirilir (6 ... 10 cm'ye kadar farklı modifikasyonlar için), sonuç olarak, tüm kalıp sistemi biraz sarkar. Bireysel boyuna ve enine kirişleri serbest bırakmak ve gerekirse kalıp panellerini çıkarmak nispeten basit bir şekilde mümkün hale gelir. Daha sık olarak, zeminin beton yapısının betonu yeterli güce ulaştıktan sonra, ara rafları kalıbın altından çıkarmak için “düşen” kafaların indirilmesi kullanılır.
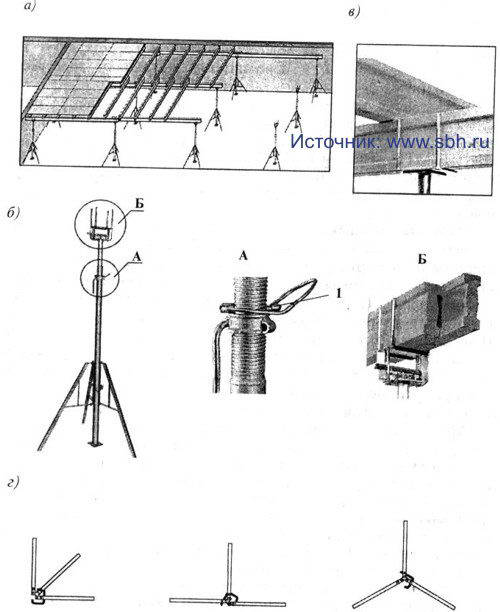
Kalıp sisteminin bir özelliği, rafın ayrılabilir kafasının, bu kafa boyunca kolayca hareket ettirilebilen iki örtüşen kirişi aynı anda tutabilmesidir, böylece tasarım, plandaki kalıbın herhangi bir şekline uygulanabilir. Kendi içinde stabil olan raflar-tripodlar ve bunların yanında bulunan boyuna ve enine kirişler, algılayacakları yükün gereksinimlerine karşılık gelen mesafelerde yerleştirilebilir. Önemli yükler için mesafeler daha kısa olmalıdır; daha ince döşemeler ve daha düşük kalıp yükleri için, dikmeler ve havai kirişler arasındaki mesafeler artırılabilir.
Bu kalıp sistemi H20 ahşap kirişler kullanır. Yüksek mukavemetli kuzey ladin ağacından yapılmışlardır, "dışbükey" kenarlara ve oldukça geniş ve sabit kayışlara sahip bir I-kiriş şekline sahiptirler. Bu kompakt şekil, kirişi güçlü ve kararlı hale getirirken, beş katmanlı birleştirme genel sertliği önemli ölçüde artırır. Kiriş, kenarlara çivi çakılsa bile bölünmez. Gerekirse, herhangi bir yerde, hatta eğik olarak bile kesilebilir, bu da mukavemet özelliklerini düşürmez. Kiriş düşerken deforme olmaz, aşınmaya çok az maruz kalır, emprenye onu çürümeye karşı korur. Ahşap kirişler nispeten hafiftir ve iki kişi tarafından manuel olarak kurulabilir. Kirişlerin enine kesiti, eğilmelerini ve doğru yere monte edilmesini kolaylaştırır. Bu tür çalışmalarda metal olanlara kıyasla daha kolay, daha kolay ve dolayısıyla çalışması daha hızlıdır.
Kalıp sistemi "Meva Dek". Yatay yapılar ve tavanlar için tasarlanmıştır. Bu sistemin ana avantajı, bilinen tüm yatay kalıp teknolojilerini kullanmasıdır, bu da dört farklı kalıp sistemi oluşturmayı mümkün kılar.
Bu sistemlerin kombinasyonu, her bir özel durum için, yüzey yenileme yüzeyini en aza indirmeyi mümkün kılar ve "düşenler" dahil olmak üzere çıkarılabilir kafaları olan dikmelerin kullanılması, hızlandırılmış bir soyma seçeneği ile yalnızca ayrı ara dikmelerin bırakılmasını mümkün kılar, bu da önemli ölçüde zaman ve para tasarrufu sağlar.

Yaygın kullanım, evrensel bir kalıp sistemi oluştururken, bir ana ve ikincil kiriş sisteminin “düşen” bir kafasına sahip metal raflara monte edilmek üzere tasarlanmış ahşap yapıştırılmış bir kiriş H20 bulmuştur (Şekil 22.13). Kirişlerin standart ölçüleri (20 cm yükseklikte) 250, 330, 390 ve 450 mm'dir, talep üzerine diğer ölçülerde kirişler yapılabilir.
Döşeme kalıp sistemi "NOE"
1. Ana kirişlerden ve kalıp panellerinden kalıp. Alüminyum alaşımlarından yapılmış taşıyıcı elemanlara sahip döşeme kalıp sistemi uygulama bulmuştur. Sistem, "düşen" başlıklı dikmelerden, tavan kirişlerinden ve kalıp panellerinden oluşur (Şekil 22.14). Kalıp panelleri 150 ve 120 cm uzunluğunda ve 90 ila 30 cm genişliğindedir (15 cm basamak). Desteklerin eksenleri boyunca boyuna tavan kirişleri 300, 210, 180, 150 ve 120 cm boyutlarında olabilir, “düşen” kafa 36 cm yüksekliğinde galvanizli çeliktir, gerekirse başı 17 cm'ye kadar düşürür . kalkanlar.
Aynı döner kafalı kalıp sistemi, kalıp kapağının serbestçe seçilmesine izin verir. Tasarım, damlalı veya döşeme yapısının güçlü bir şekilde bölünmesine sahip döşemeler için geçerlidir. “Düşen” veya döner başlı standart raflarda, aynı boyutlarda uzunlamasına kirişler (yukarıya bakın) ve alt kirişler boyunca enine kirişler döşenir. Çözüm, kalıp kapağını özgürce seçmenize olanak tanır. Enine kirişlerin montajına bağlı olarak, kalıp (panjur levhaları veya paneller) hem uzunlamasına kirişler arasına hem de üzerlerine döşenebilir.
2. Kayar ikincil kirişli kalıp. Alüminyum kalıp ile uyumlu "NOE" şirketinin (Şekil 22.15) tavan şeklindeki sistemi, daha da geliştirilmesi ve iyileştirilmesidir. "Düşen" başlıklı raflar, desteklerin bükülme anı olmadan tek taraflı yüklemede bile yükü çatı panellerinden alır. İkincil kirişler - 100 ila 150 cm arasında kayar, teleskopik tip. Bir seçenek olarak, ana kirişlerin flanşları üzerinde doğrudan desteklenen büyük boyutlu panellerden oluşan şekillendirilmiş bir sistem uygulanabilir, bu da panellerin kolay montajını ve sökülmesini sağlar. Levha yelpazesi, 15 ve 30 cm'lik bir eğime sahiptir, bu da kalıbın minimum ilavelerle odanın tüm alanına en uygun şekilde yayılmasını mümkün kılar. Tasarım çözümü, duvara sıkıca oturmanıza ve onunla güvenli bir şekilde sabitlemenize olanak tanır. Gerekirse, gerekli direk sayısını önemli ölçüde azaltan ve kalıp tavan panellerinin altına kurulum sürecini basitleştiren 3 m uzunluğunda uzunlamasına kirişler kullanmak mümkündür.


3. Düşen başlıklı tavan kalıbı. Bu çözüm evrenseldir, "düşen" başlıklı bir tavan kalıbı ve uzunlamasına kirişler ve tavan panellerinden oluşan bir destek sistemi içerir (Şekil 22.16). Kirişler, destek direklerinin geri çekilebilir çubuklarının kafalarına önceden takılmış olan "düşen" kafalara monte edilir. "Düşen" kafalarda, yatak traversleri sıkıştırılır, rafların tripodları, traverslerin montajı sırasında stabilite sağlar. Kalıp panelleri, kalıbın monte edilmiş destek yapısı üzerine serilir, döşeme hem boyuna hem de enine yönlerde hızlı bir şekilde gerçekleştirilir. Bu çözümün avantajı, erken sıyırma olasılığıdır ve "düşen" kafalı raflar, soyulmuş tavanı sürekli olarak destekler. Kaldırılan kalıp panelleri, bu sırada yedek destekler üzerindeki bitişik kavrama üzerine monte edilebilir.

4. H20 kirişli kalıp. H20 ahşap kirişler NOE firmasının kalıp sisteminde yaygın olarak kullanılmaktadır. Tüm sistem oluşur ahşap kirişler, çatal başları, standart destekler ve tripodlar ve kalkanlar veya kontrplak levhalar şeklinde kaplama (Şek. 22.17). Kalıp manuel olarak kurulur. Özellikle kapalı alanlar için uygundur. Bu sistemin dezavantajı, kirişlerin (50 dönüşe kadar) ve kalkanların (20 dönüşe kadar) azaltılmış devridir.
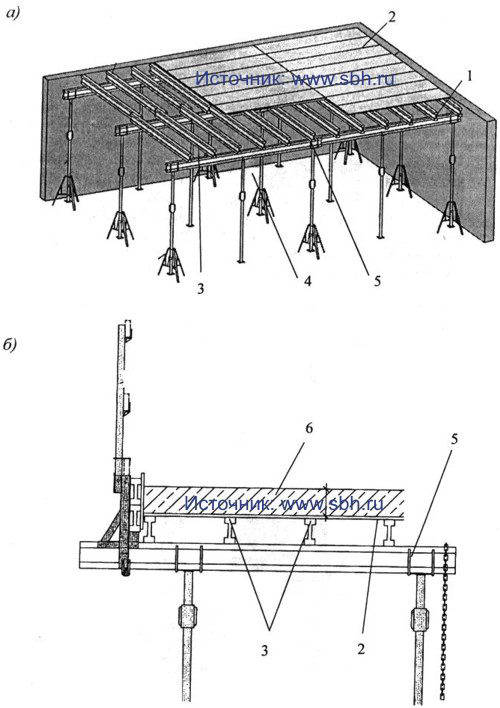
Döşemeler için Dally kalıbı. Yapıcı kalıp çözümü gelenekseldir - kayar raflar, üst raflarda kalıp panellerinin döşendiği H20 ahşap yapıştırılmış kirişler, duvarlar için tasarlanmıştır ve ayrıca benzer boyutlarda özel paneller (ancak sadece 132 ve 88 cm uzunluğunda) (Şek. 22.18). 1,5...3 değişken uzunlukta üç standart boyuttaki raflar; 2...3.5 ve 2.3...4.1 m, H20 kirişler standart boyutlar, sıyırma için, kayar raflara “düşen” kafalı U şeklinde bir kiriş tutucu monte edilmiştir.

Utinor tarafından üretilen döşeme kalıbı. Firma "Utinor", beton zeminler için kalıp için üç bağımsız seçenek sunar: geçici ara desteklerin varlığında sadece kendi ağırlıklarına değil, aynı zamanda döşenen ağırlığına da dayanabilen kendinden destekli elemanlardan yapılmış çıkarılabilir olmayan kalıp beton karışımı; vinçsiz kurulum ve kalıplama masaları için küçük panel kalıp.
Makale şirket tarafından dijital olarak hazırlanmış ve gönderilmiştir.
Küçük panel kalıp üç ana eleman içerir: üstüne sabitlenmiş çatal başlı standart bir direk, metal profil kiriş ve çelik çerçeve ve lamine kontrplak levhadan oluşan paneller. Kayar raflar, zemin yüksekliği 2 ila 5,2 m olan odalar için kalıp kullanmayı mümkün kılar 1.0 ve 1,6 m uzunluğundaki yatak kirişleri, gerekirse bunları 0,6 ... 0,9 m, 30 ve 60 cm genişliğinde ve 0,9 oranında artırmaya izin verir. 1,5 m uzunluğa kadar (en ağır kalıp elemanı 26 kg ağırlığındadır). Panellerin ve kirişlerin sökülmesinden sonra, betonarme döşeme, çatal, destek ve düşme başlıklı standart raflar kullanılarak desteklenir.
Standart şekillendirme tablosu firma "Utinor". Tablonun tasarımı, 2 ila 2,5 m'lik bir oda yüksekliğinde ve 1,9 ila 6 m'lik bir aralıkta kullanılmasına izin verir.Çalışma yüzeyi, 3 mm kalınlığında bir metal levha veya büyük boyutlu kontrplak levhalar 18 şeklinde yapılır. ..21 mm kalınlığında. Masa, masa çerçevesinin uzunlamasına kirişlerine monte edilmiş kayar enine kirişlerden oluşur. Metal kapak, kayar kirişlere kaynaklı takviyeler, kontrplak - braketler ve havşa başlı cıvatalarla tutturulmuştur.
Kafes boyuna ve çapraz kirişler V şekli 60 cm'lik artışlarla 1,2 ila 5,4 m uzunluğa sahiptir, bu da 6 m'ye kadar açıklığa sahip bir güverte elde etmenizi sağlar. Her bir destek ayağı, kalıbı açıklık boyunca hareket ettirmek için 690 mm stroklu manuel olarak çalıştırılan bir vidalı kriko ve 200 mm çapında bir tekerlek ile donatılmıştır.
İlk olarak, destek ayaklarındaki vidalı krikolar yardımıyla ve duvarların üst kısmındaki referans işaretlerinin seviyesine göre tabla yüksekliği ayarlanır, yan boşluk sıyırma rayları ayarlanır (kalıp boyutlarını gösterirler. odanın çevresi) ve daha sonra açma kalıpları, elektrikli ekipman ve kablo tesisatı kurulur, gerekli iletişim döşenir ve takviye ağları döşenir.
Masanın her iki yanına sıyırma rayları monte edilmiştir. Masa ve bitişik duvarlar arasında kurulum sırasında oluşan boşluğu seçmenize ve beton sertleştikten sonra şekillendirme tablasını kolayca indirmenize izin verir. Masanın sökülmesi, yerçekimi etkisi altında ve yalnızca destek ayakları ve krikolar indirilirken onların yardımıyla oluşturulan 30 ... 40 cm'lik masa ile zeminin tabanı arasındaki boşluk nedeniyle gerçekleştirilir. sonraki uzatma ve yeniden düzenleme için levhanın kenarına yuvarlamak kolaydır. Aynı zamanda, henüz mukavemet kazanmamış beton levhayı desteklemek için serbest bırakılan açıklıkta geçici destek direkleri kurulur.
İkinci katın zeminlerini betonlarken, yükü birinci katın döşeme levhasına aktaran, masaları kaldırmak için sıyırma platformları veya konsol iskeleleri kullanılmalıdır. Bir vinçle tabloları çıkarmak için çeşitli seçenekler vardır. Masa, levhanın devamı olarak hizmet veren iskeleler üzerine yuvarlanabilir ve dört kollu bir askı kullanılarak bir vinç ile onlardan kaldırılabilir. Masa, özel bir travers veya dengeleme cihazı kullanılarak vinçle ve iskele olmadan da kaldırılabilir.
Düşük (ancak negatif olmayan) sıcaklıklarda, ekzotermik ısı nedeniyle betonun sıcaklığını korumak, sertleşmesini hızlandırmak için beton levhanın hafif bir örtü ile kaplanması tavsiye edilir. ısı yalıtım malzemesi polistiren türü. saat Yüksek sıcaklık ortam havası, aksine, betonun akşam geç saatlerde yapılması ve sabahları betonun çatlamasını önlemek için masa hareket edene kadar tavana su dökülmesi tavsiye edilir.
Tavan kalıbı "Kaplock". Kaplok destek sistemi şu anda mevcut olan en dayanıklı ve çok yönlü yük taşıma sistemlerinden biridir. Önemli bir özellik sistem, teleskopik rafların bütünlüğü değil, tek tek elemanlardan istenen yüksekliğe montajıdır.
Raflar iki çeşitte tasarlanmıştır - burçsuz ve burçlu bağlantılar (Şekil 22.19). Raflar, boylarına bağlı olarak 2...6 fincan bağlantılarına sahiptir, fincanlar 50 cm uzunluğunda raflara kaynaklanır. Kolsuz bağlantı rafları bağımsız olarak kullanılabilir, üzerlerine vidalı krikolar sabitlenebilir. Burç bağlantı rafları, burçsuz raflarla birlikte kullanılır, diğer raflarla dikey bağlantı için 150 mm uzunluğunda burçları vardır. Kilitleme pimleri veya dübeller üzerinde rafların birbirine ek olarak sabitlenmesi için delikler sağlanmıştır.
Her bağlantı iki kaptan oluşur, üst, hareketli, kapak şeklinde, güvenliğine ve dayanıklılığına katkıda bulunan dövülebilir dökümden yapılmıştır. Belirli bir yüksekliğe (50 cm'lik artışlarla) sabitlenen alt kap, dışta bir kase şeklinde yapılır ve içinde yatay bağları yerleştirmek için dört özel deliğe sahiptir. Rafların tasarımı, karşılıklı olarak gerekli yüksekliğe kadar uzanmalarına izin verir. 3,2 mm et kalınlığına sahip yüksek mukavemetli çelikten yapılmış raf boruları, tüm sistemi önemli ölçüde hafifletmeyi mümkün kılarken, bir raftaki yük 64 kN'ye ulaşabilir.
Raf seti, 110 mm yüksekliğinde kaynaklı bir boruya sahip bir destek içerir. Destek, rafın alt kısmında taban (topuk) ve üst kısımda kafa olarak kullanılabilir. Rafların üst kısmı için, kirişleri birbirine yakın (150 mm çatal genişliğinde) veya açısal ofset (200 mm çatal genişliğinde) kurmak için ahşap, çelik veya alüminyumdan yapılmış sabit çatallar kullanılır. . "Düşen" bir kafa ve sallanan bir çatal, raflarda bir veya iki yönde kırılma olduğunda kullanılan uygulama buldu. Önemli bir bileşen evrensel bir vidalı krikodur, rafların üst ve alt kısımlarında kullanımı mümkündür. Bir kaplinli iki tip vidalı kriko vardır - eleman uzunluğu 400 mm, kesimi 250 mm, eleman uzunluğu 860 mm, kesim 620 mm'ye çıkar. Krikolar hassas ayar için tasarlanmıştır destek sistemiÇatal veya topuk ile bağlantılı olarak kullanılan, fincan ekleminin boşluğuna sabitlenir. Gerekli yatay ve çapraz bağları kurarken belirli bir yük için tasarlanmıştır.

Yatay bağlantılar 600, 900...1300 (100 mm'lik adımlarla), 1600, 1800 ve 2500 mm uzunluğa sahiptir. Bu bağlantılar, rafların projenin ihtiyacına göre 60 ila 250 cm mesafeye yerleştirilmesini sağlar, rafların üzerine yerleştirilebilirler. farklı seviyeler yükseklikte, tüm destek sistemine mekansal sertlik sağlar. Yatay ve raflar gerektiğinde hızlı bağlantı ve bağlantı kesme iskelesi olarak kullanılabilir. Her yatayın uçlarında, yüksek mukavemetli dövme bir ağızlık (sınırlayıcı) ve rafların alt bardaklarının özel deliğine sağlam bir şekilde dahil edilen özel bir tasarım bulunur.
Orijinal bir eleman bağlantısına sahip olan "Kaplock" sistemi, çerçevenin düğümler halinde hızlı bir şekilde monte edilmesini sağlar. Yatay elemanların düğüm montaj yöntemi, rafların alt bardaklarındaki desteklere ön kurulumlarına dayanır, bu tür dört eleman olabilir. Üst çanak, mafsalda kurulu yatay bağlantıların limit anahtarlarına indirilirken, bu limit anahtarlarını rijit bir şekilde yakalar ve bir çekiç darbesi ile sabitlenerek rijit bir bağlantı oluşturur. Aynı seviyedeki bu tür bir yatay eleman eklemi uygundur, komple montaj basitleştirilir ve montajdaki gerilmeler azaltılır. Destek sisteminin avantajı da cıvata, takoz, somun olmadan çözülmesidir.
Çerçevenin taşıyıcı alüminyum kirişleri (Şekil 22.20, Tablo 22.4), yatak yüküne ve kaplanacak açıklığa bağlı olarak üç çeşittir.
Tablo 22.4. "Kaplock" çerçeve sisteminin kirişleri
Kiriş T150 |
Kiriş T225 |
||||||||||
Ağırlık (kg |
Ağırlık (kg |
Ağırlık (kg |
Ağırlık (kg |
Ağırlık (kg |
Ağırlık (kg |
||||||
İskeleyi sabitlemek, zemin kalıbının taşıyıcı ve ikincil kirişlerini kurmak için seçenekler, Şek. 22.20, II. Destek-kalıp sisteminin önemli bir avantajı, yapıcı çözümün basitliği ve hızlı montaj ve demontaj imkanıdır. Takılan krikonun çalışma aralığı 620 mm'dir (diğer kalıp sistemlerinde - 100...200 mm), arasındaki mesafe destek gönderileriönemli ölçüde değişebilir. Sistem, tüm çerçevenin vinçsiz montajı için tasarlanmıştır; ahşap ekleri olan yük taşıyan alüminyum kirişler, uygun ve teknolojik olarak gelişmiş olup, kütle ile 7,5 m'ye kadar çerçeve kolonları arasında bir mesafeye izin verir. taşıyıcı kiriş kalıp 67 kg. Kirişlerde ahşap eklerin varlığı, çeşitli tasarımlardaki kontrplak levhaların ve kalıp panellerinin güvertesinin güvenilir şekilde sabitlenmesini sağlar. Çeşitli kalıp sistemlerinin ön karşılaştırması için, şek. 22.21, zeminler için kalıp montajı için belirli işçilik maliyetlerinin dağılımını gösterir.
Makale şirket tarafından dijital olarak hazırlanmış ve gönderilmiştir.
